Work equipment can pose a variety of hazards, such as mechanical, electrical, chemical, and others. Operators must be well-informed about the specific risks associated with laboratory equipment and undergo comprehensive training to ensure its safe and proper use.
Responsibilities: as defined in EPFL LEX 1.5.1 (Article 12), the head of unit ensures compliance with occupational health and safety rules within their team, and approves the purchase and installation of work equipment in laboratories or workshops.
Standard: set of rules or specifications established to ensure safety and minimize risks, with SN, EN, and ISO representing national (Swiss), European, and international bodies responsible for developing these standards to guarantee product safety and quality.
Declaration of conformity: document drawn up by the manufacturer or their authorized representative certifying that the work equipment complies with the European and Swiss safety requirements necessary for it to be marketed, including for personal protective equipment (PPE).
Example of declaration of conformity :
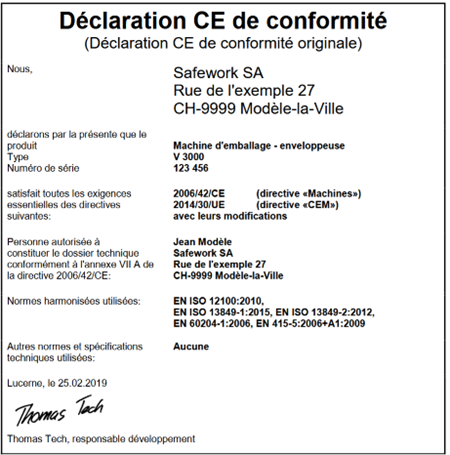
CE certification: it stands for “Conformité Européenne” and it certifies that the product complies with the essential safety, health and environmental protection requirements defined by European legislation. This involves the intervention of a certification body, which will issue a certificate after assessing the equipment’s compliance with the current standard.
European conformity and China Export: the CE logo for compliance with European standards is very similar to the China Export logo, which does not represent any form of official certification or compliance with European Union standards.
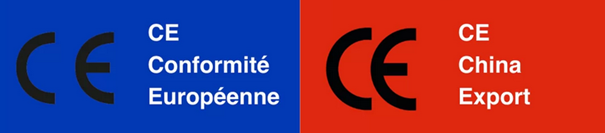
This marking can be misleading, and the China Export marking can give the impression that a product has received CE (Conformité Européenne) certification when this is not the case.
In case of doubt, the declaration of conformity will indicate the standards to which the work equipment conforms, while the CE (Conformité Européenne) certification should also be mentioned in the user manual for the equipment concerned.
The safety of work equipment begins with the purchasing process. All equipment installed in a laboratory or workshop must comply with legal safety requirements. The EPFL’s Occupational Health and Safety Service (OHS) requires all work equipment to have a declaration of conformity to Swiss (SN), European (EN) or international safety standards (ISO), or a CE certification.
When purchasing equipment, a specifications document defining the following points must be established:
• What function must the work equipment fulfill?
• Where is the installation to be located (evacuation routes, logistics paths, ground resistance)?
• How is the installation to be set up and used?
• How should maintenance and repairs be carried out?
• What is the noise (sound emissions) and vibration level of the work equipment?
• Is the equipment explosion-proof?
• Are any harmful substances released?
In addition, the work equipment must be supplied with a declaration of conformity (or equivalent document for equipment from outside Switzerland and European Union) and a user manual written in the user’s own language.
The user manual must include :
• Instructions for using the equipment in accordance with its intended use, as well as assembly instructions for partially assembled machines.
• Information on the personal protective equipment that must be worn when using the equipment. The corresponding pictograms must be displayed on the equipment.
• Information on equipment maintenance.
• Information on the specific training that users must undergo.
• Information on installation, commissioning, description of normal use, as well as contraindications, residual risks and troubleshooting, based on experience.
Like new work equipment, second-hand work equipment must meet the essential health and safety requirements. The head of unit must ensure that a declaration of conformity and a user manual are available. In the absence of these two documents, an approved certification body must assess the work equipment in question.
Page under construction
Following the reception of work equipment, the following steps must be carried out:
• Verification of the presence of the declaration of conformity and the user manual.
• Inspection of the equipment for any visible defects.
• Identification of an appropriate location for the equipment. The installation must not create new hazards, and the load-bearing capacity of the floor must be respected.
• Verification of the presence and proper functioning of safety devices (e.g., safety lock or interlock).
• Verification of the availability of necessary personal protective equipment and the display of corresponding pictograms on the equipment.
• Organization of maintenance for the work equipment.
• Identification of any foreseeable incorrect usage.
• Organization of specific training if the equipment requires special instructions for users.
• Identification of residual risks (risks remaining after implementing all safety measures).
Page under construction
Specific work equipment
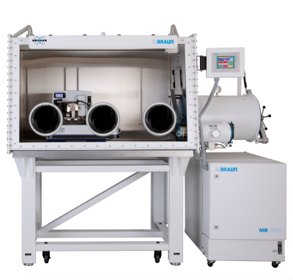
Gloveboxes
Guidelines and best practices for the use and maintenance of gloveboxes at EPFL
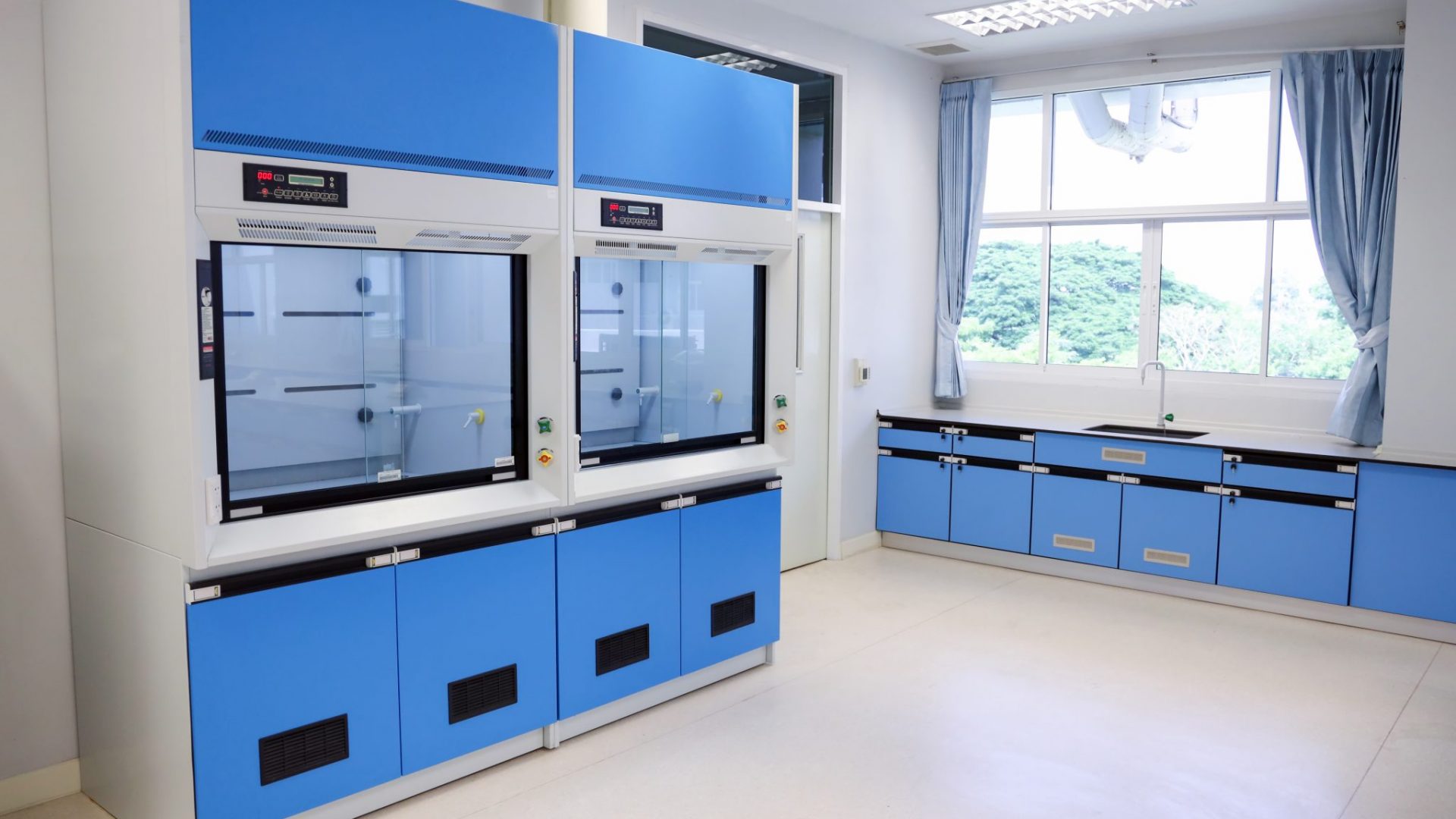
Laboratory fume hoods
Use and good practice of laboratory fume hoods
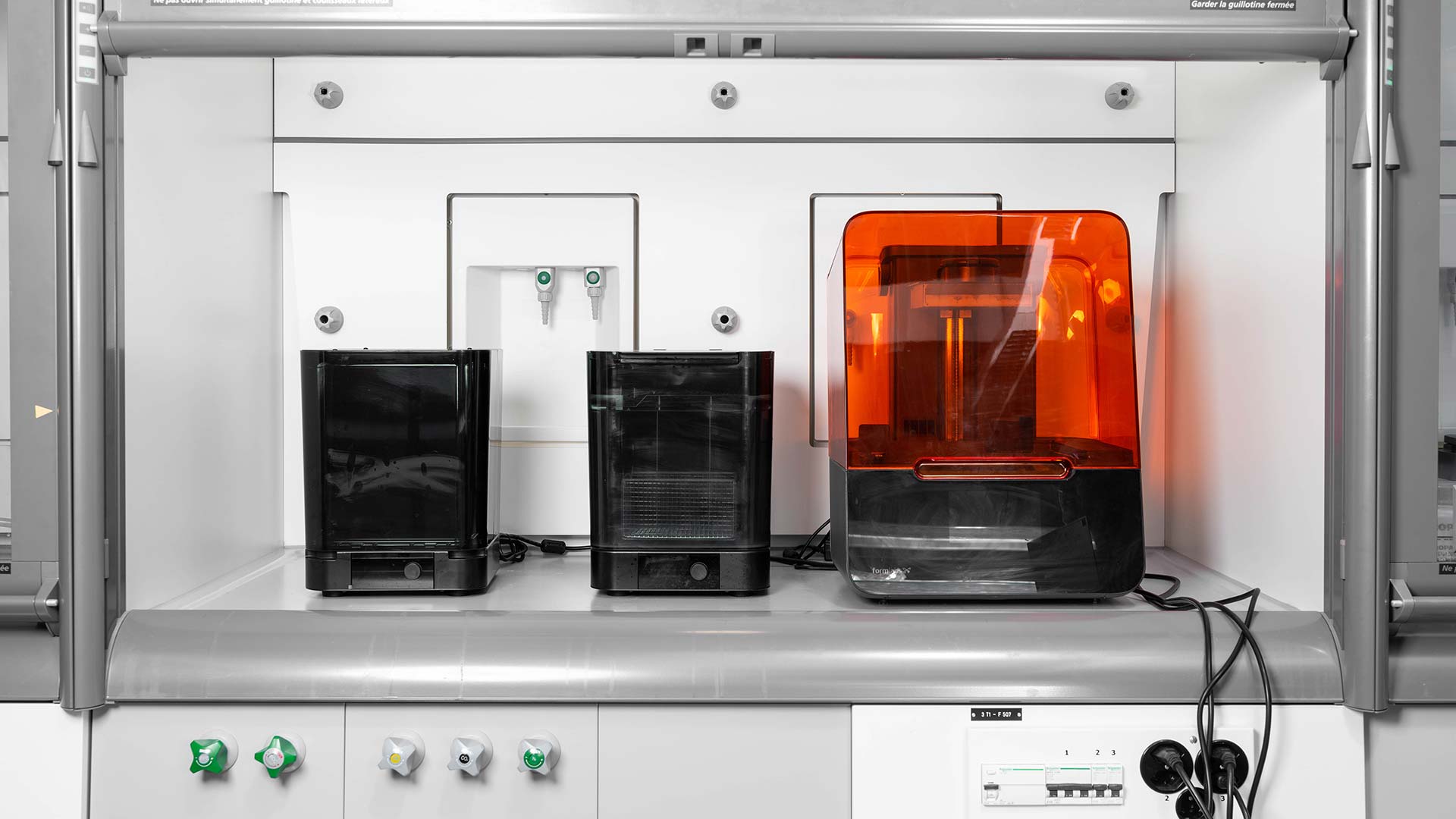
Workbench 3D printers
Guidelines for tabletop 3D printers
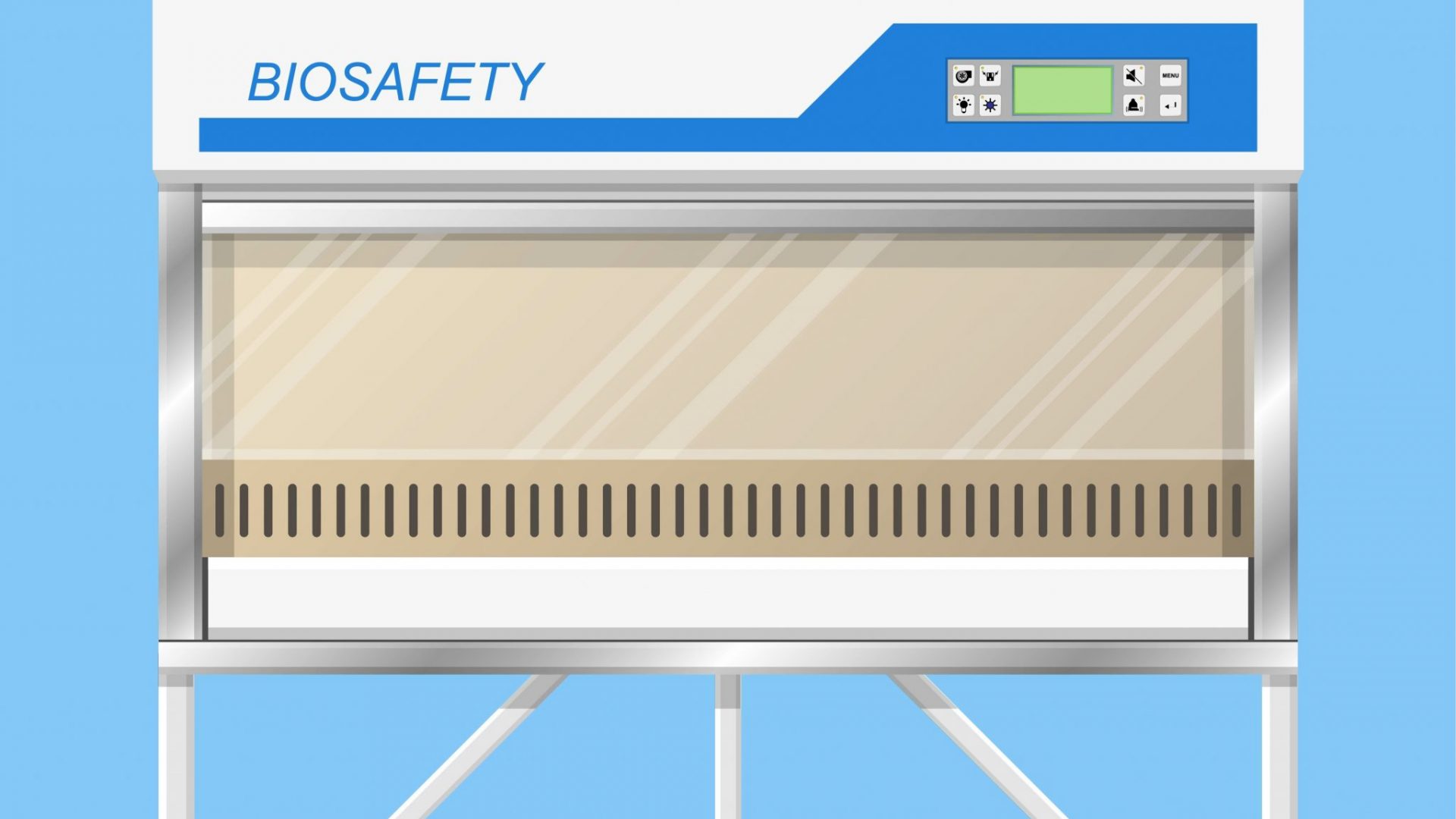
Biosafety cabinets
When working with microorganisms, care must be taken to protect:the user against infectionsthe environment from contaminationA biosafety cabinet meets both these criteria, as it is a physical barrier consisting of an airflow to protect the user from aerosols, and a glass screen to protect the user from minor spills and splashes.As they often look alike, (…)
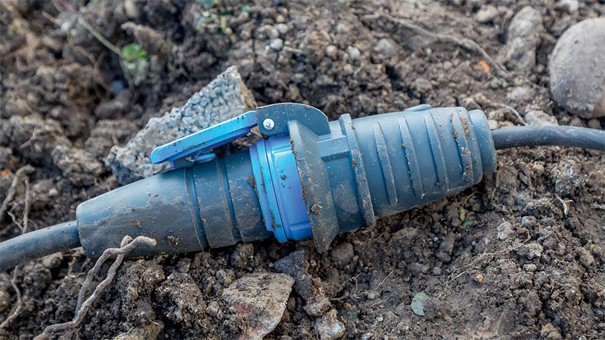
Outdoor extension cords
Extension cords and reels that comply with the new IP55 standard now offer effective protection against dust and splashing water, regardless of the angle at which they are projected and whether they are plugged in or not.
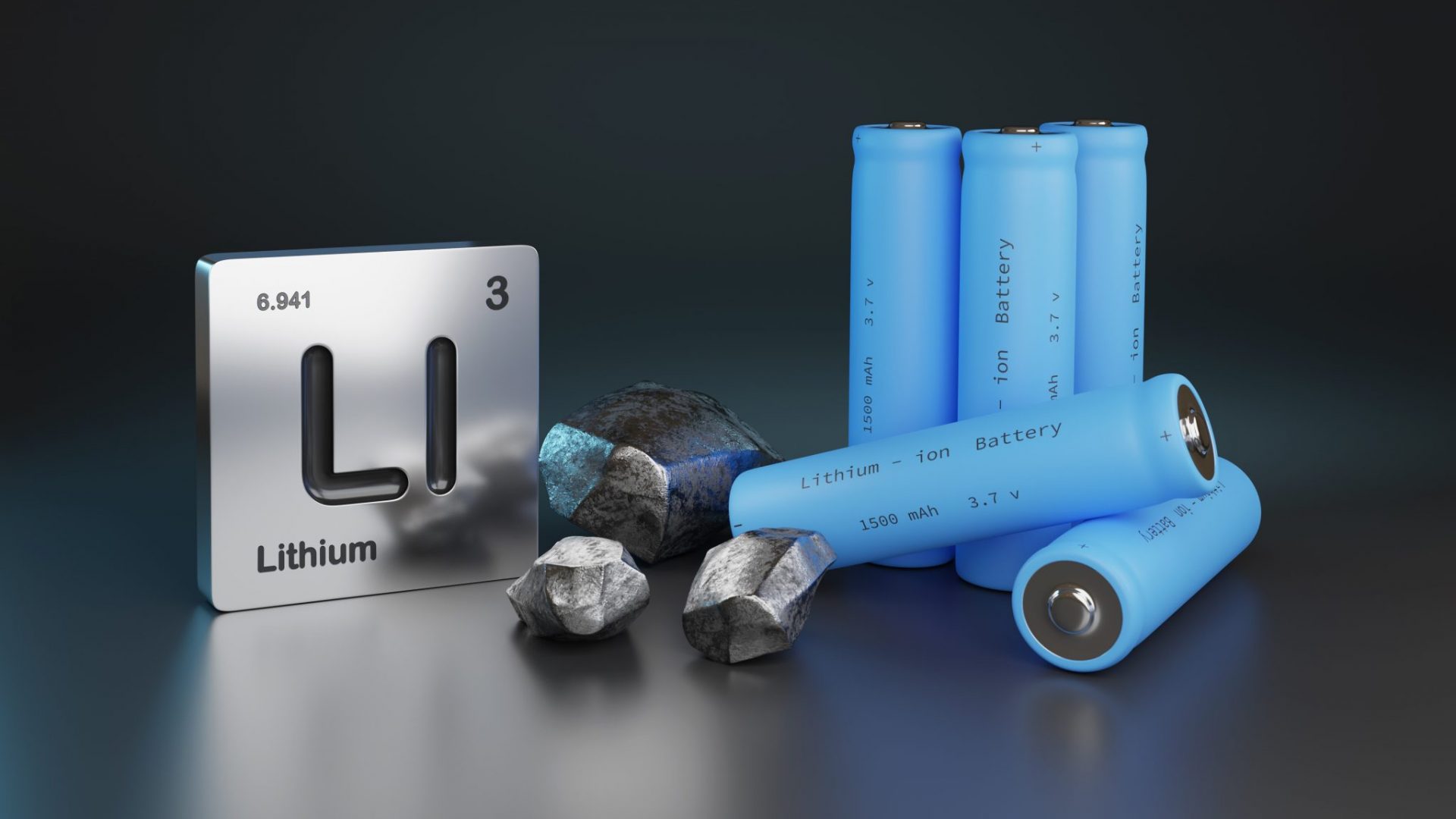
Lithium batteries
Lithium batteries pose risks due to their thermal instability. Overcharging, short-circuiting, or physical damage can induce thermal runaway, resulting in fire and/or explosion of the battery. These incidents can cause serious injuries and fires, highlighting the importance of handling, storing, and recycling these batteries with caution.General Rules- Follow the supplier’s instructions. – Avoid: heat sources, (…)