Molecular DLL – Chemical engineering
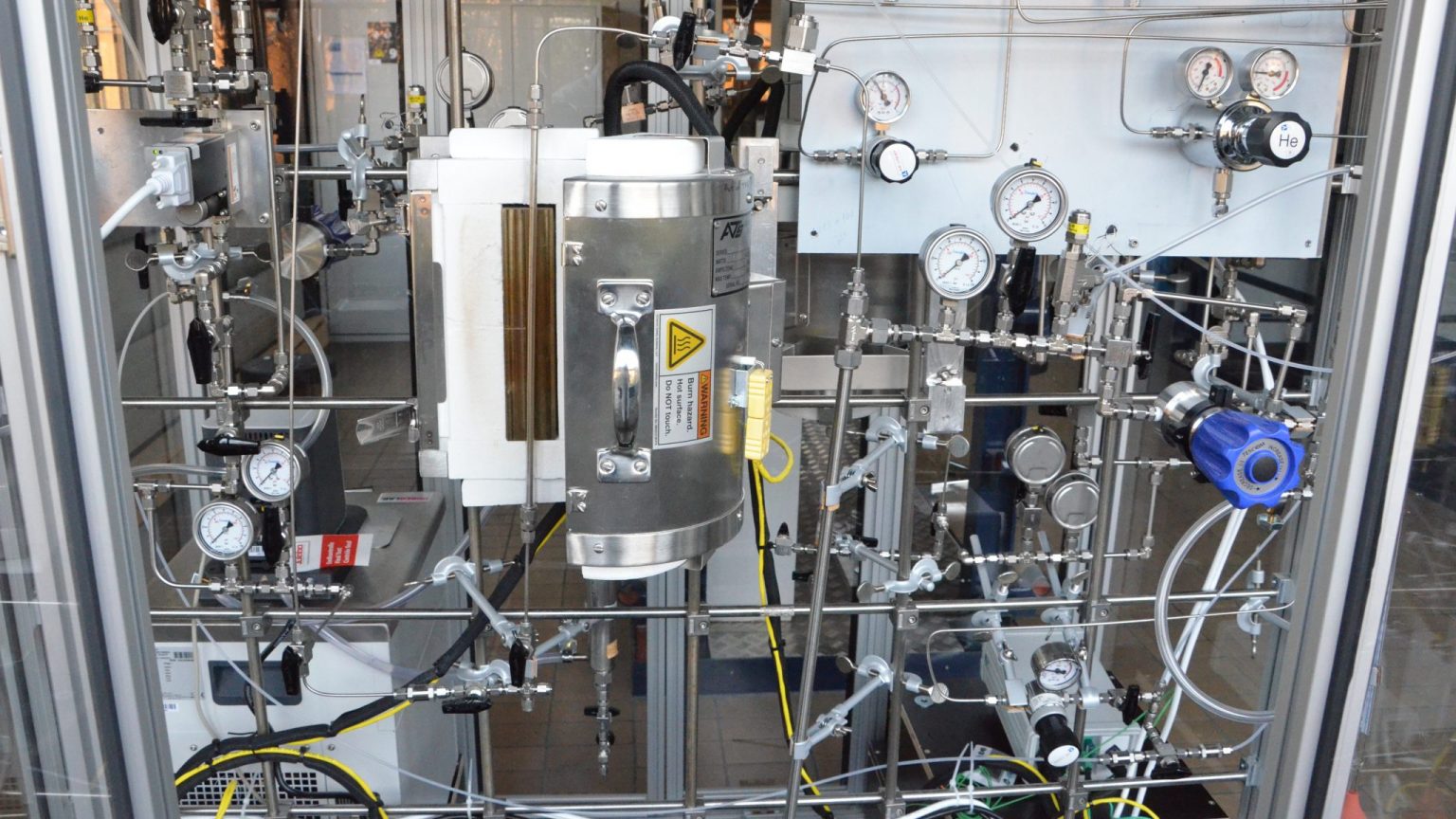
Réacteur catalytique à flux
By definition, chemical engineering, or physico-chemical process engineering, refers to the application of physical chemistry on an industrial scale.
In this chemical engineering laboratory, the main facilities that can be found in the small-scale industry are therefore available. These make it possible to test and understand the functioning of the various fundamental processes of chemical engineering.
These facilities are located in a three-storey hall and can be classified into the following categories:
- Energy conversion (fuel cell, photovoltaic, heat pump)
- Separation (crystallization, filtration, continuous distillation, liquid-liquid extraction, double evaporation)
- Heat transfer (heat exchanger, conduction, free and forced convection)
- Chemical reactors (catalytic flow reactor, residence time distribution, microreactors)
- Mass transfer (gas oxygenation)
- Fluid mechanics (hydraulic pressure drop)Process control (control of the level of a tank)
There are also devices such as:
- Gas chromatograph
- UV-Vis spectrophotometers
- 3D printer
- Analytical sieves
- Potentiostat GAMRY
As well as various apparatus and tools for mechanical and electronic manufacturing (prototyping centre)
Facilities
The different types of energy conversion are:
- Fuel cell
- Photovoltaic
- Heat pump
Horizon Educational H-100 PEM Fuel Cell – 100W
Localisation : CH C1 396
By electrochemistry, a fuel cell converts the chemical energy of hydrogen into electrical energy, producing water as the only waste.
Specifications:
Fuel cell type: PEM (Proton Exchange Membrane)
Number of cells: 20
Rated power: 100 W
Performance: 12 V to 8.3 A
Actors: Hydrogen and air
Operating temperature: 5 to 30 oC
Pressure hydrogen: 0.45 to 0.55 bar
Hydrogen purity: 99.9995 % H2 dry
Humidification: Self-moidified
Cooling: Air (integrated cooling fan)
Dimension: 11.8 cm x 10.4 cm x 9.4 cm
Maximum power output: 1.3 L/min
Starting time: 30 seconds at room temperature
Cell efficiency: 40 per cent at 12 V
External power supply: 13 V (1 V), 5 A
Localisation : CH C1 396
Understanding how the energy of our largest renewable energy source, the Sun, can be converted and used is essential for a modern chemical engineering program.
This test bench offers possibilities for measurements on two solar panels of 0.45 m2 each. It will also be possible to produce a service voltage of 20 volts in parallel and 40 volts in series.
Thermodynamics of a heat pump
Localisation : CH C1 396
This experiment makes it possible to understand the operation of a heat pump. The heat pump is a thermodynamic system that allows thermal energy to be transferred from a cold medium to a hot medium. The heat pump is a high-performance system that makes it possible to produce heat with low energy consumption. It is therefore an interesting solution for heating buildings.
The operation of a heat pump is based on the principle of compression and decompression of a refrigerant. The refrigerant circulates in a closed circuit and passes through four stages:
Evaporator: The liquid refrigerant (SOLKATHERM SES36) arrives in the low-pressure and temperature evaporator. It absorbs heat from the environment and evaporates.
Compressor: The refrigerant gas is then compressed by the compressor. The compression increases the pressure and the temperature of the gas.
Condenser: Hot refrigerant gas arrives in the condenser. It yields heat to the environment and condenses.
Pressure regulator: The high-pressure refrigerant fluid is then expanded by the pressure regulator. The expansion decreases the pressure and the temperature of the liquid.
Analysis of the results: The coefficient of performance (COP) of the heat pump is defined by the ratio between the useful heat produced (heating of the water in the condenser) and the energy consumed (work supplied by the compressor).
Evaporation – continuous crystallization MP1004
Localisation : CH C0 396
This facility illustrates the efficiency and precision of the continuous crystallisation process, often used in the chemical and pharmaceutical industries for the production of high-quality crystals.
Description of the installation
Evaporator: The evaporator is designed to concentrate the initial solution. It is continuously fed with an aqueous solution containing the solute to be crystallized. The solution concentrated in the evaporator flows by overflow to the next step of the process.
Water-cooled crystallizer: The crystallizer is designed to induce the crystallization of the solute from the concentrated solution. The concentrated solution enters the crystallizer, which is maintained at a lower temperature by means of a water-cooling system. The drop in temperature decreases the solubility of the solute, promoting the formation of crystals.
Press filter PIGNAT
Localisation : CH C0 396
The filter press is an effective method for separating the solids from a liquid. It is used in the chemical, agri-food and mining industry.
The advantages of the filter press:
High treatment capacity. The filter presses can process large volumes of suspension.
Simple operation: Filters presses are relatively easy to use and maintain.
Relatively low cost: Filter presses are generally cheaper than other types of filters, such as centrifuges.
The drawbacks of the filter press:
Discontinuous operation: The filter presses operate by cycles, which means that they are not suitable for applications where continuous filtration is required.
Sensitivity to clogging: Filters presses can become clogable easily, which can reduce their effectiveness.
Specifications :
Flow rate of the filtrate: 0 to 400 L/h (Nod nominal flow rate 100 L/h)
Filtration pressure: 0 to 3 bar relative (rated pressure 0 to 1 bar)
Power supply tank: 120L
Rate vessel: 100L
Continuous distillation MP1010
Localisation : CH C0 396
Continuous distillation is a technique for separating liquid mixtures which is distinguished by its uninterrupted operation. Unlike discontinuous distillation where the mixture is loaded in a single operation, continuous distillation involves a constant stream of the mixture to be separated in a specific apparatus. The principle is based on a distillation column, where the vapors rise and the liquids descend, creating a temperature and concentration gradient. The most volatile components evaporate first and are condensed at the top of the column to obtain the pure product.
Double effect continuous ascending film evaporation MP1052
Localisation : CH C0 396
The operating principle of the multi-effect evaporator is based on the fact that the boiling point of the water decreases when the pressure decreases.
Thus, in each effect, the pressure is maintained lower than in the preceding effect, which allows the water to boil at a lower temperature.
The use of several effects makes it possible to considerably improve the energy efficiency of evaporation.
Indeed, the heat of the steam produced in an effect is used to heat the water in the following effect, which avoids having to use an external heat source for each effect.
The multi-effect evaporator is used in many industrial applications, including:
Concentration of fruit and vegetable juices
Salt production
Seawater desalination
Treatment of industrial effluents
The MP 1052 system allows a continuous supply of up to 6 liters per hour.
There are several types of heat exchanger. :
- Liquid/liquid – tubular – double tubes – plates
- Thermal convection exchanger
- Heat conduction exchanger
Localisation : CH C1 396
Heat exchangers (tubular, double tubes, plates) are an essential component of industrial chemical plants and commercial appliances.
This module consists of a basic unit that will supply heated water at controlled flow rates for each of the three heat exchangers, all equipped with temperature sensors.
Continuous chemical reactors form the basis for chemical engineering and there are many examples in biochemical engineering, pharmaceutical industries and fine chemical industries.
Insulated stirred reservoir reactor
Insulated stirred series reservoir reactor
Insulated tubular reactor
Localisation : CH C1 396
A CSTR (Continuous stirred-tank reactor) is a reactor into which the reactants are introduced continuously and the products are also continuously removed.
The reactor is maintained at a constant temperature by means of a Julabo CORIO CD-600F heating or cooling system.
In this experiment, the hydrolysis of ethyl acetate is studied in a CSTR..
NaOH + CH3COOC2H5 → CH3COONa + C2H5OH
The residence time, the flow rate of the reactants and the temperature are the important parameters which are studied in order to determine the effect on the conversion and the selectivity of the reaction.
This experiment makes it possible to measure the residence time of a chemical component on 3 different systems:
– Tubular reactors
– Reactor capacity 3L
– Reactors arranged in series
micro mixing
Localisation : CH C2 396
Since the early 1990s, micro-reactors have been the subject of hundreds of scientific publications and patents in terms of mixing.
The main characteristics of interest of micro-mixers are their large transfer capacities, due to large transfer coefficients and large surface/volume ratios. By adapting the geometrical dimensions of the reactor to the requirements of the reaction transfer, the micromixers make it possible to carry out in complete safety particularly demanding reactions (speed speed, great exothermicity, dangerous chemicals), open new synthesis routes, improve the durability of the processes.
The experimental characterisation of micromixers is an important research area that makes it possible to obtain quantitative data on the intrinsic performance of micromixers.
We’re going to use the Villermaux-Dushman reaction to get information on the quality of the mixture in the micromixers.
Harvard Apparatus pump33DDS
Two independently controlled pumping channels in a single instrument. Perform two distinct flows using different directions, flow rates, volumes and sizes of syringe
Suitable for syringe sizes of 0.5 l to 60 ml.
Regular throughput up to 1.02 pl/min High accuracy 0.25%
Localisation : CH C0 396
This equipment consists of different types of pipes, fittings and valves which are supplied with a water flow control system (between 3 and 50) L/min.
The equipment is designed to study the behavior of closed flows over a certain range of Reynolds numbers.
- Press loss in smooth and rough pipes of different diameters :
It makes it possible to study the pressure drops in the pipes 4 m in length (except for tube No. 3, which is 2 m) but of different internal diameters:
PVC TUBES :
(1) smooth, Øint. = 22 mm
(2) smooth, Øint. = 28.2 mm
(3) smooth, Øint. = 44,5 mm
(4) rough, Øint. = 22 mm
(5) rough, Øint. = 28.2 mm
- Pressure loss in the various elements :
(1) Filter
(2) Membrane valve
(3) Pitot Øint. 32 mm
(4) Venturi
(5) Diaphragm
(6) Double elbow 90° Øint.. = 25 mm
(7) Simple elbow 90 ° Øint.. = 25 mm
(8) Simple elbow 120° Øint.. = 25 mm
Fixed and fluidized bed
Localisation : CH C0 396
The objective of this installation is to create a fluidized bed using glass beads of different diameters in a tube. A fluidized bed is a system where solid particles are suspended in a fluid (usually a gas or a liquid) in such a way that they collectively behave like a fluid. This experiment demonstrates the principle of fluidisation and shows how a bed of solid particles can be handled to behave like a fluid, thus paving the way for many effective and innovative industrial applications.
Preparation of the fluidized bed:
The glass beads are placed in the plexiglass tube with an inner diameter of 44 mm and a height of 44 cm.
Introduction of the fluid:
A fluid (usually air or water) is introduced through the base of the tube at a controlled flow rate (between 0 and 5 liters/minute).
Fluidized bed formation:
When the fluid velocity reaches a certain critical point (called minimum fluidization speed), the particles begin to rise and separate from each other, thus forming a fluidized bed. The particles in suspension in the fluid behave like a liquid, allowing homogeneous mixing and uniform distribution of the particles in the fluid.
- Applications and uses
Fluidized beds are used in various fields in chemical engineering due to their ability to improve heat and mass transfer, as well as for their homogeneous mixing and distribution characteristics. Here are some common applications :
Fluidized bed reactors : used for various chemical reactions, in particular for catalytic cracking of hydrocarbons.
Fluidized bed combustion : used to burn solid fuels with increased efficiency and reduced emissions.
Coatings : application of coatings to particles or objects by hanging them in a fluidized bed and exposing them to a coating material.
Heat and mass transfer : used in heat exchangers and separation systems to improve process efficiency.
- Benefits of Fluidized Beds
Omogeneous mixture : ensures uniform distribution of the reactants and a constant temperature throughout the reactor.
Efficient heat transfer : the suspension of the particles allows excellent heat transfer between the particles and the fluid.
Reactions control : allows better control of chemical reactions and reduces hot spots in the reactor.
Gas absorption on a wetted wall :
Localisation : CH C1 396
This installation makes it possible to understand the mechanisms of absorption of gas by a moistened wall and to determine the mass transfer coefficients as a function of the experimental conditions. The results can be used to optimise industrial processes involving the absorption of gases in liquids.
A conventional example is the absorption of carbon dioxide (CO2) with an aqueous solution of sodium hydroxide (NaOH). The CO2 is fed in the tube where it is absorbed by the solution of NaOH forming sodium carbonate (Na2CO3) or sodium bicarbonate (NaHCO3).
Principle of the Oxygen Experiment of Water
Preparation of deserted water : Gaseous nitrogen (N2) is bubbled through the water to remove dissolved oxygen. This deaeration process continues until the oxygen concentration is negligible or reaches a desired level. (Deoxygenation column)
Glass column : The deerated water is pumped (AB-1) at the top of the column, where it is distributed uniformly to form a thin liquid film that descends along the inner walls of the column. (Oxygenation column with film falling 30 mm in diameter and 600 mm in length)
Introduction of Oxygen : An air flow is introduced into the column, usually from the bottom, so that it rises counter-currently with respect to the descending liquid film.
Measurement of Dissolved Oxygen : Two oxygen probes are placed at the inlet (02 IN [%)) and at the outlet (02 IN [%)) of the column to measure the concentration of dissolved oxygen. This concentration measurement is carried out by means of two electrochemical probes INPRO6050/120 from Mettler-Toledo.
Mass Transfer measurement : These measurements make it possible to determine the amount of oxygen absorbed by the water at different water and air flows.
Bench test MINIREG-LF :
Localisation CH C1 396
Control of level control or flow control processes is an essential concept in chemical engineering. The MINIREG-LF test bench is designed for study and experimentation on a level control loop in a column and flow rate loops in a pipe.
The practical work carried out on this bench is intended to :
- Understanding the operation of a control loop and its various components : method, sensor, regulator, actuator.
- Inducing students to different types of regulation.
- Use supervision software that allows real-time parameters to be changed and operating curves to be visualized.
Gas chromatography (GCP) is a technique that makes it possible to separate molecules from a mixture that may be very complex and of very different natures. It applies mainly to compounds that are gaseous or capable of being sprayed by heating without decomposition.
GC AGILENT 8860 system
Localisation : CH C2 396
This chromatograph is provided with two injectors :
- In front of an automatic injection turret placed on a split/splitless injector
Behind, a pneumatic injection system with an injection loop (0.25 mL) for the continuous analysis of gas mixtures.
Detectors : two FID (flame ionization detector) are placed at the outlet of each of the columns.
Columns :
Type of column |
Length [m] | Diameter [mm] | Film [µm] | T. limits [°C] |
HP-5 | 30 | 0.320 | 0.25 | 325 |
GS-ALUMINA | 30 | 0.530 | N/A | 200 |
HP-AL/S | 25 | 0.320 | 8.00 | 200 |
Each UV-Vis spectrophotometer is coupled to a computer with software for spectra acquisition and processing.
Spectophotomètre UV-VIS VWR model UV-3100PC
Localisation : CH C0 396
Specifications:
Optical system: single beam
Source lamps: Tungsten/deuterium
Wavelength range: (190 – 1100) nm
Wavelength accuracy: 0.5 nm
Spectrophotometre UV-VIS lambda 365 de Perkin Elmer
Localisation : CH C2 396
Specifications:
Optical system: double beam
Source lamps: Tungsten/deuterium
Wavelength range: 190-1100 nm
Wavelength accuracy: 0.3 nm for full range
Markforged modèle Mark Two
Localisation : CH A0 397
Equipment to make parts on your desk as strong as aluminium.
Construction volume (320 x 132 x 154) mm (12.6 x 5.2 x 6) in
Layer height Default 100 microns, maximum 200 microns
Plastics available: Onyx
Available fibres: Carbon fibre
Projet MJP 2500 Plus
MJM – Multi jets déposition
Localisation : CH A0 397
Multi Jet Modelling. This process is similar to a print head of a conventional 2D inkjet printer, but has hundreds of jet nozzles and whose droplets of resin or wax are a few microns.
Construction volume (294 x 211 x 144) mm (11.6 x 8.3 x 5.7) in
Plastic available: VisiJet M2R-CL transparent
Analytical sieve HAVER & BOECKER EML 200 Pure
Localisation : CH C0 396
This system can be used, for example, to determine the distribution of crystal sizes.
External diameter : 209 mm
Material: stainless steel
We have at our disposal 10 sieves with different screen opening widths
(aperture width) :
10 mm / 5 mm / 2,5 mm / 1,25 mm
1.630 µm / 315 µm / 150 µm / 75 µm / 38 µm / 20 µm
Potentiostat GAMRY :
Localisation CH C0 397
The Reference 3000TM is a potentiostat/high-performance resitance Amperometrie recommended for the development of batteries, condensers or fuel cells, as well as for general electrochemical measurements requiring higher currents.
The Booster Reference 30kTM is ideal for higher-current applications such as large-format batteries and lead-acid batteries. It is also ideal for fuel cell testing. The insulation of the earth allows operation in parallel with an electrical power supply, an electronic load or grounded cells.
The 30K reference booster is attached to a reference potentiostat 3000 or a reference auxiliary electrometer 3000 to bring the current limit up to 30 A with conformity limits of 20 and -2.5 V. This high-current device has an impressive bandwidth allowing EIS measurements up to 300 kHz.
Access and safety rules
These facilities are located in a three-storey hall in the CH building:
CH C0 396
CH C1 396
CH C2 396
Safety rules : Any person wishing to handle chemicals must be trained accordingly, in accordance with the safety rules at EPFL, the DSPS, and the rules specific to ISIC/SCGC.
Training and booking
Julien Andres, +41 21 693 74 55
Activities and courses
Cours | Titles |
ChE-203 | Heat exchanger 1 Drop pressure Refrigeration and heat pump Photovoltaics Continuous chemical reactors 1 Fuel cell |
ChE-309 | Continuous chemical reactors 2 Double-acting evaporator Fixed and fluidized bed Water oxygenation Regulation of the level of a tank Filtration (press filter) Heat exchanger 2 |
ChE-409 | Continuous distillation Liquid/liquid extraction Residence time in a reactor Micro mixers |