This project builds on the successful integration of prior educational technologies in classrooms of carpenter apprentices. The video below shows a sample activity of a tablet-based technology that can be deployed in classroom for understanding the behavior of a roof structure in the presence of loads like wind or snow.
Embed of video is only possible from Mediaspace, Vimeo or Youtube
Swiss carpenter apprenticeship lasts 4 years and involves one day per week at school and 4 days per week at the workplace. Master carpenters are required to be able to design and structurally guarantee the soundness of roofs in residential buildings and understand the building physics intuitively. Transfering this intuition to apprentices is necessary for their safety in the construction process and also for the stability of their products for those who finish the apprenticeship and make their own enterprise. Although carpenters are not structural engineers, they should be able, as stated on their newly reformed curriculum, to understand, explain, describe, illustrate and show the building physics of a structure. However, transfering this intuition from master carpenters to apprentices is difficult. On one hand, they cannot test the building physics in the workplace. On the other hand, schools have neither enough time to spend on teaching statics nor any way to relate intuitively the complex structures found in the workplace with basic notions like compression, tension and stress of material.
The tangible part
The system is a Tangible User Interface (TUI) with a tangible and a virtual interface that communicate through a paper interface. The tangible interface provides to the apprentice the familiar to him setting of joining rods and a simple way to build and navigate in 3D conceptions.
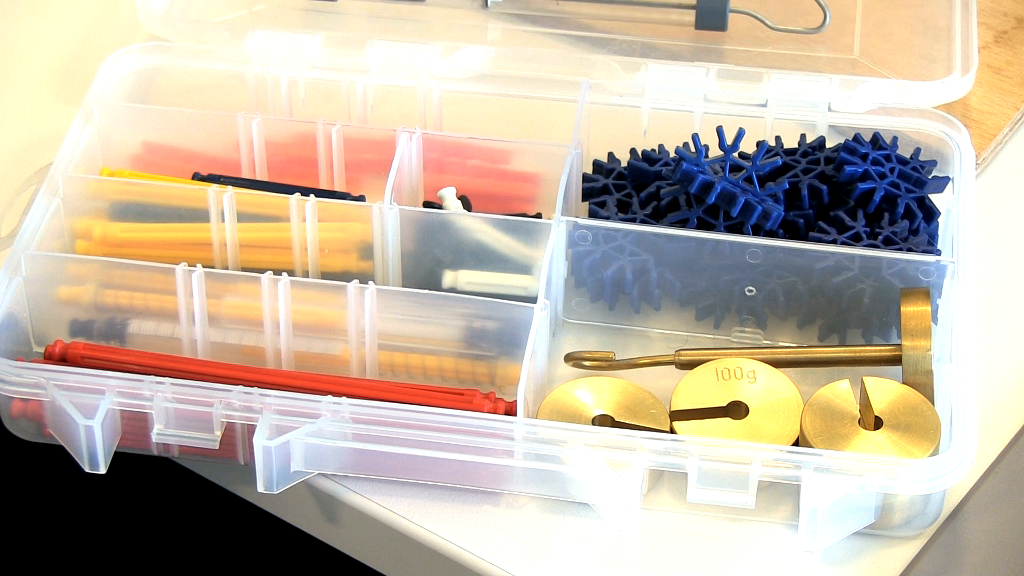
Each structure is made with plastics rods connected together with plastics connectors. The different kinds of connectors enable the construction of 3D structures with angles of multiple of 45° in all three directions. To apply a force, weights or dynamometer (see fig. 2) can be used. The whole structure is screwed to a wooden plate to have a stable base. To visualize the applied forces as a form of immediate feedback, a compression spring is used along with a millimiter ruler as shown below.

The student worksheet
The paper interface is both a material that the system can detect and also a material that is heavily used in room. The activity shown on the video on the top involves an exploration phase of building and stress testing, a theoretical exercise to reflect on that experience and link it with abstract concepts and a second challenge that seeks on using these concepts.
The virtual part
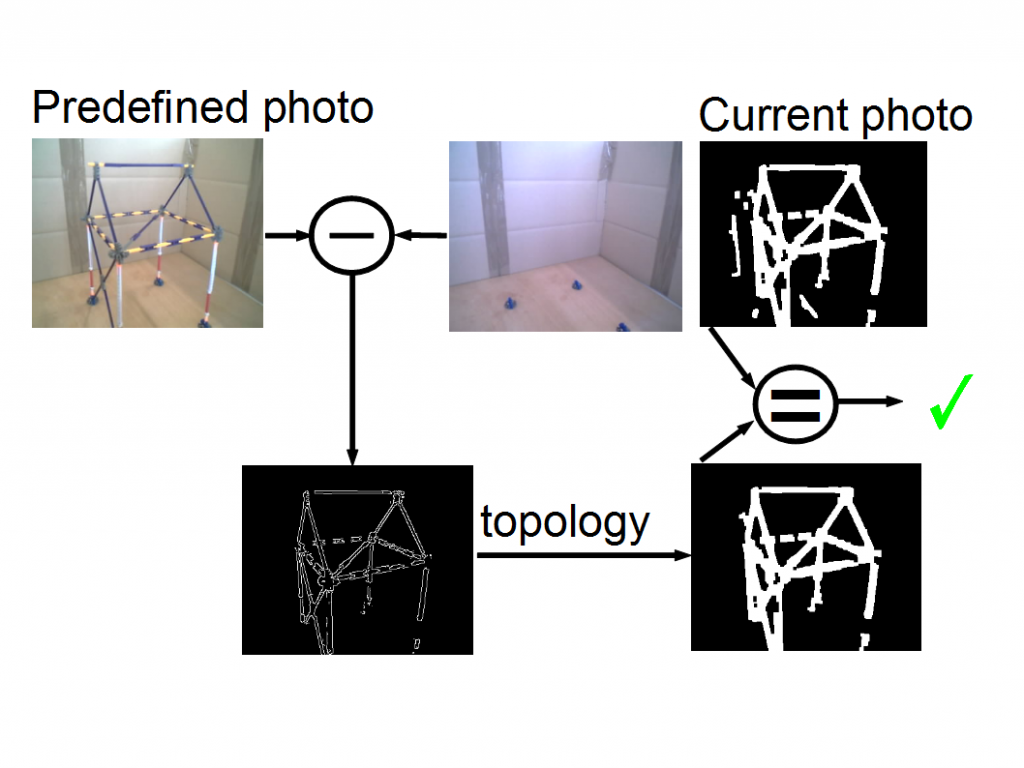
The virtual interface allows the teacher to build activities around specific structures and concepts. The system is based on the principle that structures with the same way of connecting the rods correspond to similar images when viewed from the same point of view. The reference scene can be made by the teacher and the purpose of the two white squares on it is to help the student move the camera to the right point of view. When the student wants to validate his answer, he puts an Augmented Reality marker in front of the camera. This way, he doesn’t have to stop his mental task in order to communicate with the system.
An AR marker is a very distintive element and once the system detects its presence and then its absence for 3 seconds, it takes a photo of the structure. The system processes each image by removing the background and comparing the topology of the current image with the reference image. Finally, the educational activity can be deployed on a large scale as it requires only a camera and no specialized hardware.