The LAI is specialized in modeling (using developed analytical models and FEM) and design optimization of rotating and linear electric motors and actuators.
- The design optimization is performed using deterministic methods (based on various gradient methods – the commercial software ProDesign) or stochastic ones (a genetic algorithm developed by the LAI members, or design for experiment). The power ranges from several kW (electric traction) down to µW (MEMS – batch-processed motor placed on a silicon chip).
- To miniaturize an electric drive and increase its reliability by eliminating position sensors, sensorless control algorithms are applied. A broad set of electromagnetic phenomena is exploited to estimate the rotor/mover position. Among them, two completely new ones are used: the first one is the Magnetic Anisotropy of permanent magnet materials (MAM method) and the second is the local B-H hysteresis loops method.
Electromagnetism being the core of the Lab activity, two application domains have emerged: Contactless Power Transmission (CPT) and Radio Frequency (RF) based solutions for access control.
- CPT domain has brought the Lab to develop solutions for many applications. Among them, medical devices for direct stimulation, blood analysis, or power supply; transportation devices for battery charger, high speed vehicles, or particular robots; industry machines for special supply, specific movements, or combined information and power.
- The use of the RF domain leads to a lot of advantages in terms of movement freedom. Therefore, it is perfectly suited to ease individuals access management according to their position.
The combination of existing technologies and the use of new smart materials leads to new innovative devices.
- In the field of piezoelectric actuators, two main axes of research are followed. One axis addresses the generation of a touch feeling: a piezoelectric actuator generates vibrations on a touch screen so that the user feels a modified friction coefficient when touching the screen. The second axis concerns generation of high forces in a reduced volume. Sensorless techniques are applied to piezoelectric-based linear actuators as well. In the domain of haptics, the potential of Neural Networks and Machine Learning for position feed-back generation on a piezo-driven surface is explored.
- The use of Shape Memory Alloys (SMA), combined with Permanent Magnets (PM) leads to hybrid grippers that opens doors to new markets in replacement of conventional pneumatic ones.
- Dielectric Electro-Active (DEA) polymers present particular characteristics that are exploited by the Center for Artificial Muscles (cf. CAM) to benefit from actuators with large deformations under high voltage supply. Specific electronics is developed.
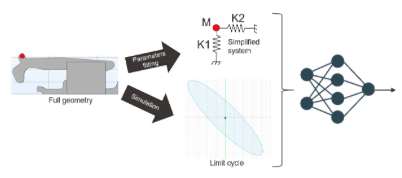
Artificial Intelligence and Topological Optimization
Topology Optimization pushes mechanical devices performances to their best. In order to make it pertinent in the field of piezoelectric actuators, driven by the not yet fully understood friction phenomenon, we need to model interaction between two surfaces at small scale and high acceleration.
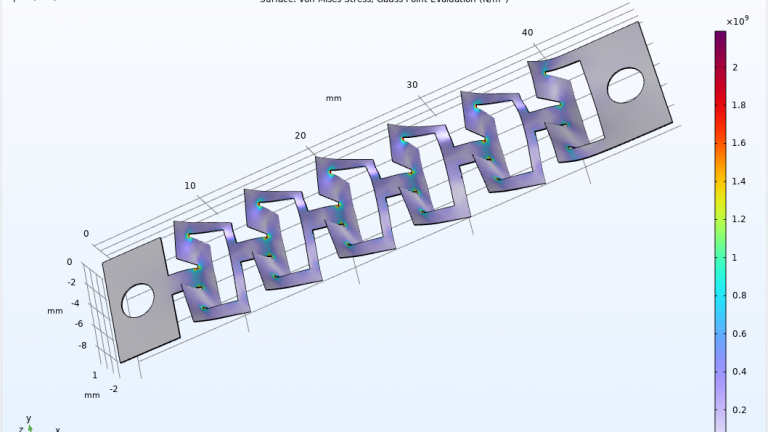
SMA-based Gripper
The step towards machines without pneumatic is a strong signal for the automation consumer industry that the Laboratory of Integrated Actuators (LAI), along with a Swiss company, Mikron SA have taken to establish a clean, energy-saving assembly solution that meets the requirements of the production environment.
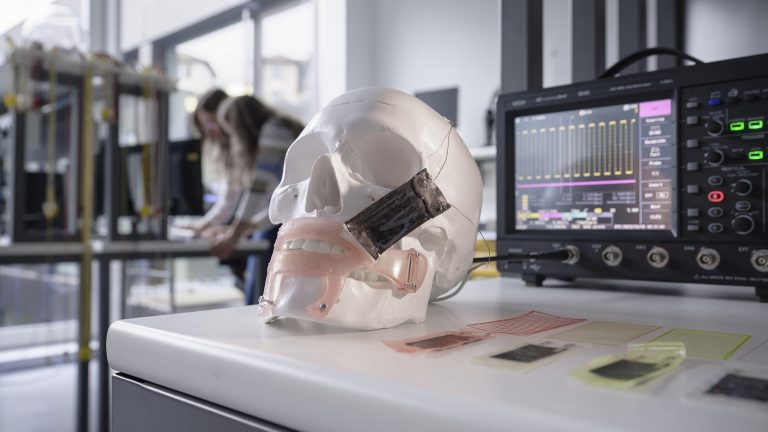
Reinforced DEAs for post-Paralysis Facial Reanimation
Facial paralysis is a highly burdening condition, resulting in a patient’s inability to move his musculature on one or both sides of his face. Our team is working on a novel, less invasive approach for dynamic facial reanimation, using artificial muscles.
© WSS – Félix Wey
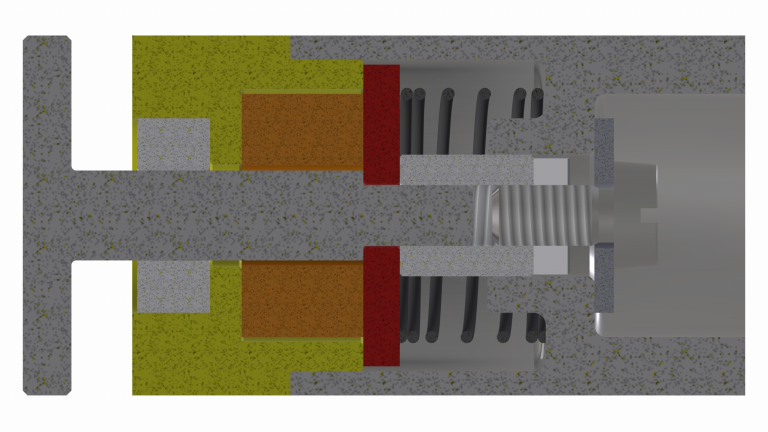
Fluid-less Damper
Complications of Diabetes Mellitus can lead to peripheral neuropathy, causing a lack of sensitivity in the foot that may result in skin damage and ulcers.
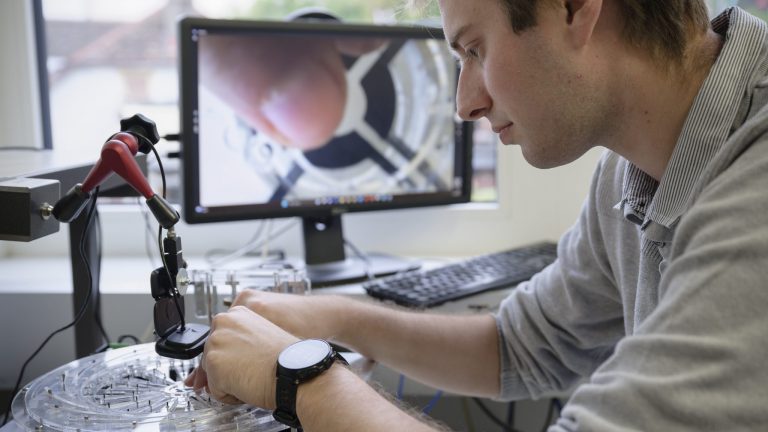
Artificial Bio-bladder
The human bladder is an expandable muscular organ which stores urine and help in its flow control. Various diseases can occur that could prevent the bladder from a proper function.
© WSS – Félix Wey
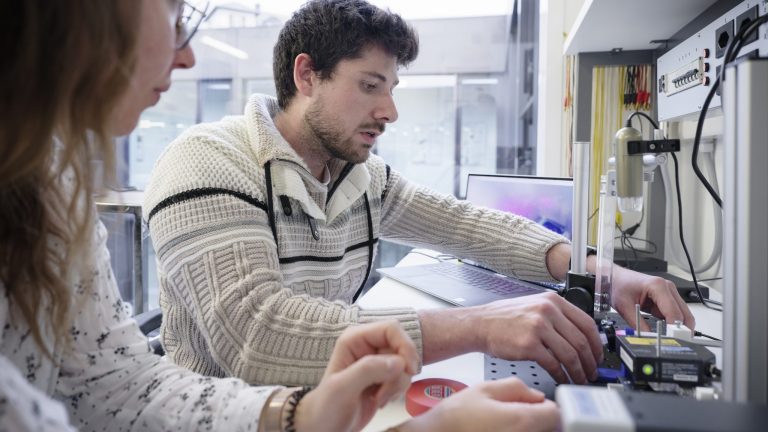
Artificial Urinary Sphincter
Lower urinary tract dysfunctions and symptoms and Urinary Incontinence (UI) in particular is a medical condition that affects millions of people worldwide. UI can be defined by an involuntary loss of urine.
© WSS – Félix Wey
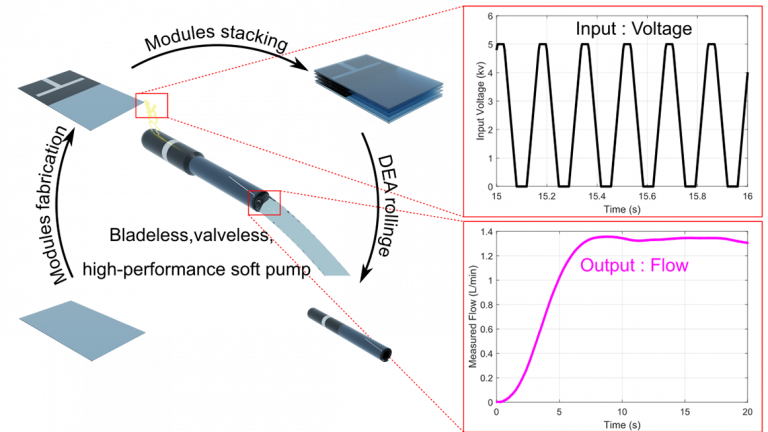
Impedance Pump for Fontan Circulation Support
Impedance pumps use flexible tubing with different impedances to generate flow through periodic compression. A bladeless, valveless soft pump, inspired by embryonic heart mechanisms, employs DEAs.
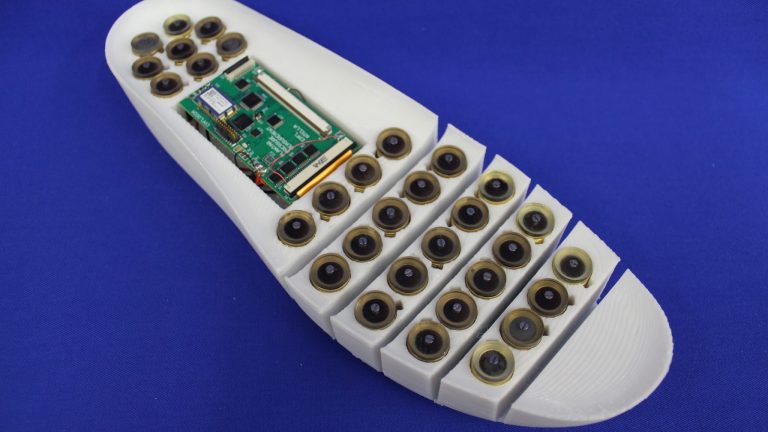
Smart Insole for Foot Ulceration Prevention
At LAI, we develop a smart insole for diabetic patients in order to prevent diabetic foot ulceration (DFU).
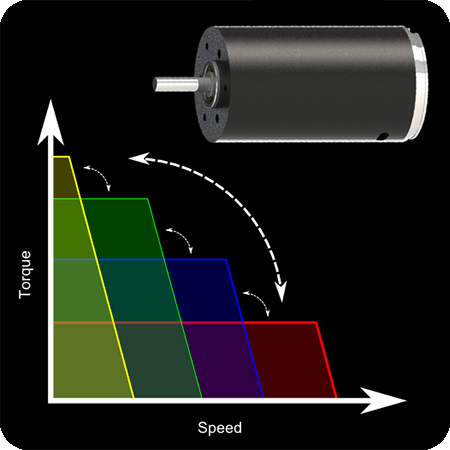
Auto-adaptive synchronous motor
CTI Project
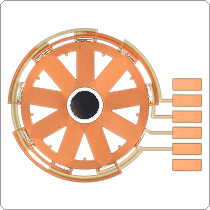
BLDC motor as a MEMS
CTI Project
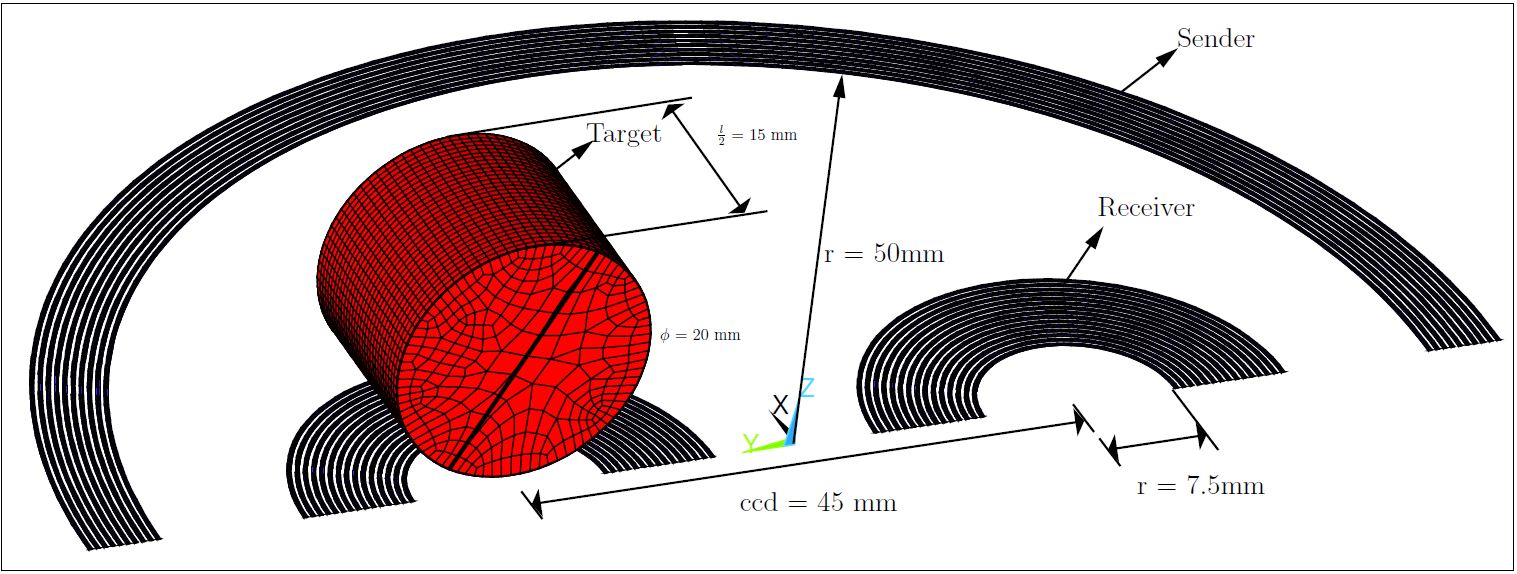
Nondestructive detection sensor technology
Foreign Industrial Partner
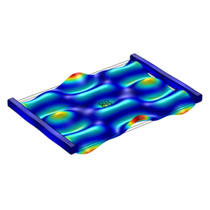
Piezoelectric vibration system
CTI Project
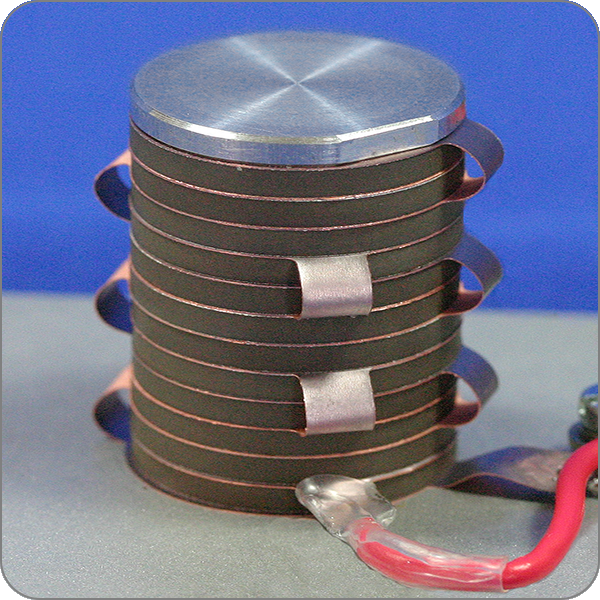
Haptic touch interface
CTI Project
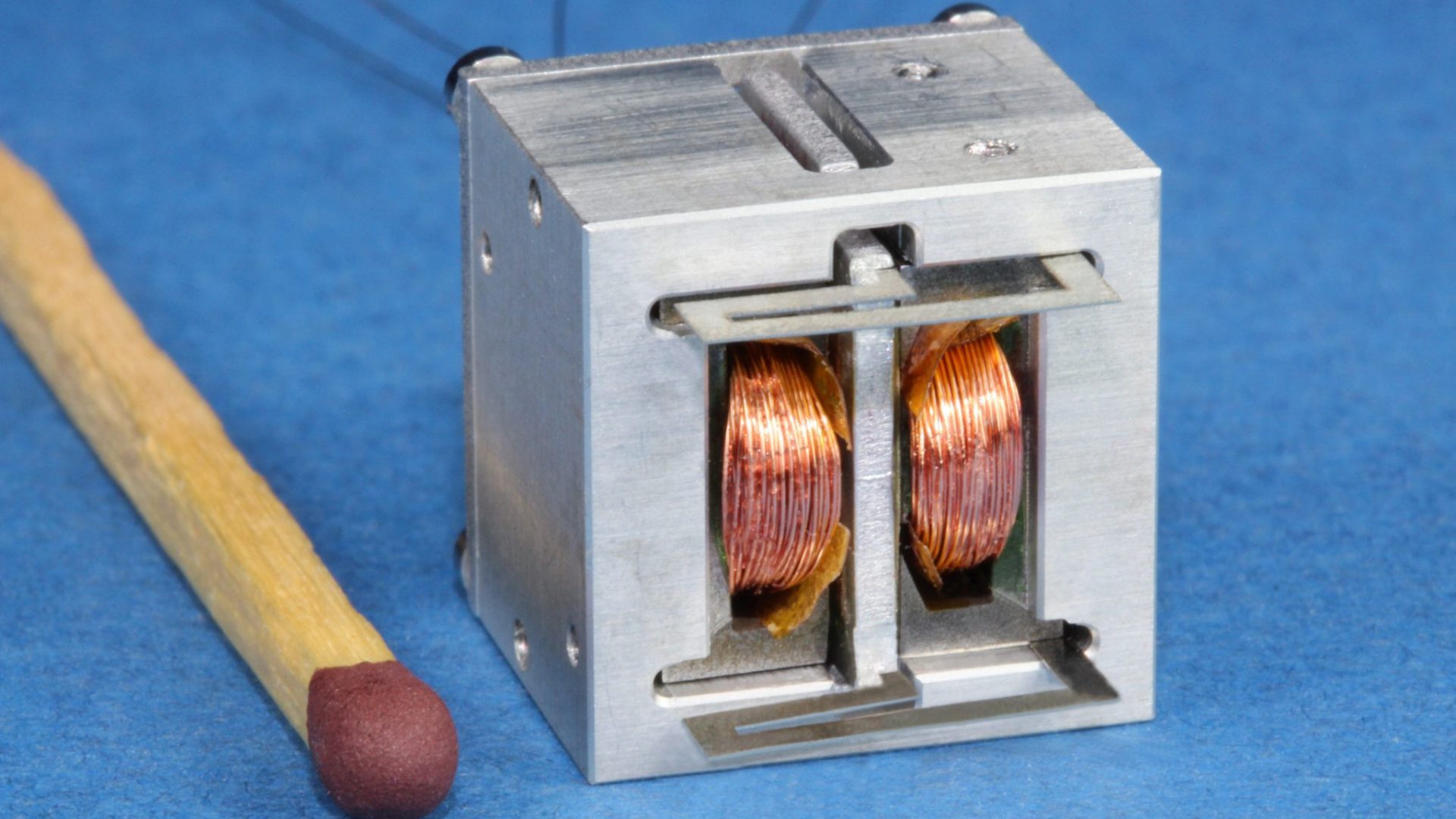
Linear escapement mechanism
CTI Project
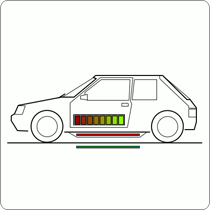
Design of a contactless power transfer for an electric vehicle battery charger
Foreign Industrial Partner
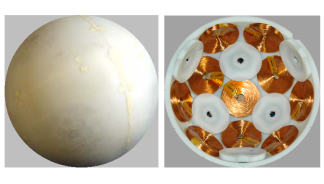
Reaction sphere for satellite attitude control
CSEM Partnership
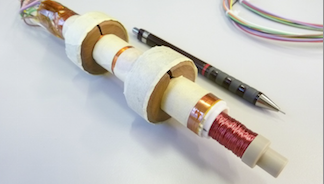
LVDT magnetic sensor
CERN Partnership
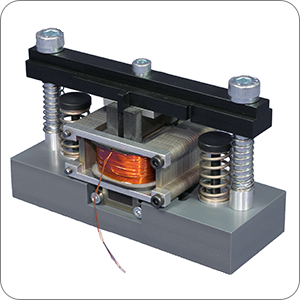
Linear electromechanical actuator with sensorless position control
Foreign Industrial Partner