Innosuisse project in collaboration with a Swiss industrial partner
Project description
The step towards machines without pneumatic is a strong signal for the automation consumer industry that the Laboratory of Integrated Actuators (LAI), along with a Swiss company, Mikron SA have taken to establish a clean, energy-saving assembly solution that meets the requirements of the production environment. Pneumatic actuators are currently the gold standard for part handling, but they have several disadvantages, including low energy efficiency, particle creation, and the necessity for complicated infrastructure.
This research addresses the replacement of pneumatic grippers with an innovative method of actuation based on shape memory alloy (SMA). The new sort of gripper takes advantage of the high work output per volume of smart materials. Shape Memory Alloys (SMAs) are one promising type of smart material with a high work output. This gripper would be lightweight and compact, allowing it to be used as a pick-and-place gripper for clean-room applications. The research aims to investigate a novel technology that will take advantage of the properties of this smart material to create a highly responsive, dynamic, lightweight, and compact actuation system while it doesn’t utilize the conventional design. By using the conventional design of the actuation part such as wire or coil, it is possible to have either a higher stroke or higher force output. Therefore, this research project aims to design and investigate novel structures to create higher force output and higher stroke without adding any complexity to the system.
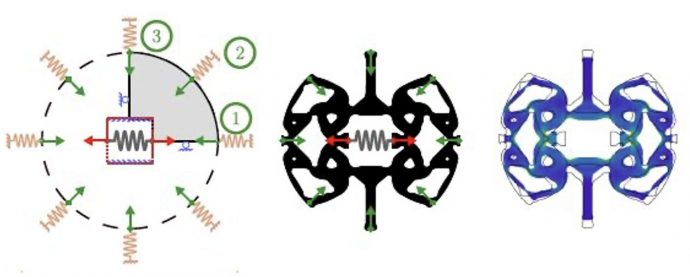
In addition to providing higher force and stroke, the fatigue life of the actuation part can be improved through this novel design. This innovative approach allows for the uniform distribution of load within the structure, as opposed to concentrating the load on microstructural defects. Consequently, we gain better and effective control over the mechanical behavior of the actuation part.
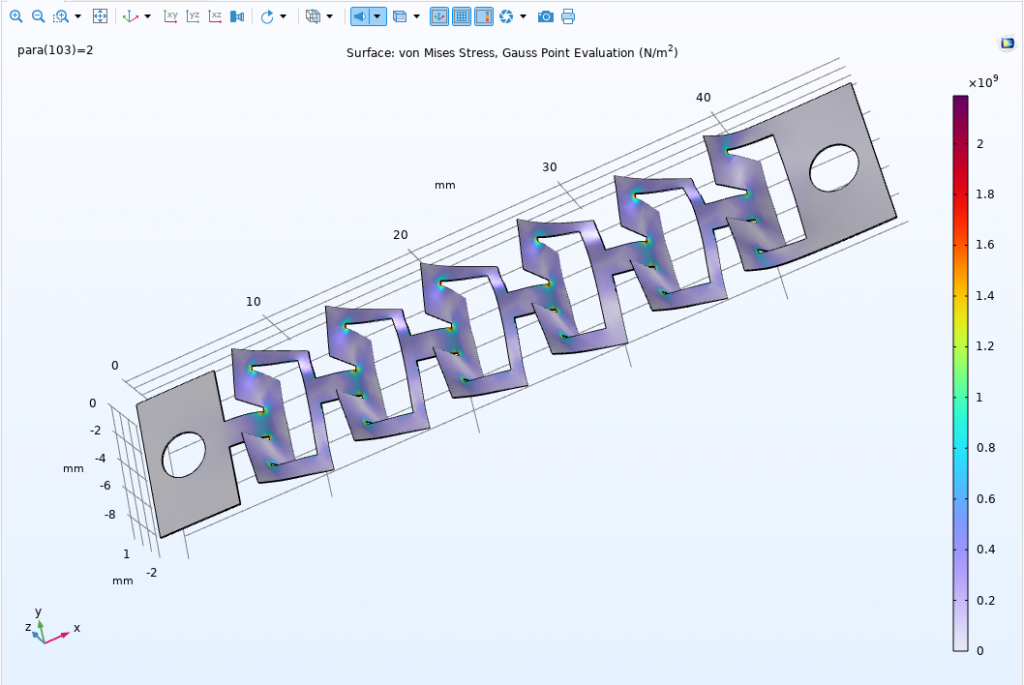
Nowadays, the limiting factor of SMA is the response time. The goal of the project is to overcome this limitation by studying new unconventional designs that will allow optimizing the thermoelastic and morphological response of the active element structure significantly boosting the actuator working frequency.
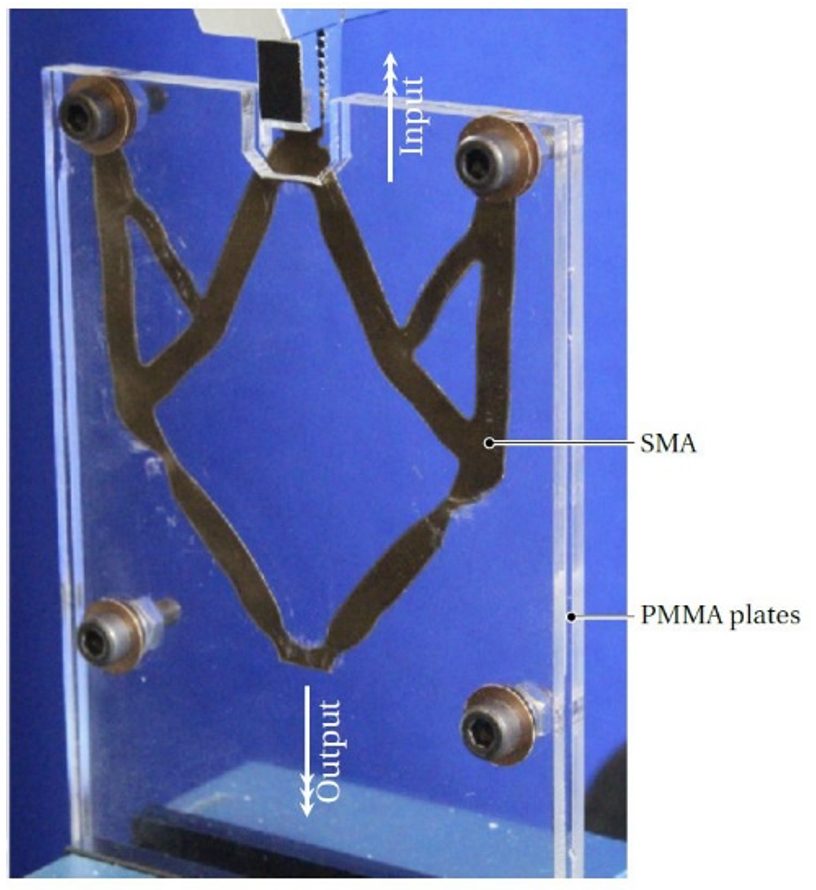
Please note that the publication lists from Infoscience integrated into the EPFL website, lab or people pages are frozen following the launch of the new version of platform. The owners of these pages are invited to recreate their publication list from Infoscience. For any assistance, please consult the Infoscience help or contact support.