Formation and drying of colloidal crystals
Much interest has been generated in the fabrication of colloidal crystals and ordered arrays from suspensions because of the promise of photonic band gap applications amongst others.
Non-sedimenting colloidal spherical silica with diameters varying from 80 to 20 nm, with controlled colloidal stability have been used to fabricate colloidal crystals by drying the suspending liquid.
During drying, the repulsive interparticle forces at distances larger than 1 nm and possible steric repulsions [1] allow the particle rearrangement up to a critical point where the capillary forcescome into play , whichare several orders of magnitude greater.
This makes avoiding cracks on the macroscale (mm) difficult without the use of binders. Careful drying experiments showed the 3 different stages of drying clearly.
Measurement of the loss of weight (solvent) as a function of time at constant temperature and relative humidity (drying mechanism) | SEM picture showing the hexagonal close packed arrangement of spherical silica particles (80 nm) after drying |
Fabrication of large-area ordered arrays
Regular arrays of nanometer-scale particles with tailored properties are expected to find applications in diverse fields, including optical & data storage devices, bio-sensors and colloidal lithography.
Guided-assembly of colloidal particles on patterned templates is a promising method for fabricating such particle arrays in a controllable fashion.
By combining novel lithographic and colloidal methods ordered arrays of particles as small as 15 nm (e.g. gold and silica) can be achieved over large areas by using dip-coating.[3]
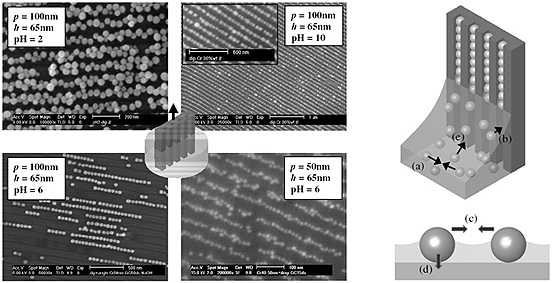
Left: Particle arrays obtained on substrates with groove patterns by dip-coating in the direction parallel to the grooves (varying suspension properties and dip coating velocities) | Right: Schematic representation of the various interactions present at the liquid meniscus of a vertically immersed substrate. |
The use of dip-coating on topographically structured surfaces opens the way to producing large area defect-free ordered structures.
No specific chemistry is required on the template or the particles to enable the assembly process. Therefore the methods are generic and allow a large choice of support and particulate materials [3]
More information:
1. Langmuir 2005, 21, 5761-5769