Additive Micro-Manufacturing for Plastic Micro-Electro-Mechanical-Systems
![]() |
![]() |
PI: Prof. Dr. Juergen Brugger
Project start: 1st October 2017
Project duration: 60 months
Summary
The manufacturing of silicon-based MEMS today is well advanced because the micro-electro-mechanical devices for automotive, domestic, health-care and consumer electronics can be fabricated with methods from IC industry. Polymer-based MEMS have a great potential for flexible electronics and biomedical applications, but to date, the techniques to engineer functional polymers into 3D microsystems, are still at their beginning because a coherent fabrication platform with the right tools and processes does not yet exist. The field could tremendously benefit from a coordinated effort in materials and manufacturing, in particular with a focus on biocompatible plastic materials. Additive manufacturing such as 3D printing and associated processing such as sintering has already started to transform traditional industry, but is not scalable much below a micrometer because the thermal processing is done in bulk or by lasers on surfaces. MEMS 4.0, in analogy with the industry 4.0 concept, aims to perform concerted research in additive manufacturing at the micro/nanoscale and associated key techniques. Using my expertise in MEMS and Nanotechnology, MEMS 4.0 will push the frontiers in new materials and new processing for MEMS by setting a focus on stencilling, printing, self-assembly and local thermal processing. This coherent processing framework will permit the use of delicate, soft, polymer materials to engineer the next generations of plastic MEMS. We are primarily targeting biodegradable implantable MEMS and permanently implantable glassy carbon MEMS. They are the most challenging to fabricate, but if successful, they also have an enormous impact for future wearables and implantables.
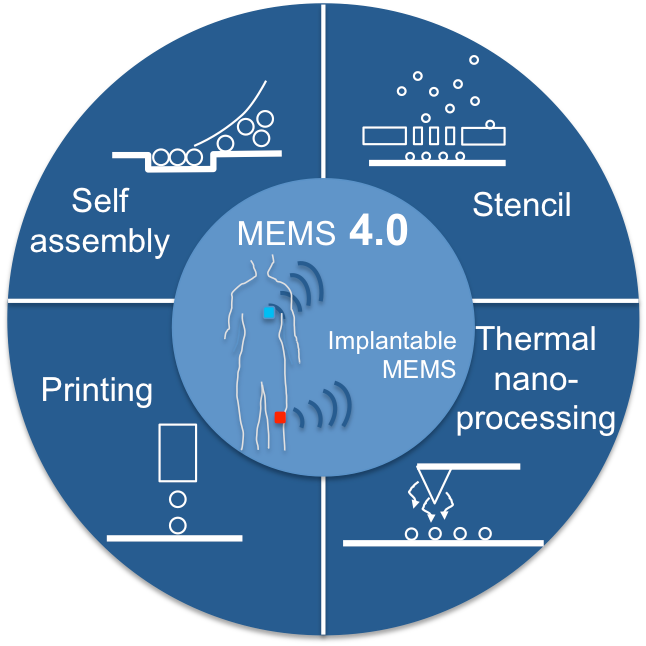
Progress
Along the main topics of this project, a brief overview of our recent research progress is listed in the following paragraphs:
1. Stenciling
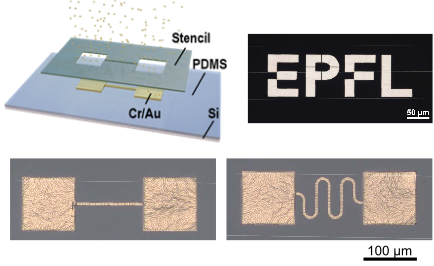
Microstencils have been fabricated by electron beam lithography (EBL) and deep-UV (DUV) lithography and benchmarked for various application purposes including for usage on biocompatible substrates. Metallic micro/nanostructures were stenciled onto biocompatible stretchable materials leading to the discovery of an original method to create large-scale liquid metal structures on stretchable biocompatible substrates. These liquid metal structures are investigated as versatile strain gauges for polymeric MEMS.
2. Printing
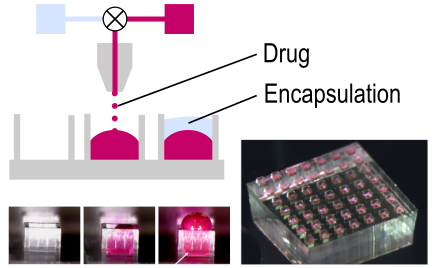
One of the challenges in drug delivery systems is to encapsulate the active substance in order to protect it from deterioration. We have developed an innovative approach for encapsulation of liquid drugs in a biocompatible micro-container to prevent evaporation of the liquid media (i.e. water). The encapsulation media and the drug are sequentially inkjet printed into a reusable template, followed by UV curing of the encapsulation layer.
3. Self-assembly
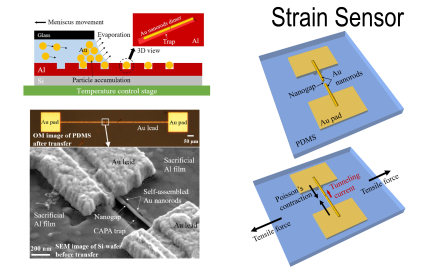
An electron-tunneling based strain sensor has been developed. The sensor has the following three characteristics: i) it is built on a stretchable biocompatible substrate poly(dimethylsiloxane) (PDMS) which makes it useful for wearable or implantable devices, ii) the strain-sensitive electrical signal is measured through two self-assembled gold nanorods separated by a distance of less than 2 nm, iii) a slick device design transforms the macroscopic strain of the PDMS into a sub-Ångström displacement which can be detected through a change in the electron-tunneling current.
4. Thermal nanoprocessing
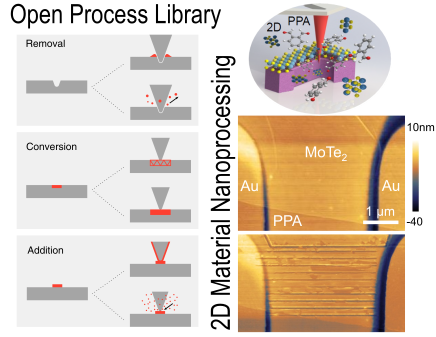
Thermal nanoprocessing of sub-100-nm structures through t-SPL is an emerging digital manufacturing technique. We have explored different ways to directly modify materials with a heated tip i.e. by annealing, melting or chemical modification. It was found that direct manipulation of 2D materials is an extremely compelling and versatile application of t-SPL. We have used t-SPL to locally cut 2D materials such as MoS2 or MoTe2 into arbitrary shapes [Liu et al. Adv. Mater. 2020, (accepted)]. A comprehensive thermal nano-processing library was published as an open-access review article.
5. Implantable biodegradable MEMS
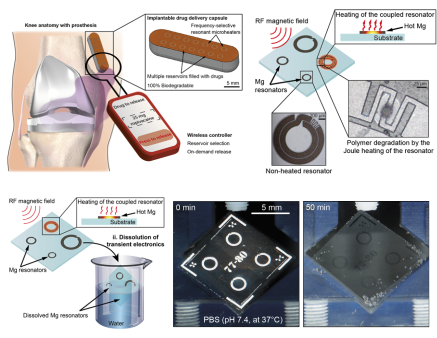
We fabricated implantable biodegradable capsules for wireless controlled drug release made from biodegradable elastomers poly(glycerol sebacate) (PGS) and poly(octamethylene maleate (anhydride) citrate) (POMaC) by an innovative imprinting process. The 10 x 10 x 20 mm3-sized drug containers accommodate up to six isolated reservoirs to be loaded separately with a drug. The capsules were covered with biodegradable membranes equipped with wirelessly powered microheaters that can be each addressed individually to release mL volumes of liquid drugs in each compartment separately. Wirelessly triggered release of the drug by breaking the membrane through heating was demonstrated, posing a significant step towards power receivers and microheaters for a variety of biodegradable implantable medical devices [M. Rüegg PhD Thesis EPFL 2020].
Publications
Please note that the publication lists from Infoscience integrated into the EPFL website, lab or people pages are frozen following the launch of the new version of platform. The owners of these pages are invited to recreate their publication list from Infoscience. For any assistance, please consult the Infoscience help or contact support.