Mechanical Metallurgy Laboratory (LMM)
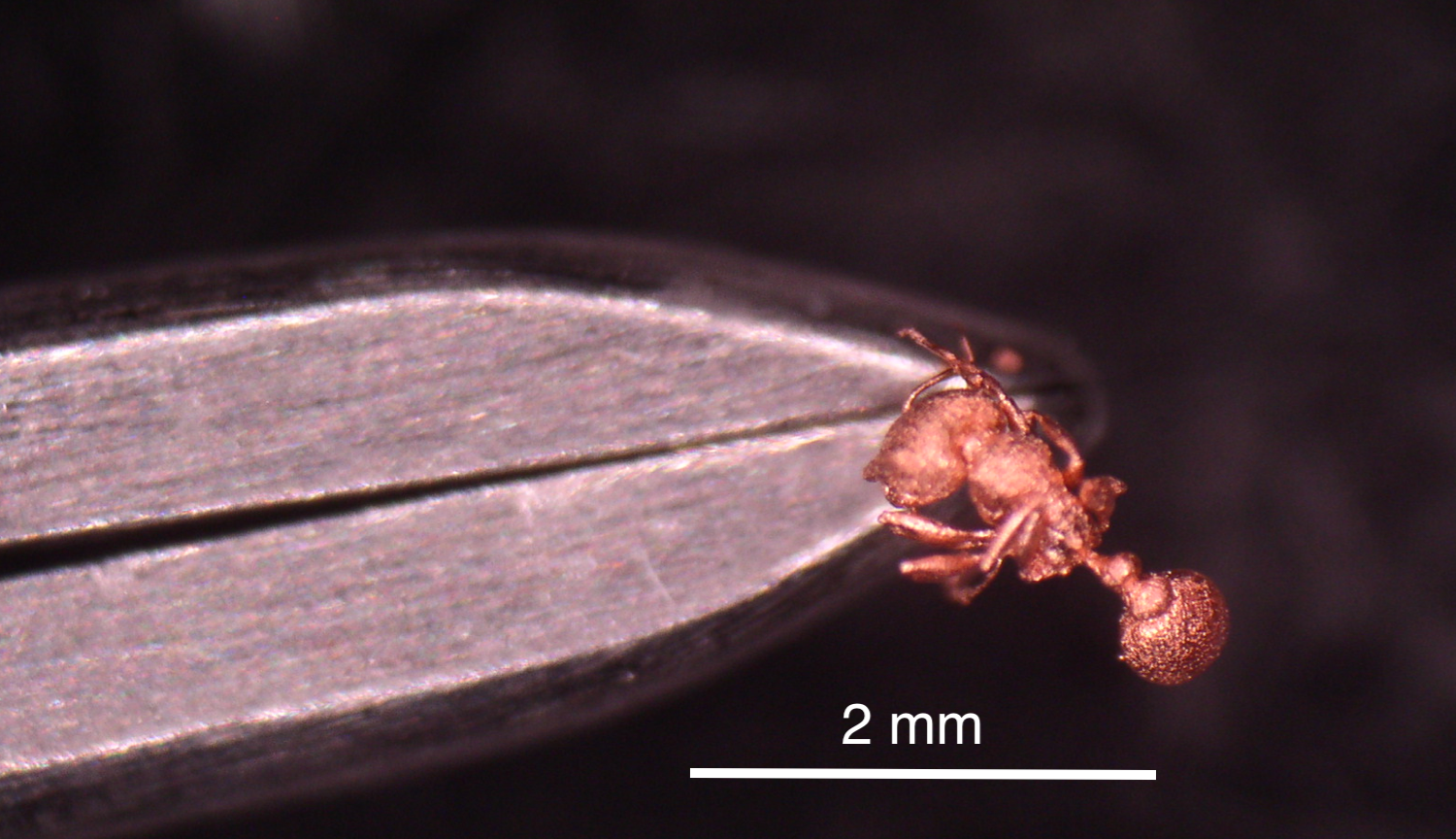
Research at the Laboratory of Mechanical Metallurgy addresses the science and engineering of advanced metallic materials.
Our activities and interests span the entire spectrum from materials processing to the exploration of links between the microstructure and the properties of materials. Materials we study are made at least in part of metal and can be destined for structural or for functional applications.
Our approach is largely but not exclusively experimental and touches upon a number of subtopics of materials science. These include capillarity, infiltration, powder densification, phase transformations including solidification, composite and cellular materials, micromechanics, damage and fracture, dislocational plasticity and creep, and the physics of conduction.
Our current projects
Titanium matrix composites produced by electro-sinter-forging
This project is a collaboration between our laboratory and EPoS Technologies SA,
a company located in Switzerland, which has developed a novel field assisted sintering process called Electro-sinter-forging (ESF), by means of which unique metal matrix composite structures can be produced. We explore ESF process capabilities for the production of titanium matrix composites. This comprises the design and production of new materials in collaboration with EPoS, the in-depth study of resulting materials for their microstructural development, and their characterization for mechanical behaviour. General goals of the project are to design novel, high-performance titanium matrix composites for structural applications, and to contribute to our understanding of the links between composition and process parameters on one hand, and resulting microstructures and mechanical properties on the other hand, of metal matrix composite materials produced by the electro-sinter-forging process.
Harnessing Melt Pool Dynamics in Additive Manufacturing
We aim to show that the additive manufacturing of metallic parts can be achieved by ducting metal in liquid form to produce a small pendular drop that bonds and solidifies onto the solid surface to be built, as is now practiced with thermoplastic polymers. To reach this goal we plan to harness the flow of liquid metal with magnetic body forces that are created when a Tesla-strong magnetic field is imposed in the region of metal deposition and solidification. Magnetic fields indeed make it possible to exert, without contacting the melt, body forces in flowing molten metals that are commensurate with that of gravity and can be used together with capillary forces to harness the flow of molten metal as it contacts, and bonds onto, a 3D printed solid. Magnetic fields have additionally been documented to affect the solidification of metal alloys: this opens the possibility that they may also be used to improve the microstructural development of additively manufactured metallic materials, a proposition that is supported by a few recent publications.
This project is carried by a team comprising, beyond permanent staff of our laboratory, three doctoral candidates (William Le Bas, Tyler Benkley and Xiaojiao You) and one postdoctoral associate (Dr. Julie Gheysen). This team will be joined in February 2025 by a second postdoctoral researcher.
Structure and micromechanics of inclusions in ferrous alloys
In this project we aim at addressing the mechanical properties of oxide inclusions embedded in an iron matrix, as well as the inclusion-matrix interface characteristics. The elastic modulus, hardness and strength of oxides generated within an iron melt and produced in our laboratory will be addressed using nanoindentation techniques as well as testing procedures developed at LMM during previous projects.