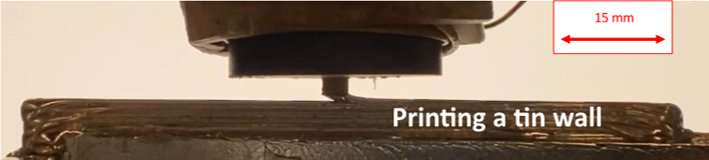
Most of the additive manufacturing processes that are used nowadays to fabricate metallic materials solidify the material onto itself from within a small travelling molten metal pool that is produced by means of a high energy source such as a laser, an electron beam or a plasma. The high intensity of those energy sources gives current metal 3D printing processes an elevated carbon footprint and results in complex and turbulent melt pool dynamics, which cause pores to appear stochastically in the built solid. We aim to show that the additive manufacturing of metallic parts can be achieved via a less turbulent and less energy-intensive approach, in which metal is ducted in liquid form to produce a small pendular drop that bonds and solidifies onto the solid surface to be built, as is now practiced with thermoplastic polymers.
We propose that this can be achieved by harnessing the flow of liquid metal with magnetic body forces that are created when a Tesla-strong magnetic field is imposed in the region of metal deposition and solidification. Magnetic fields indeed make it possible to exert, without contacting the melt, body forces in flowing molten metals that are commensurate with that of gravity and can be used together with capillary forces to harness the flow of molten metal as it contacts, and bonds onto, a 3D printed solid. Magnetic fields have additionally been documented to affect the solidification of metal alloys: this opens the possibility that they may also be used to improve the microstructural development of additively manufactured metallic materials, a proposition that is supported by a few recent publications.
This project has begun with the development of an apparatus by means of which the magnetically harnessed, direct deposition and bonding of molten metal onto a 3D printed wall of solid is implemented and used to study (i) melt pool dynamics and (ii) the material that is thus printed. Work focused on aluminium alloys starting with Al-Cu alloys. Melt pool dynamics are to be studied experimentally by direct, in-situ imaging of the metal deposition process, and theoretically using magnetohydrodynamic simulations conducted in collaboration with Prof. P. Ricci of the EPFL-based Swiss Plasma Center. Deposited material is to be studied for its microstructure and mechanical properties, with an aim to link process conditions with the quality and performance of printed alloys. These thrusts will be the basis of three doctoral theses, which will form the organisational backbone of the project.
This project is carried by a team comprising, beyond permanent staff of our laboratory, three doctoral candidates (William Le Bas, Tyler Benkley and XiaoJiao You) and a postdoctoral associate (Dr. Julie Gheysen).

(Portrait by Gilles Nahon, Lausanne,Switzerland)