La fusion sélective par laser (ou LPBF pour Laser Powder Bed Fusion) est un processus de fabrication additive dans lequel la pièce est construite couche par couche à partir d’une poudre métallique, céramique ou polymère. L’un des avantages majeurs du procédé LPBF est la possibilité de construire des pièces avec des géométries très complexes (structures en treillis, canaux de refroidissement conformes, petites caractéristiques, etc.)
En revanche, une des principales limitations réside dans les contraintes résiduelles en tension qui s’accumulent pendant la phase de construction. Ces contraintes entraînent une diminution de la durée de vie en fatigue de la pièce ou peuvent même provoquer un délaminage et faire échouer la phase de construction.
Le grenaillage laser 3D est un procédé breveté par le LMTM, qui combine le grenaillage au laser (Laser shock peening ou LSP) avec la LPBF, dans le but de diminuer les contraintes résiduelles en traction pendant la phase de construction et de créer des pièces avec un champ de contraintes résiduelles sur mesure, c’est-à-dire des pièces qui ont des contraintes résiduelles en compression bénéfiques dans la région proche de la surface. Dans la figure 1 un changement clair peut être observé du comportement à la traction à l’état brut (valeurs positives des contraintes résiduelles = tension), vers les contraintes de compression de pièces traitées avec différents paramètres LSP (valeurs de contraintes négatives = compression), qui améliorent les propriétés mécaniques et augmentent la durée de vie en fatigue.
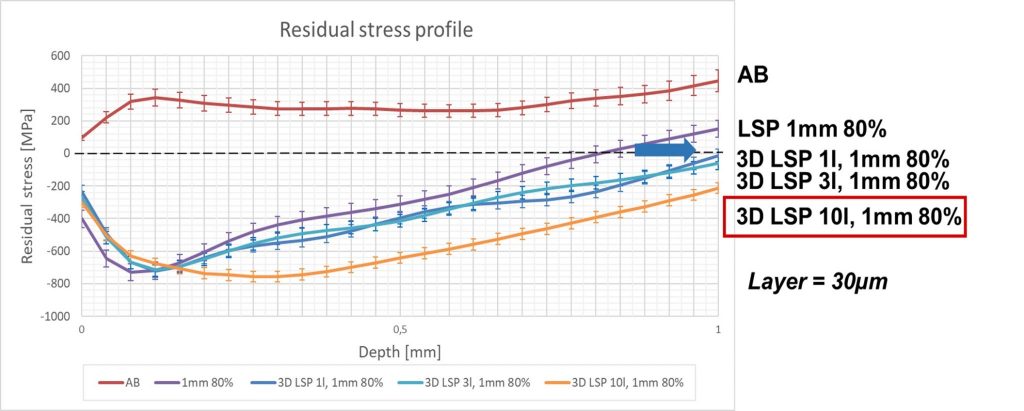
Avec une telle approche, nous avons démontré une augmentation de la durée de vie des pièces produites de plus de 14 fois par rapport aux pièces à l’état brut (figure 2) [2], une réduction des fissures de plus de 95% [3], une réduction des distorsions de plus de 75% [4], ainsi que la possibilité d’adapter de manière sélective la microstructure [5], augmentant ainsi à la fois le champ des matériaux pouvant être produits par la fabrication additive métallique et leur domaine d’application.
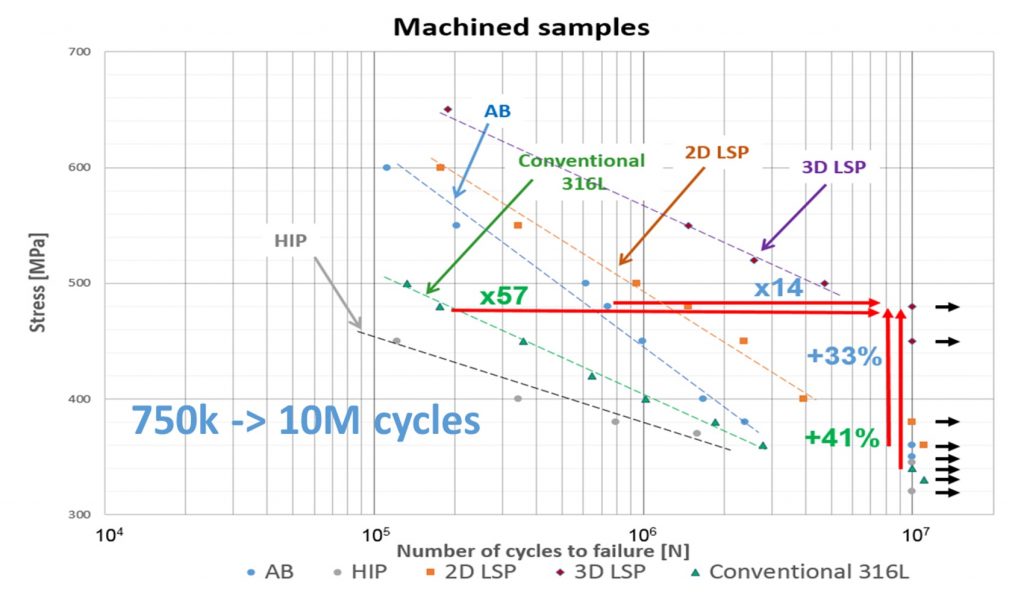
[1] N. Kalentics et al., “3D Laser Shock Peening – A new method for the 3D control of residual stresses in Selective Laser Melting,” Mater. Des., vol. 130, pp. 350–356, Sep. 2017, doi: 10.1016/j.matdes.2017.05.083.
[2] N. Kalentics, M. O. V. de Seijas, S. Griffiths, C. Leinenbach, and R. E. Logé, “3D Laser Shock Peening – A new method for improving fatigue properties of Selective Laser Melted parts,” Addit. Manuf., p. 101112, Feb. 2020, doi: 10.1016/j.addma.2020.101112.
[3] N. Kalentics et al., “Healing cracks in selective laser melting by 3D laser shock peening,” Addit. Manuf., vol. 30, p. 100881, Dec. 2019, doi: 10.1016/j.addma.2019.100881.
[4] N. Kalentics, A. Burn, M. Cloots, and R. E. Logé, “3D laser shock peening as a way to improve geometrical accuracy in selective laser melting,” Int. J. Adv. Manuf. Technol., vol. 101, no. 5, pp. 1247–1254, Apr. 2019, doi: 10.1007/s00170-018-3033-3.
[5] N. Kalentics, K. Huang, M. Ortega Varela de Seijas, A. Burn, V. Romano, and R. E. Logé, “Laser shock peening: A promising tool for tailoring metallic microstructures in selective laser melting,” J. Mater. Process. Technol., vol. 266, pp. 612–618, Apr. 2019, doi: 10.1016/j.jmatprotec.2018.11.024.