La fusion laser sur lit de poudre (ou LPBF pour Laser Powder Bed Fusion) est un processus de fabrication additive dans lequel la pièce est construite couche par couche à partir d’une poudre métallique, céramique ou polymère. L’un des avantages majeurs du procédé LPBF est la possibilité de construire des pièces avec des géométries très complexes (structures en treillis, canaux de refroidissement conformes, petites caractéristiques, etc.).
Les échantillons métalliques produits par LPBF peuvent atteindre une densité presque complète et une résistance élevée. Cependant, pour éviter que des défauts – porosités, fissures et accumulation de contraintes résiduelles – ne détériorent la qualité des pièces, un ensemble approprié de paramètres doit être optimisé. Les solutions expérimentales reposent sur des méthodes empiriques longues et coûteuses. Toute modification mineure des paramètres du procédé ou des conditions environnementales peut avoir un impact direct et significatif sur la qualité de la pièce. Ce manque de répétabilité, en plus de la nature probabiliste de la formation des défauts, limite les applications de cette technologie. Par conséquent, la surveillance et le contrôle en ligne sont d’un grand intérêt et plusieurs approches sont étudiées pour résoudre ce problème.
Une solution proposée dans ce projet surveille le procédé via des capteurs acoustiques et des algorithmes avancés d’intelligence artificielle. Ces derniers nécessitent suffisamment de données étiquetées ainsi qu’une compréhension fondamentale du processus. Le projet propose de relier les paramètres du procédé LPBF aux propriétés des matériaux, à la caractérisation des défauts, aux simulations multi-échelles et à la surveillance in situ en temps réel. Les résultats seront les informations d’entrée des cadres d’intelligence artificielle, développés au LAMP de l’Empa à Thoune. Le but est de progresser dans l’optimisation automatisée du processus afin d’atteindre la fabrication «zéro défaut».
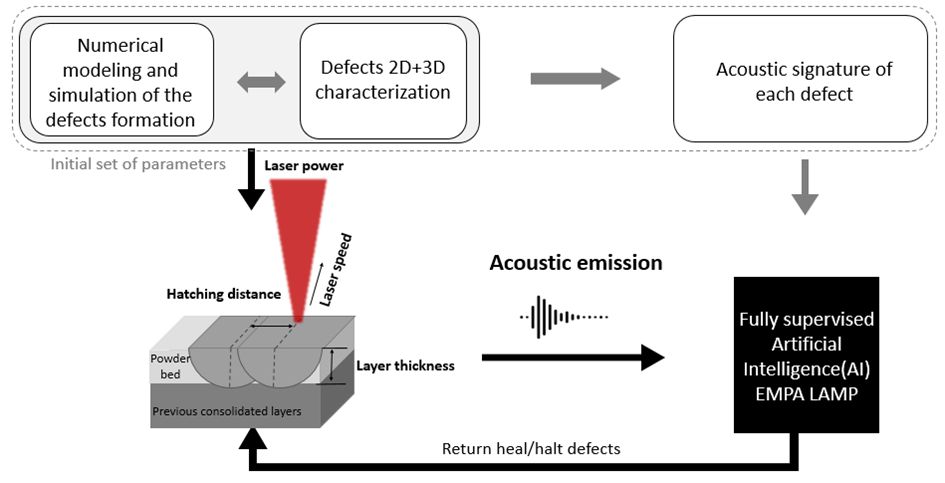