Laser Powder Bed Fusion (LPBF) is an additive manufacturing process in which the part is built layer by layer out of a metallic, ceramic or polymer powder. One of the biggest advantages of the LPBF process is the ability to build parts with very complex geometries (lattice structures, conformal cooling channels, small features, etc.).
Metallic LPBF samples can achieve near full-density and high resistance. However, to prevent defects – porosity, cracks, and accumulation of residual stress – from deteriorating the work-pieces quality, an appropriate set of process parameters must be optimized. Experimental solutions rely on costly and time-consuming trial and error methods. Any minor changes of process parameters or environmental conditions can have a direct and significant impact on the quality of the part. This lack of repeatability, in addition to the probabilistic nature of defect formation, limits this technology’s applications. Hence, online monitoring and control are of great interest and several approaches are studied to solve this problem.
A proposed solution in this project monitors the process via acoustic sensors and state-of-the-art artificial intelligence frameworks. The latter requires sufficient labeled data as well as a fundamental understanding of the process. The project proposes to link the LPBF process parameters with materials properties, defect characterization, multiscale simulations, and real-time in situ monitoring. The results will be the input information of the artificial intelligence frameworks, developed at LAMP at EMPA in Thun. The goal is to advance further in the automated optimization of the process such as to reach “zero defect” fabrication.
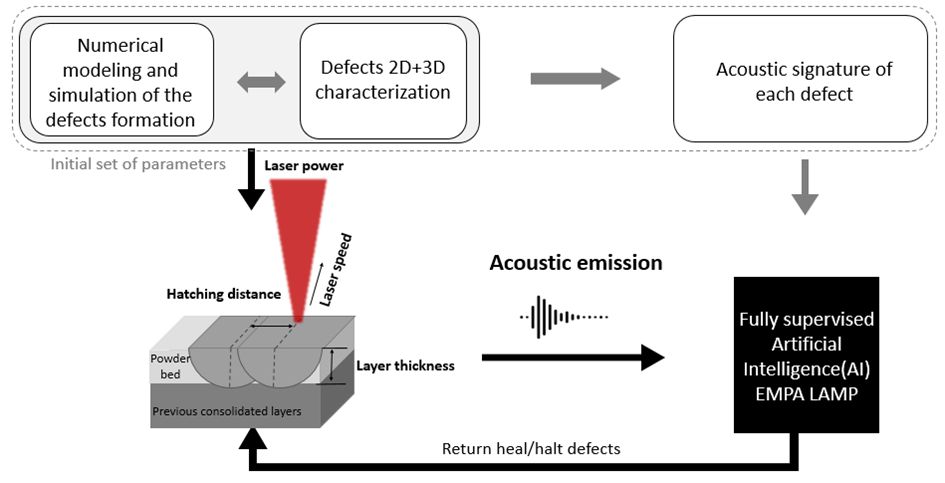