Bulk Metallic Glasses (BMGs) are known for their excellent mechanical properties, provided they retain the amorphous structure inherited from a sufficiently high cooling rate from the melt. Due to the lack of defects such as grain boundaries and dislocations, BMGs possess high hardness and strength, excellent wear resistance, and a high elastic limit, usually combined with a low Young’s modulus. Applications range from jewelry to electronics and sports goods. One of the main drawbacks of BMGs’ conventional production methods, such as casting and melt spinning, is the size limit and the restriction to simple shapes. When the size of the cast sample exceeds the so-called critical casting diameter of the alloy, crystallization is initiated, which generally has an adverse effect on the mechanical properties. Thus, the widespread use of BMGs in the industry is limited by the lack of possibilities to manufacture large BMG samples with complex shapes.
Recently, laser-based additive manufacturing (AM) methods have been used to produce BMGs via the high cooling rate provided by laser processing. The most used AM method has been Laser Powder-Bed Fusion (LPBF). LPBF has several advantages over conventional manufacturing methods, such as the possibility to build parts with complicated geometries, minimal feedstock waste and no size limitation. Since the interaction between the laser and the deposited powder is short and confined to a small volume, the local cooling rate can reach 103–108 K/s, which is typically higher than the critical cooling rate of most BMGs.
We characterized printed Zr-based BMG (AMZ4) samples and detected nanocrystals via synchrotron X-ray diffraction (XRD) and field-emission scanning electron microscopy (FESEM) (see Fig. 1). The crystallization was explained from analysis of numerical finite element modeling (FEM) (see Fig. 2) and fast differential scanning calorimetry (FDSC) investigations. We measured the physical and mechanical properties of the samples, and found that despite the presence of nanocrystals in the amorphous structure, compressive and flexural strength, nano- and micro-hardnesses, and wear resistance were excellent (see Fig. 3). We also printed a benchmark with complicated geometrical features and (see Fig. 4) demonstrated an excellent dimensional accuracy for these printed structures. Potential applications include sporting goods or medical devices, for which properties are competitive with those of crystalline metals and carbon-fiber-reinforced polymer (CFRP) composites (see Fig. 5). The various results show that LPBF is an excellent choice for the fabrication of complex BMG parts, with no required post-processing steps, except for surface finishing.
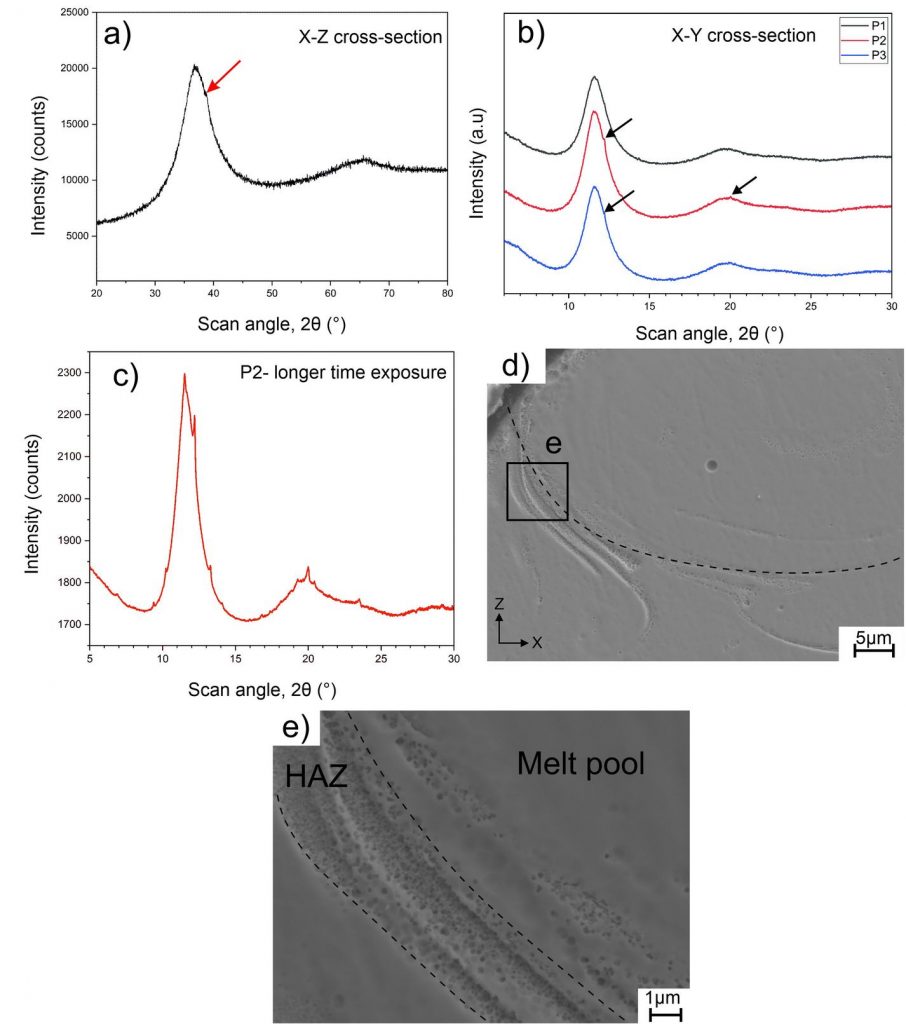
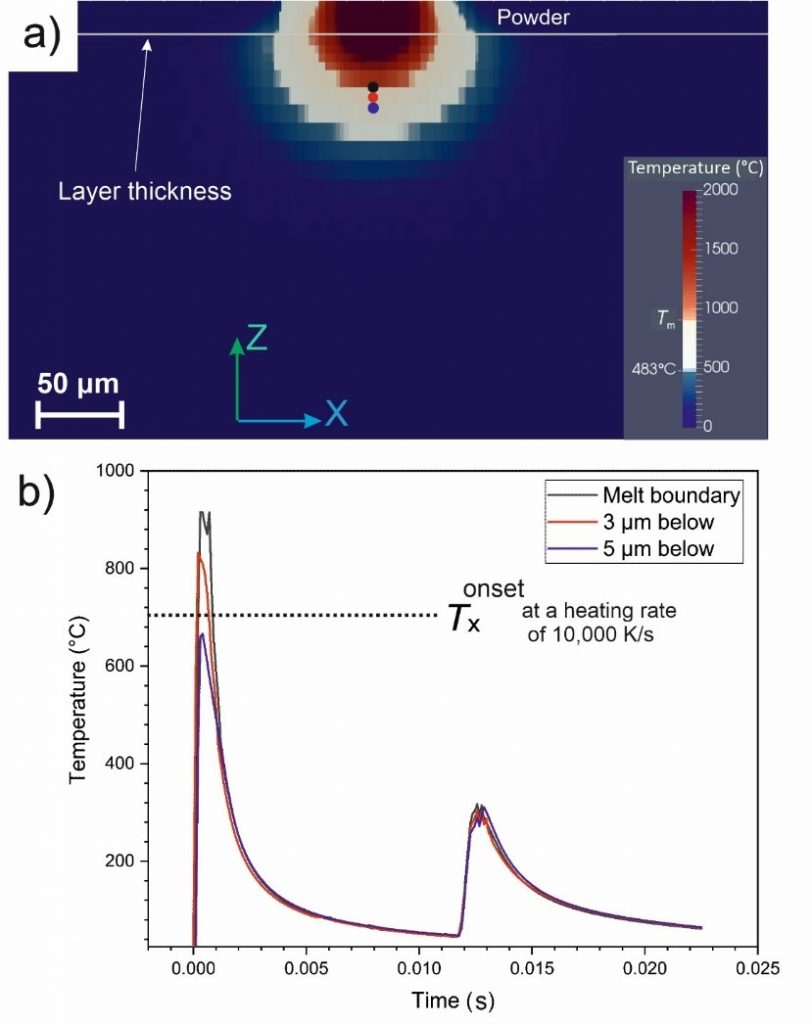
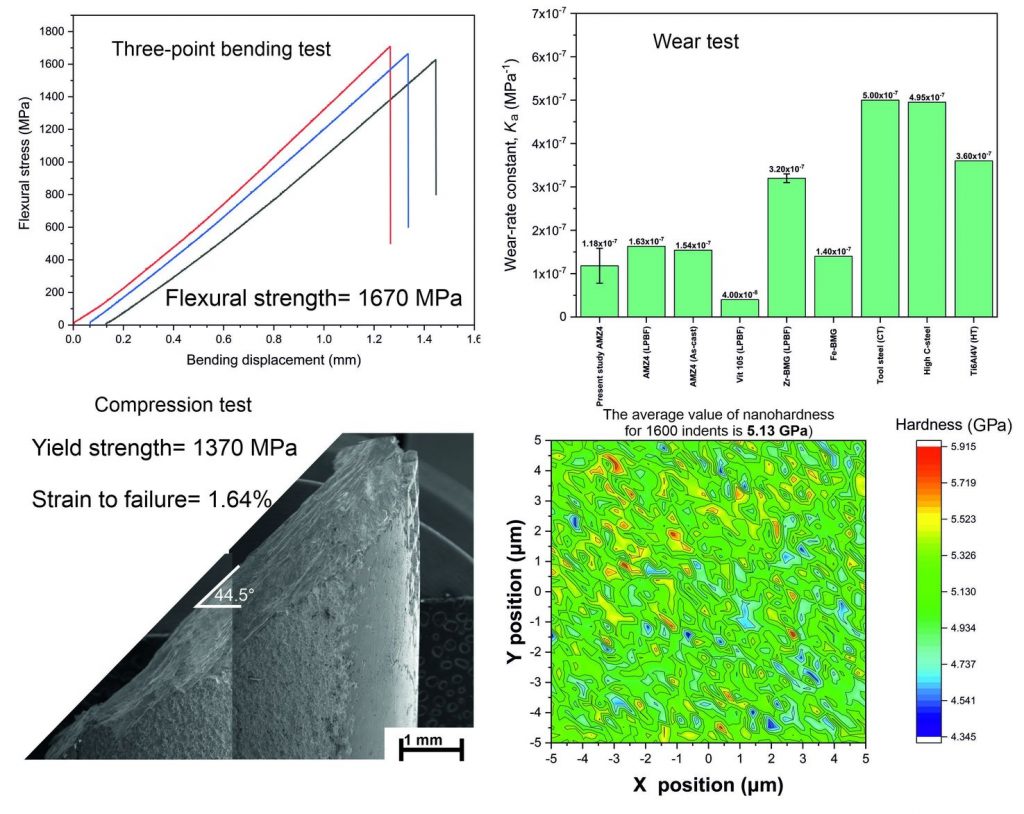
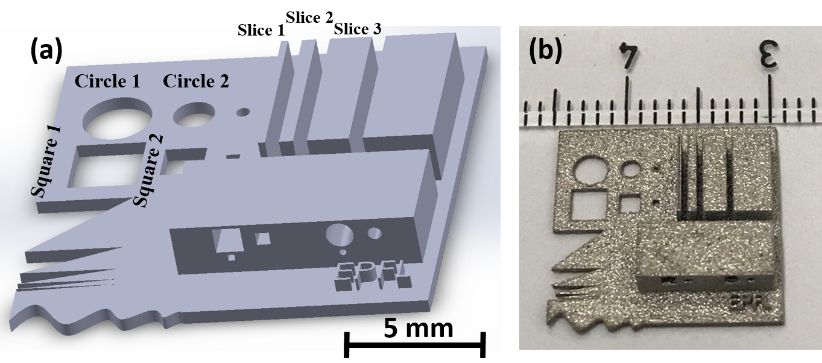
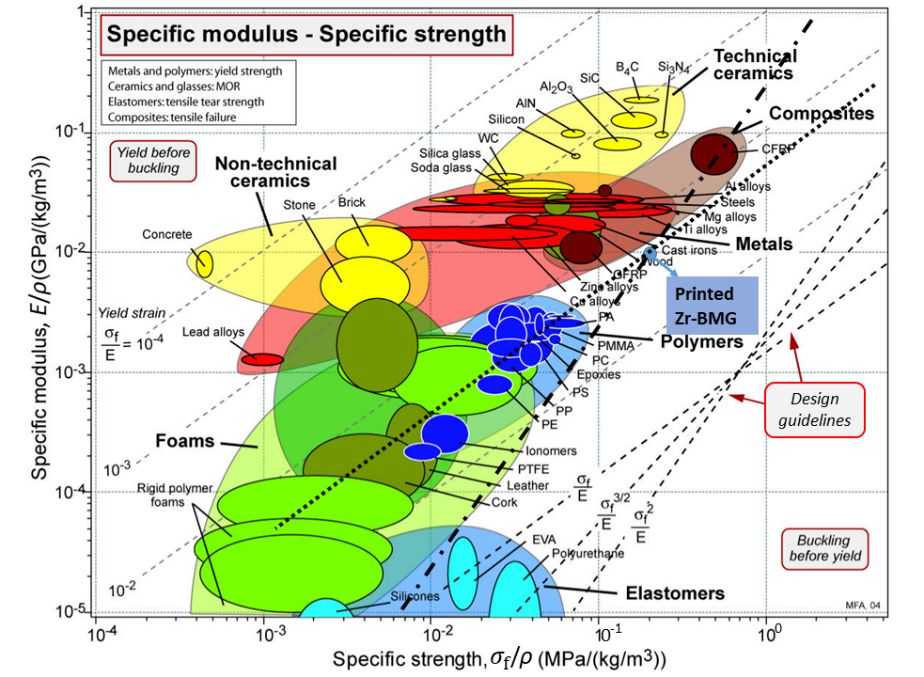
References:
[1] N. Sohrabi, J. Jhabvala, G. Kurtuldu, M. Stoica, A. Parrilli, S. Berns, E. Polatidis, S. Van Petegem, S. Hugon, A. Neels, J.F. Löffler, R.E. Logé, Characterization, mechanical properties and dimensional accuracy of a Zr-based bulk metallic glass manufactured via laser powder-bed fusion, Mater. Des. 199 (2021) 109400. doi:https://doi.org/10.1016/j.matdes.2020.109400.
[2] N. Sohrabi, R.S. Panikar, J. Jhabvala, A.R. Buch, S. Mischler, R.E. Logé, Laser coating of a Zr-based metallic glass on an aluminum substrate, Surf. Coatings Technol. 400 (2020). doi:https://doi.org/10.1016/j.surfcoat.2020.126223.
[3] N. Sohrabi, J.E.K. Schawe, J. Jhabvala, J.F. Löffler, R.E. Logé, Critical crystallization properties of an industrial-grade Zr-based metallic glass used in additive manufacturing, Scr. Mater. 199 (2021) 113861. doi:https://doi.org/10.1016/j.scriptamat.2021.113861.
[4] N. Sohrabi, J. Jhabvala, G. Kurtuldu, R. Frison, A. Parrilli, M. Stoica, A. Neels, J.F. Löffler, R.E. Logé, Additive manufacturing of a precious bulk metallic glass, Appl. Mater. Today. 24 (2021) 101080. doi:https://doi.org/10.1016/j.apmt.2021.101080.