The ultimate autonomous smart wearable system is a device in which all parts are seamlessly integrated. Due to the recent strong progress in the field of 3D printing, it is becoming ever easier to develop systems integration strategies and novel structural and functional elements. In order to introduce smart features into 3D printed customized wearables, it is necessary to integrate the printing of functional layers and sensing components directly into a flexible process chain.
Our approach, called digital manufacturing, allows for new design possibilities of smart objects which are made available by the use of digitally driven 3D printing techniques. Complex digitally manufactured sensors and systems could be introduced by fabricating stacks of multiple functional layers within 3D space. Other added benefit is that digital manufacturing enables easy customization, self-packaging and seamless integration into pre-existing products.
D-SENSE aims to solve one key challenge of integration of sensors into smart objects: Enabling the integration of functional sensing layers into the fabrication process of 3D-printed constructs. The objective is to apply digital printing of functional and structural inks targeting the whole processing in a single tool.
In this fashion, smart wearable systems can be developed for robots and humans alike. Demonstration will happen through the fabrication of smart prosthesis, developed through the collaboration between the partners, which will integrate physical and mechanical sensors able to communicate their readout wirelessly. These smart prosthesis will in effect be smart revalidation monitoring systems which can be conformably worn on the skin.
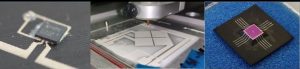
First 3D printed elastomeric capacitive, piezoresistive, and triboelectric sensors prototypes have been produced. Transfer and embedding of silicon components, SMDs and Si chips for the electronic and wireless communication, has also been demonstrated into 3D printed parts.
Soft piezoresistive sensors have been produced for measurement of normal and shear forces based on silicon composites both for the structural materials (i.e. with cellulose) and the sensing material (i.e. with carbon particles).
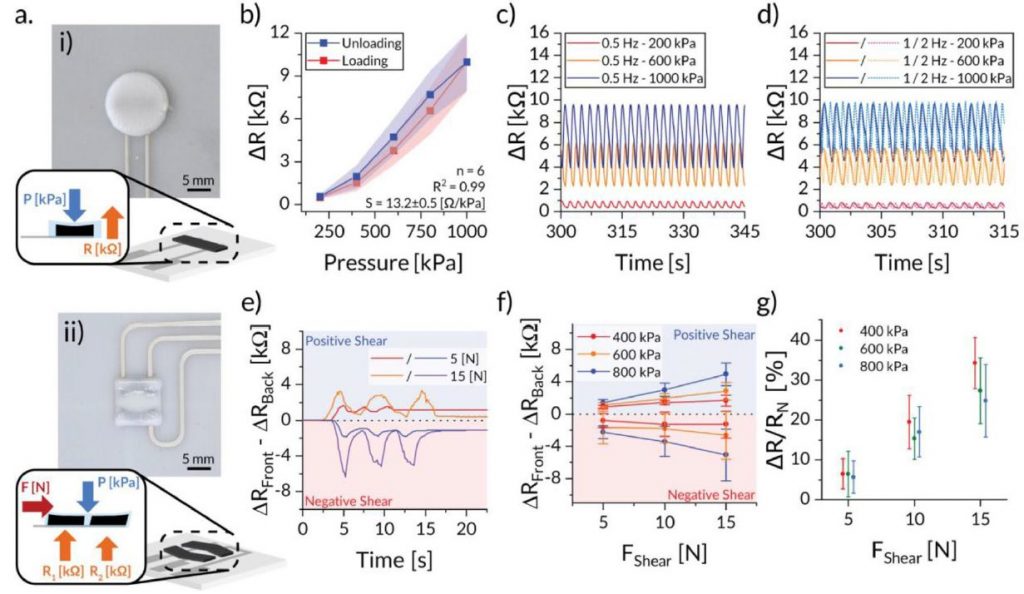
These sensors have been implemented in fully digitally fabricated insole using direct ink writing (DIW) and performed in a single integrated processing tool. The technology allows customization of the wearable in terms of shape, rigidity, and sensors placement, this according to the needs of the user.
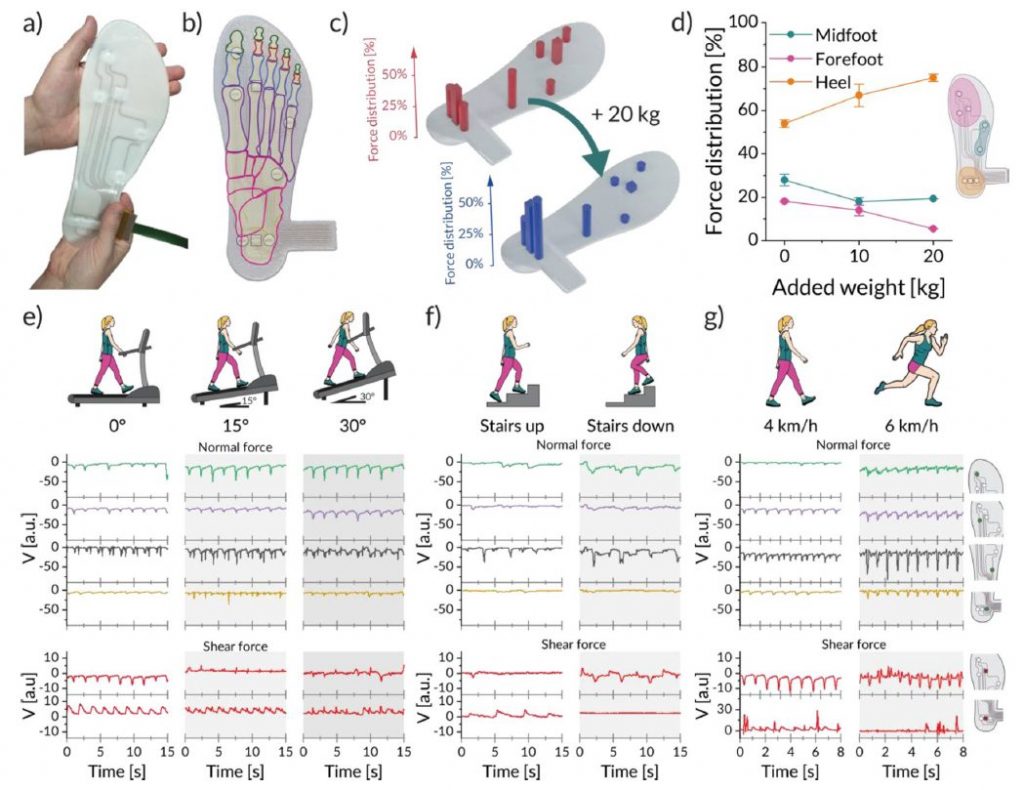
Project funding and partners
The project, named D-SENSE, is funded by the Strategic Focus Area (SFA) Advanced Manufacturing program and is executed in collaboration with the following partners whom all have their own focus:
- EPFL on the digital printing of sensors embedded in the 3D printed structures;
- EMPA on the inks formulation for 3D printing;
- ETHZ on 3D/4D printing of polymer nanocomposites;
- CHUV and NUMO AG as applicative partner for rehabilitation and sports usage.
Scientific publications
M. R. Binelli, R. van Dommelen,Y. Nagel, J. Kim, R. I. Haque, F. B. Coulter, G. Siqueira, A. R. Studart, D. Briand, Digital manufacturing of personalised footwear with embedded sensors, Scientific Reports, (2023) 13:1962.
R. van Dommelen, R. I. Haque, O. Chandran, S. Lani, D. Briand, In-situ laser sintering for the fabrication of fully 3D printed electronics composed of elastomeric materials, Flexible and Printed Electronics, 6 (2021) 045003.
Contact