We have developed a high force density textile electrostatic clutch, that enables new applications in soft and wearable haptic feedback, teleoperation, and in robotics. We have integrated it into thin gloves and sleeves, allowing us to block motion of selected body location rapidly and silently.
Our most recent work was published in 2022 in Advanced Intelligent Systems. This research build on our textile-based clutch reported in Advanced Materials Technologies in December 2019 , which itself builds on our earlier DextrES project with ETHZ-AIT. Main EPFL contributor: R. Hinchet
![]() |
![]() |
![]() |
Electrostatic clutch for wearable applications:
Clutches are key elements for blocking or coupling motion in wearable systems. Electrostatic clutches are compact and light, making them particularly well-suited for wearable applications:
- Haptic clothing: for instance blocking fingers’ motion to provide kinesthetic haptic feedback when grabbing virtual objects in virtual reality.
- Textile-based robots and soft exoskeletons
- Rehabilitation equipment
The textile integration allows for ultralight and highly flexible clutches which increases comfort and facilitates integration on body and clothing.
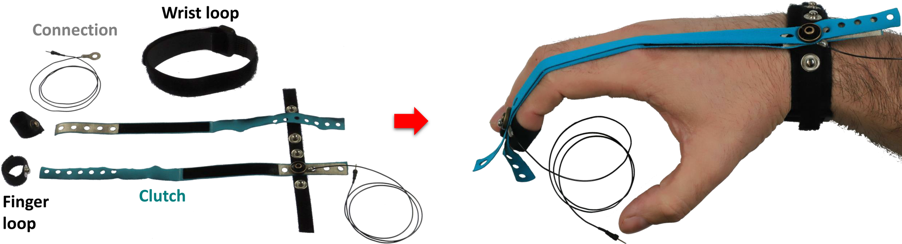
Haptic kinesthetic feedback glove
Kinesthetic haptic feedback is a field of rapidly growing importance, for instance, in VR, actively blocking a user’s fingers’ motion to give the user the convincing feeling that virtual objects are solid or compliant. Our variable friction device allows a brick to feel solid, and a sponge to feel soft.
How does the electrostatic clutch work?
Electrostatic clutches are variable capacitors. They are made of two flexible and partially overlapping electrodes separated by a thin insulator, and possibly by an air gap. The electrodes can slide with respect to each other. When the voltage difference between the electrodes is zero, there is no electrostatic attraction between the electrode, and they slide freely. When a voltage is applied between the electrodes, electrostatic attraction pulls them together. This electrically-controlled normal force increases the sliding (or shear) frictional forces between the strips, impeding or fully blocking the sliding motion. The frictional force between electrodes is proportional to the square of the applied voltage.
By careful choice of dielectric materials and processing methods, our electrostatic clutch generates very high frictional shear stress up 20 N.cm-2 (>2 kg) when actuated at 300 V but using only 1 mW.cm-2. Actuation and release time are less than 15 ms. The clutch is thin, highly flexible and weighs only 30 mg.cm-2 which give it outstanding performances in term of force blocked to mass ratio and force blocked to power consumption ratio.
Comparison of the performance of different electrically driven clutches from literature (figured inspired from Diller, Collins and Majidi, 2018)
For more info:
For more information, please see:
R. Hinchet and H. Shea, “High Force Density Textile Electrostatic Clutch,” Adv. Mater. Technol., p. 1900895, Dec. 2019. https://doi.org/10.1002/admt.201900895
Funding:
We gratefully acknowledge support from the Hasler Foundation Cyber-Human Systems program. We thank Piezotech-Arkema for kindly providing the high-performance P(VDF-TrFE-CTFE) polymers and members of the EPFL-LMTS for helpful discussions.