2023 – 2025
Nour Halawani, Feyza Karasu and Yves Leterrier

This project aims to develop a biobased, photocurable, and biodegradable composite ink tailored for compostable film materials, to enhance their mechanical robustness without compromising their compostability. The research work includes the formulation and coating of sustainable alternatives to oil-derived resins using biobased precursors, extensive mechanical and biodegradation testing, and scale-up to pilot industrial conditions. The fundamental challenge is to combine a priori antagonist properties, i.e., mechanical performance and rapid biodegradation. The project achievements hold promise for advancing eco-friendly packaging solutions and reducing reliance on non-renewable resources.
Funding
- Innosuisse 106.535 IP-ENG
Partner
- BioApply Sàrl
Thematics
- Fundamentals of polymers and composite materials processing (process kinetics, UV curing)
- Surfaces and interfaces (bioinspired surfaces, multilayers, adhesion and bonding)
Field
- Sustainable materials (biobased, renewable energy, recycling)
2024 – 2028
Martyn Wakeman, Jean-Baptiste Desbrest, Véronique Michaud
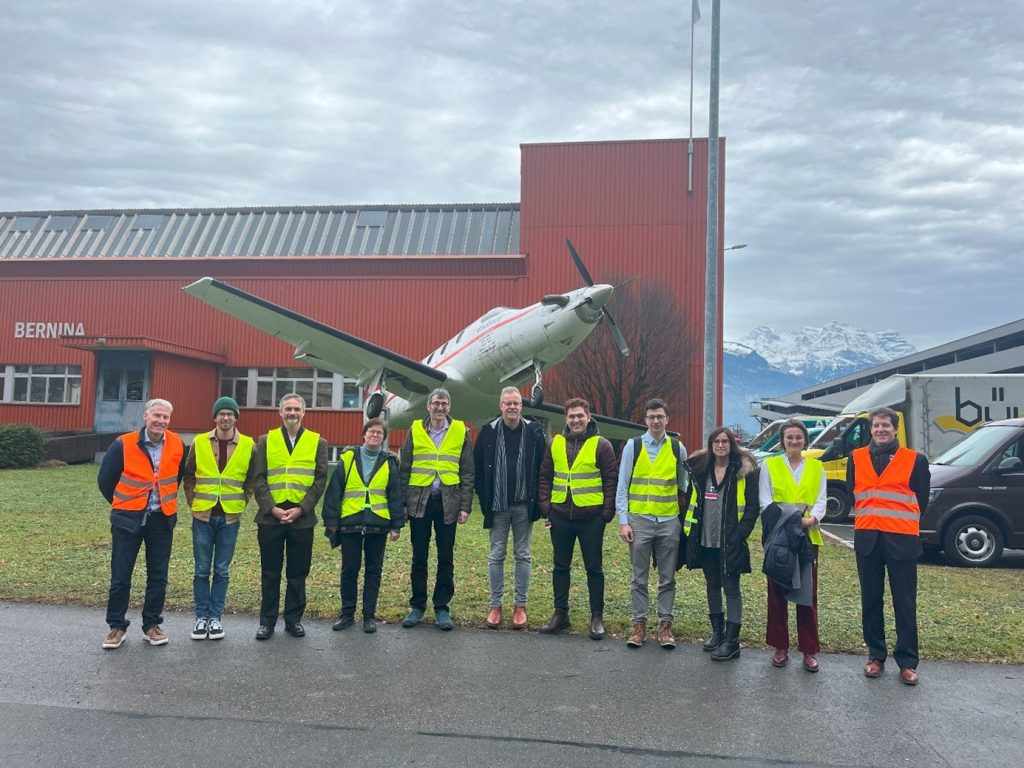
This Innosuisse FLAGSHIP project aims at reducing the environmental impact of plastics in the industry in the context of the NetZero 2050 objectives. LPAC is involved in a subproject that will examine and develop best carbon footprint materials, using innovative approaches to materials, processes, and recycling to minimize the impact of composite materials in various industries.
The focus will also be on the eco-design of parts, anticipating end-of-life scenarios to shift from a linear to a re-wired circular economy model. Additionally, the project will seek to reorganize how materials are sourced and distributed to create a more sustainable industry, involving collaboration with multiple industrial partners.
Funding
- Innosuisse – Flagship project
Partners
- Huntsman Advanced Materials
- Pilatus Aircraft Ltd.
- OST – Eastern Switzerland University of Applied Sciences
- Composite Recycling SA
- Composites Busch SA
Fields
- Mobility (light weighting and cost effectiveness in automotive, rail, aeronautics and space)
- Sustainable materials (best carbon foot print materials, bio-based, renewable energy, recycling)
- NetZero transition strategy modelling (LCA, MFA, finance), circular economy
2023 – 2027
Michele Bonacina, Anthony Hoogmartens, Yves Leterrier and Véronique Michaud

ESPERANTO stands as a Marie Curie Doctoral Network (MSCA-DN) in Europe, where LPAC is a key partner with 2 PhDs. The consortium’s goal is to pioneer innovative sustainable polymer products and technologies by leveraging light-based processes as opposed to conventional, energy-intensive heat methods. One PhD (Michele) focuses on creating bio-based multifunctional coatings using UV-based self-assembly processes to mimic natural surfaces. The focus of the second PhD (Anthony) is to advance the development of light-responsive and recyclable composites through the utilization of photo reversible precursors.
Funding
EU’s Horizon 2021 programme under the Marie Skłodowska-Curie Doctoral Networks (MSCA-DN) grant agreement
University partners
- Politecnico Di Torino
- Université Haute-Alsace
- Montan Universität leoben
- Polymer Competence Center Leoben
- Yildiz Teknik Universitesi
- Université de Montepellier
- Imperial College
Industrial partners
- Logitech
- Adler
- Kansai Helios
- Kayalar
- Microla
- SICPA
- Centre Technique du Papier
Webpage
http://www.horizon-msca-esperanto.eu/
Thematics
- Fundamentals of polymers and composite materials processing (process kinetics, UV and thermal curing)
- Surfaces and interfaces (bioinspired surfaces, multilayers, adhesion and bonding)
- Integration of functions (self-healing ability, self-cleaning, biocompatibility).
Fields
- Biomedical and electronic devices (encapsulation materials, flexible electronics and devices)
- Health and comfort (biocompatible composites, prostheses)
- Sustainable materials (biobased, renewable energy, recycling)
2021-2026
Alper Balkan, Yves Leterrier
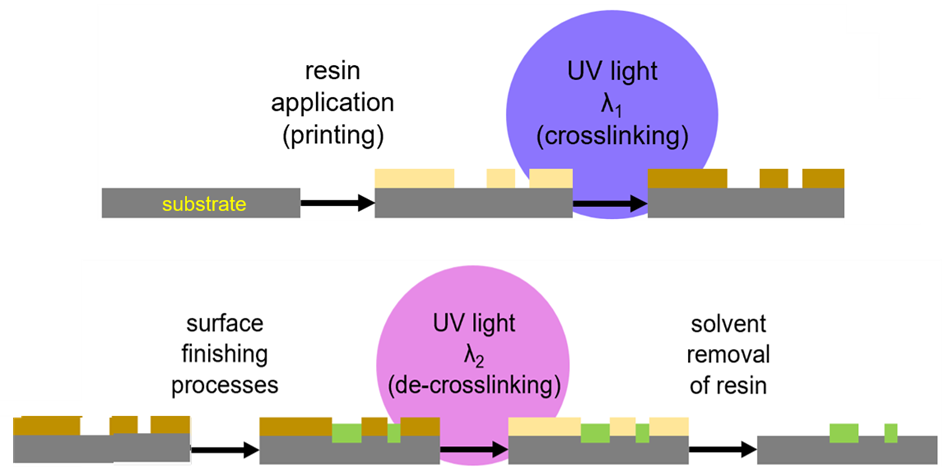
DiPrintProtect aims to develop and process photo-curable composite resins and form robust but temporary coatings on metal substrates that can withstand severe finishing operations and be removed easily. These advanced coatings are to be realized by state-of-the-art digital printing methods for replacing certain manufacturing steps and achieving a more capable and automated watch production procedure. Major challenges are the dispersion of reinforcing particles within the photo-curable resin while maintaining reasonable resin processability as well as optical transparency, the light-assisted de-crosslinking of the composite coating material in a practical time frame using commercially available solvents or other dissolution/delamination methods, the quantitative monitoring of the de-crosslinking process, and the optimization of this coating removal method until “traceless removal” is achieved.
Funding
- Strategic Focus Area – Advanced Manufacturing of the Swiss ETH Board
Project Partners
- Laboratory for Thin Films and Photovoltaics (EMPA)
- Laboratory for Functional Polymers (EMPA)
- Macromolecular Engineering Laboratory (ETHZ)
Industry Partners
- Association Suisse pour la Recherche Horlogère
- The Swatch Group Research and Development Ltd
- Optomec GmbH
- Ciposa S.A.
Webpage
Thematics
- Fundamentals of polymers and composite materials processing (multiphase fluid flow, capillary effects, process kinetics, UV and thermal curing)
- Surfaces and interfaces (bioinspired surfaces, multilayers, adhesion and bonding)
- Integration of functions (smart and piezoelectric composites, self-healing ability, damping, non-linearity, biocompatibility).
Fields
- Sustainable materials (biobased, renewable energy, recycling)
2020 – 2024
Jialiang Fan, Veronique Michaud, Anastasios Vassilopoulos (CCLab)
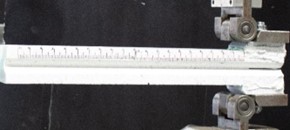
This project is a collaborative project between EPFL (LPAC and CC Lab) and two universities in Belgium (UGhent and VUB). This project proposes a new combined numerical and experimental approach for the materials development, testing and analysis of thick adhesive joints for large scale civil engineering structures, with the case study of wind turbine blades. To achieve these objectives, (i) numerical modelling is used to analyze the local loading conditions of the adhesive under the global loading conditions of the blade, so as to establish a detailed sub-model of this critical part; (ii) experimental characterization of model thick adhesive layers are carried out in static and fatigue complex loading conditions so as to mimic realistic loading cases; (iii) a commercial state of the art adhesive was characterized as a basis for further material development and inclusion of second phases to improve damage tolerance of the adhesive in these specific conditions and provide “healing mechanisms” to prevent crack propagation. At LPAC, we adapted a grooved geometry to test thick adhesive joints in double cantilever beam testing, to achieve cohesive failure under both quasi-static and fatigue loadings. New formulation adhesives with self-healing capabilities are developed to prolong the lifetime of the thick adhesive joints. The new formulation adhesives also fulfill the requirements proposed from manufacturing process, design, and usage phases, such as sufficient rheological yield stress, adequate mechanical properties.
Funding
-
Swiss National Science Foundation (SNF)
-
Research Foundation – Flanders (FWO Vlaanderen)
Project partners
- Composite Construction Laboratory (CCLAB-EPFL)
- Universiteit Gent (BE)
- Vrije Universiteit Brussel (BE)
- Sika Technology AG (CH)
Publications
- Fan, A.P. Vassilopoulos, V. Michaud, Mode I fracture of thick adhesively bonded GFRP composite joints for wind turbine rotor blades, Composite Structures 327 (2024) 117705. https://doi.org/10.1016/j.compstruct.2023.117705.
Fields
- Sustainable materials (biobased, renewable energy, recycling)
Selected past projects
2022 – 2023
Nour Halawani, Véronique Michaud

Glass Fiber Reinforced Plastic (GFRP) is an incredibly versatile material, commonly found in boats, planes, trains, and wind turbine blades. The majority of GFRP waste ends up in landfills, while the rest is either being incinerated or worse, abandoned in the environment. Decades of attempts to recycle GFRP have been unsuccessful, as the economic incentives were not sufficient and the materials not prone to easy recycling. In this project, we have used standard pyrolysis technology which heats up the GFRP in a static oxygen free environment. This removes the plastic from the fibers leaving the fibers slightly damaged during this process, and in a difficult-to-handle form. A lab-scale protocol was thus developed to produce and test a Fiberglass mat from reclaimed fibers. This includes the development of a dispersion method, surface treatment, sizing application, and adhesion promotor, as well as preliminary protocol for mat production, up to composite testing and environmental impact analysis, to identify the main hurdles towards successful implementation.
Funding
- Gebert Rüf Stiftung Innobooster GRS-025/22
Fields
- Sustainable materials (recycling)
2018 – 2023
Helena Teixidó, Jeroen Staal, Baris Caglar, Véronique Michaud
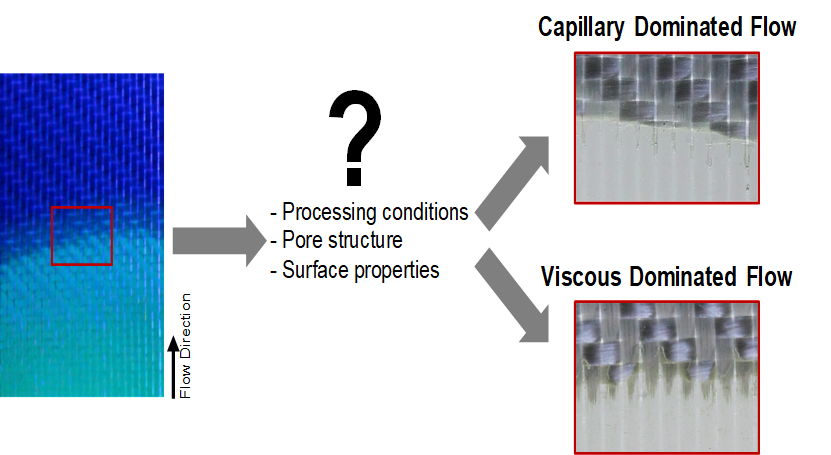
The Dynaflow project aims to probe the dynamics of flow in fibrous porous media, as used in advanced composite materials, by addressing several main points. i) One aim is to further develop the in-situ experimental methods to analyze multiphase flow processing, using advanced and novel techniques available at CSEM to enable the macro-scale observation of dynamic resin flow patterns. ii) Results of macro-scale observations will be coupled with local observation of frozen microstructures using microtomography. iii) The multiscale in-situ experimental data will feed process models that account for multiphase fluid flow effects, extended to velocity-dependent capillary forces and hierarchical pore structures.
Funding
Project partner
- CSEM – Centre Suisse d’Electronique et de Microtechnique SA
Project webpage
Publications
-
Yuksel, Onur; Caglar, Baris; Broggi, Guillaume; Michaud, Véronique; Akkerman, Remko; Baran, IsmetSaturated transverse permeability of unidirectional rovings for pultrusion: The effect of microstructural evolution through compaction. In Polymer Composites, 1–18. https://doi.org/10.1002/pc.28171
-
Staal, Jeroen; Smit, Edgar; Caglar, Baris; Michaud, VéroniqueThermal management in radical induced cationic frontal polymerisation for optimised processing of fibre reinforced polymers. In Composite Science and Technology, 237(May), 110009. https://doi.org/10.1016/j.compscitech.2023.110009
-
Teixidó, Helena; Broggi, Guillaume; Caglar, Baris; Michaud, VéroniqueMeasurement and modelling of dynamic fluid saturation in carbon reinforcements. In Composites part A, 169, 107520. https://doi.org/10.1016/j.compositesa.2023.107520
-
Caglar, B.; Broggi, G.; Ali, M.A.; Orgéas, L.; Michaud, V.Deep learning accelerated prediction of the permeability of fibrous microstructures. In Composites Part A: Applied Science and Manufacturing, 158, 106973. https://doi.org/10.1016/j.compositesa.2022.106973
-
Teixidó, H.; Staal, J.; Caglar, B.; Michaud, V.Capillary Effects in Fiber Reinforced Polymer Composite Processing: A Review. In Frontiers in Materials, 9, 809226. https://doi.org/10.3389/fmats.2022.809226
-
Caglar, Baris; Esposito, William; Nguyen‐Dang, Tung; Laperrousaz, Stella; Michaud, Véronique; Sorin, FabienFunctionalized Fiber Reinforced Composites via Thermally Drawn Multifunctional Fiber Sensors. In Advanced Materials Technologies, 6(3), 2000957–2000957. https://doi.org/10.1002/admt.202000957
-
Staal, Jeroen; Caglar, Baris; Hank, Travis; Wardle, Brian L.; Gorbatikh, Larissa; Lomov, Stepan V.; Michaud, VéroniqueIn-series sample methodology for permeability characterization demonstrated on carbon nanotube-grafted alumina textiles. In Composites Part A: Applied Science and Manufacturing, 150, 106631–106631. https://doi.org/10.1016/j.compositesa.2021.106631
-
Teixidó, Helena; Caglar, Baris; Revol, Vincent; Michaud, VéroniqueIn-operando dynamic visualization of flow through porous preforms based on X-ray phase contrast imaging. In Composites Part A: Applied Science and Manufacturing, 149, 106560–106560. https://doi.org/10.1016/j.compositesa.2021.106560
-
Daelemans, Lode; Tomme, Brecht; Caglar, Baris; Michaud, Véronique; Van Stappen, Jeroen; Cnudde, Veerle; Boone, Matthieu; Van Paepegem, WimKinematic and mechanical response of dry woven fabrics in through-thickness compression: Virtual fiber modeling with mesh overlay technique and experimental validation. In Composites Science and Technology, 207, 108706–108706. https://doi.org/10.1016/j.compscitech.2021.108706
- Caglar B, Tekin C, Karasu F, Michaud V. Assessment of capillary phenomena in liquid composite molding, Composites Part A: Applied Science and Manufacturing, 120, 73-83, 2019. https://doi.org/10.1016/j.compositesa.2019.02.018
For other outputs (conferences, data, communications), visit the project webpage
Arif Poothanari, Yves Leterrier, Véronique Michaud
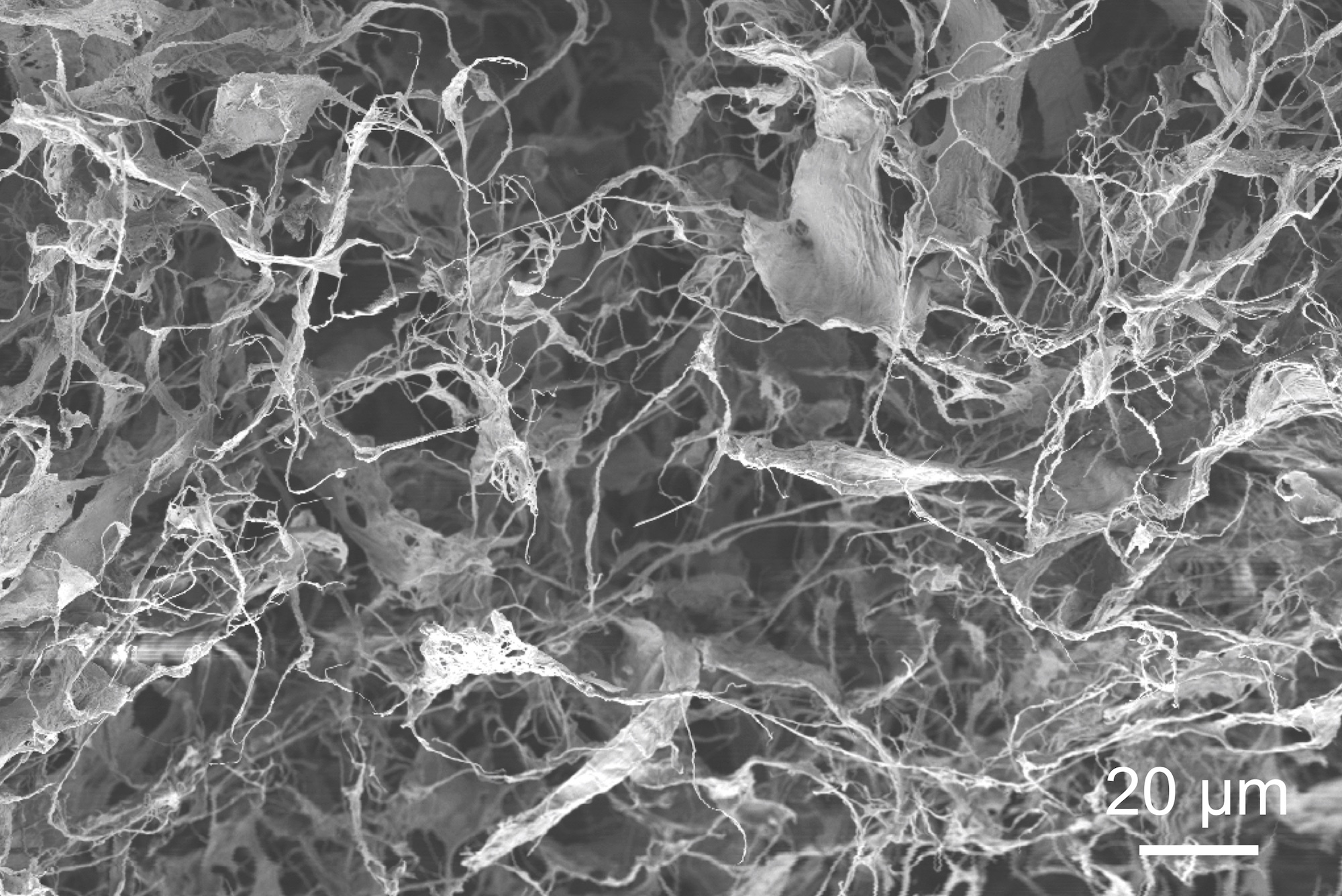
Hybrid piezoelectric nanocomposites based on surface modified graphene/microfibrillated cellulose (MFC) and poly(vinylidene fluoride) (PVDF) are developed for energy harvesting applications. The role of the fillers is first to promote the crystallization of PVDF into its polar beta-phase, and second to achieve exceptional thermomechanical stability. Fluorinated and amine-induced H-bonded interfaces are produced for both graphene and MFC and their influence on the crystalline state, mechanical and electrical properties of composites is systematically explored within a broad compositional space. Pristine and fluorinated fillers hinder beta-phase, in contrast to aminated fillers, which lead to the best property combination.
Funding
- Swiss Government Excellence Scholarships
Partners
- Prof. Damjanovic, EPFL
Kyungjin Kim, Julien Carron, Yves Leterrier
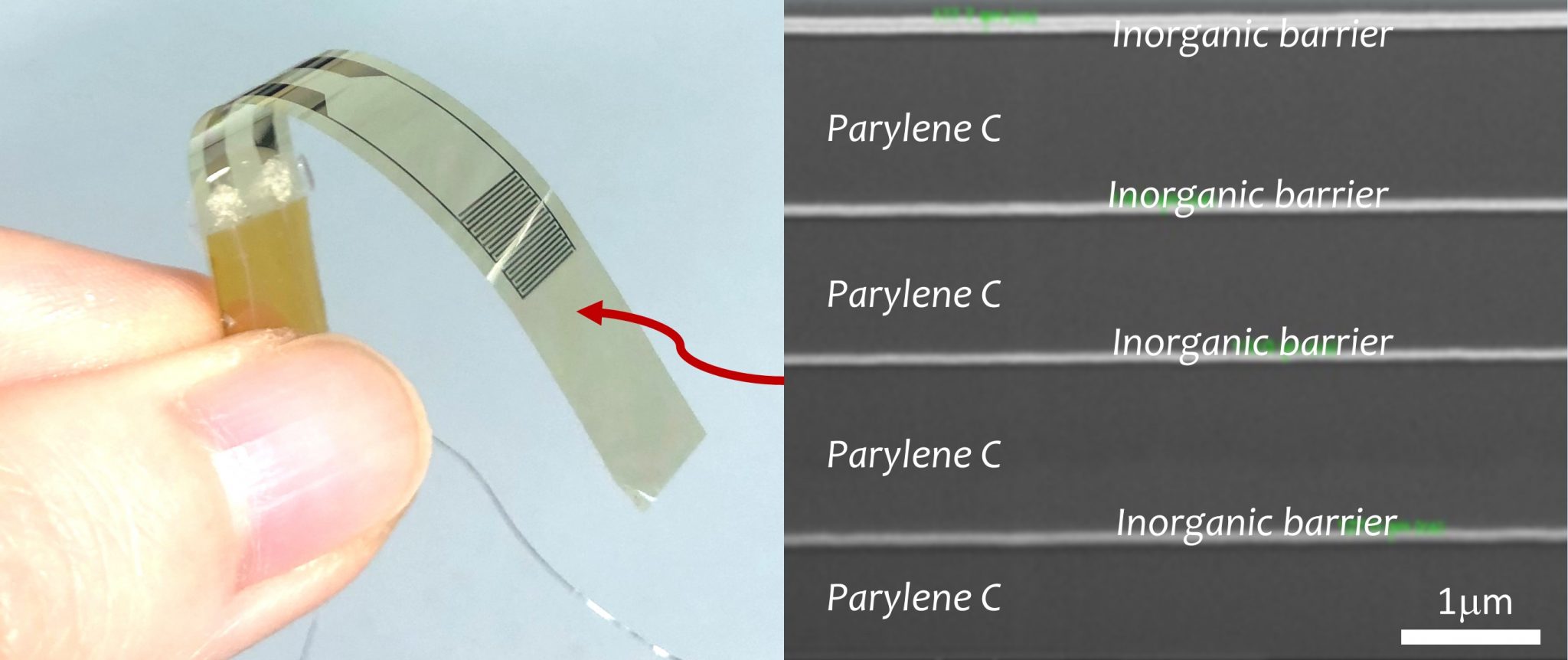
XInoCaps is a Comelec SA-LSBI-LPAC collaboration to develop organic/inorganic barrier coatings for implantable medical devices. The multilayer coatings combine Parylene C and inorganic ALD/PECVD films. These coatings are produced in a new kind of hybrid equipment developed by Comelec, allowing alternative depositions in a single deposition chamber. Specifically, LPAC designs and characterizes the multilayer structure to improve both flexibility and barrier performance in terms of crack onset strain, oxygen/water vapor permeability, and lifetime of barrier coated electrodes. Our ultimate goal is to standardize such design and procedure to coat any fabricated flexible devices at low temperature and demonstrate a new generation of soft biomedical implants with improved lifetime reliability.
Funding
- Innosuisse
Partners
- Comelec SA (http://www.comelec.ch)
- Laboratory for Soft Bioelectronic Interfaces (LSBI-EPFL)