Nanoscale Wear Processes
The wear process remains one of the least understood areas of mechanics. While it is well known that wear and friction are governed by contacts between microscopically rough surfaces, the exact nature of the interactions—even between individual asperities—remained elusive for decades. This has restricted wear prediction to empirical models with limited transferability. One reason that a widely agreed upon understanding of the wear mechanism has not been reached, is that direct modeling of the adhesive wear process presents a substantial challenge.
In our lab, we use molecular dynamics simulations to investigate these phenomena from the “bottom up” at the nanoscale. We developed simple model potentials with tuneable plastic properties, allowing us to control failure length scales more freely than with more realistic materials models. This has allowed us to conduct atomistic simulations that capture the fracture-induced debris formation during the adhesive collision between surface asperities for the first time. Systematic studies reveal a characteristic length scale that controls the adhesive wear mechanisms at the asperity level: This length scale provides a critical adhesive junction size where bigger junctions produce wear debris by fracture, while smaller ones smooth out plastically. Based on this observation, we could formulate a simple analytical model that predicts the transition in the asperity-level adhesive wear mechanisms in both the simulation results and experiments.

Using these first insights and our new modeling tools, we currently work on understanding the more complex interactions that occur in realistic contact scenarios.
For example, the video below shows the shearing of a contact with composite material made of a brittle component and a ductile one. Depending on the ratio of each component, a ductile or brittle behavior can be obtained.
The following pictures show the results of a hard particle rolling between a hard and soft surface. The behavior will differ depending on whether the initial particle diameter is larger or smaller than d* calculated with the mechanical characteristic of the softer surface. If the diameter is larger, “chips” of matter removed from both surfaces will gradually agglomerate on the particle. If it is smaller, the particle will embed in the soft surface and lead to large plastic deformation.

Media Coverage:
EPFL News, Cornell News, Phys.org
A story of two transitions: From adhesive to abrasive wear and from ductile to brittle regime
The Journal of Chemical Physics. 2024. Vol. 160, num. 014711. DOI : 10.1063/5.0176553.Understanding the mechanisms of adhesive wear for heterogeneous materials through atomistic simulations
Extreme Mechanics Letters. 2022. Vol. 57, p. 101913. DOI : 10.1016/j.eml.2022.101913.On the debris-level origins of adhesive wear
Proceedings Of The National Academy Of Sciences Of The United States Of America (PNAS)
2017
Vol. 114 , num. 30, p. 7935 – 7940.DOI : 10.1073/pnas.1700904114
Critical length scale controls adhesive wear mechanisms
Nature Communications
2016
Vol. 7 , p. 11816.DOI : 10.1038/ncomms11816
Surface roughness
Real contacts between two bodies consist of multiple asperity contacts on rough surfaces. As such, any macroscopic description of wear that is not just empirical needs to take the surfaces roughness and actual asperity contact geometry into account. While we also work with continuum models to treat such contact problems, it is very challenging to model the evolution of rough surfaces in wear conditions. Here, atomistic models can provide a way to explore such evolution, since they implicitly include realistic plastic and fracture behavior on the nanoscale.
Dry contact of metals
In our lab, we use molecular dynamics simulations to investigate the effects of two materials in dry contact. For example, we investigate how the contact surface evolves when two bodies are pressed together in normal and sliding contact. Materials, loading conditions, and surface topographies all play a part in the evolution of dry contact. These different parameters are all studied in depth in our group.
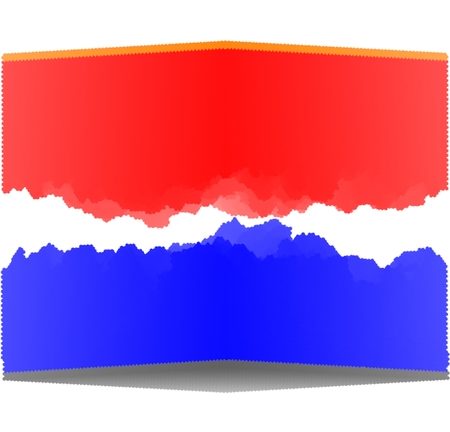
1
In the above figure, an example of an atomistic representation of a rough aluminium surface is depicted. From a macroscopic point of view this surface might be considered flat, but this is clearly not the case at the atomistic level.
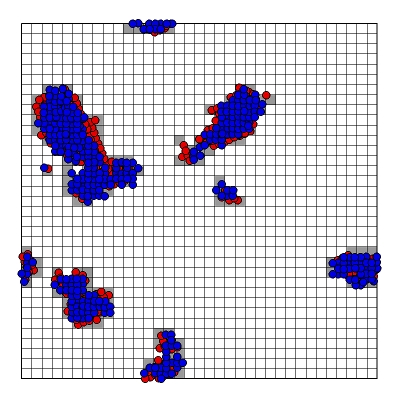
2
This figure shows the real contact area (red and blue atoms) of two rough surfaces in contact. The contact pressure is 0.05 GPa and the RMS roughness is about 1.0 nm.
We have used molecular dynamics simulations in the past to model dry friction of two rough deformable surfaces and found that friction increases with RMS roughness. Nevertheless, RMS roughness is altered during the sliding motion and as evidenced by surface flattening which closely matches the apparent friction with an exponential decay and reduces it to almost zero. This gave us insights into rate and state friction, but also called for the study of other mechanisms which are involved in recreating or preserving roughness at the contacting asperities.
With our new insights at the asperity level, we now know that the critical asperity size for debris formation in metals is too large for atomistic simulations, even using state-of-the art supercomputers. Currently, we are therefore using our newly-developed model potentials—which allow tuning the critical asperity size—in order to gain insights into roughness evolution in the presence of debris formation.
Dry sliding contact between rough surfaces at the atomistic scale
Tribology Letters
2011
Vol. 44 , p. 279 – 285.DOI : 10.1007/s11249-011-9846-y