Dynamic fragmentation is a critical mechanical process where materials or structures disintegrate into fragments under extreme loading conditions, such as explosions or impacts. During these high-energy events, cracks form at material defects and propagate rapidly, causing branching, merging, and fragment formation. This process is further characterized by the propagation and interaction of stress waves with boundaries, material interfaces, newly formed cracks, as well as repeated collisions among moving debris.

Our research focuses on simulating fragmentation processes caused by impacts, high-strain-rate loads, and internal residual stresses. We use massively parallel simulations to capture the initiation, propagation, branching, and interaction of cracks with high fidelity. These simulations offer detailed insights into fragment sizes, masses, and velocities, as well as critical phenomena such as stress wave propagation and debris particle interactions and energy partitioning, which are challenging to monitor experimentally.
While dynamic fragmentation spans many scales—from astronomical events like supernovae to molecular processes—it is of particular concern in the aerospace industry and its safety. It plays a crucial role in the escalating issue of space debris. This topic gathers two different research projects at LSMS.
Hypervelocity impacts of satellites in orbit
Space debris consists of man-made objects in Earth’s orbit, such as spent rocket stages, decommissioned satellites, and fragments from collisions or explosions. Since the dawn of the space age in 1957, these objects have accumulated at an alarming rate. Currently, there are over 128 million pieces of debris smaller than 1 cm, around 900,000 objects between 1 and 10 cm, and approximately 34,000 objects larger than 10 cm (ESA’s annual space environment report). Traveling at speeds exceeding 10 km/s, even the smallest pieces of debris can cause catastrophic damage to spacecraft, which must often perform evasive maneuvers to avoid collisions. This problem is exacerbated by the increasing number of satellite launches, driven by commercial demand for large constellations of satellites. The Kessler Syndrome, first introduced by NASA scientist Donald J. Kessler in 1978, describes a dangerous feedback loop where each collision generates more debris, increasing the likelihood of further collisions.
These observations motivate the growing need for a numerical tool that is not only efficient but also scalable and reliable. The Cohesive LIPschitz Project (CLIP)—an initiative funded by the Swiss National Fund (SNF) and the Agence Nationale de Recherche (ANR)— brings together the expertise of GEM at Centrale Nantes and LSMS at EPFL to develop a tool designed to meet these challenges.

Existing methods for crack modeling rely either on diffuse damage approaches (e.g., Phase-Field, non-local integral models) or sharp crack techniques (e.g., Cohesive Zone Model (CZM), XFEM). CLIP takes a pioneering approach by combining the strengths of both methods—integrating CZM with Lip-Field modeling. This fusion seeks to mitigate the limitations of individual methods, such as CZM’s mesh dependency, while capitalizing on their benefits, particularly computational efficiency. This leads to the introduction of two dependent damages variables, cohesive’s and bulk’s.

For additional information, please contact Thibault Ghesquière.
Creation of debris during satellite’s atmosphere re-entry
With the increasing reliance on orbiting satellites, the risks posed by their potential impact on Earth’s surface during re-entry has become a significant concern. Re-entering vehicles face extreme loads, leading to many propagating cracks, which then coalesce to form fragments in a process called dynamic fragmentation.
Robust numerical models are direly needed to develop a fundamental understanding of such highly energetic breakup events. This research aims to promote the creation of an efficient, high-fidelity, physics-based FE software that can reliably predict the generation of debris. The focus will be on obtaining accurate statistical distributions of fragment sizes, shapes, and velocities to better inform the mitigation of risks during satellite re-entry.
The LSMS group has expertise in dynamic fragmentation and has developed high-performance algorithms for the insertion of cohesive cracks. Yet, this approach suffers from a mesh dependency of the crack paths and non-robust predictions of fragment shapes. Phase-field modelling of fracture belongs to another family of methods using diffuse crack approaches, resulting in mesh-independent crack paths. This method has been shown to lead to promising results, and its use in the context of dynamic fragmentation has yet to be explored. It could lead to drastic improvements in the predictive ability of numerical models.
This project is co-sponsored by the European Space Agency (ESA) through their Open Space Innovation Platform (OSIP) initiative.
It is carried out in close collaboration with experts from ESA and partnering entities, who provide valuable insights into the requirements of the space industry. This joint effort aims to contribute to tackling the aforementioned challenges and to deepen the understanding of the significance of dynamic fracture propagation and fragmentation during destructive re-entry.

For additional information, please contact Shad Durussel.
Modeling of dynamic failure and fragmentation in brittle and quasi-brittle materials is still a challenge since it highly depends on the material micro-structure. Indeed, to be able to model flaws at the micro-structure scale, a fine description of the material is needed, and thus powerful and effective numerical methods. The finite elements method with dynamic insertion of cohesive elements is used, in order to take advantage of a higher computational efficiency than that of particle methods. Interaction among fragments is then handled by means of contact detection and contact laws algorithms.
Depending on the loading rate and on material parameters, convergence may constitute a numerical challenge. Simulations on very fine meshes require high amount of memory and efficiency, that only a parallel implementation of the algorithms together with high performance computing can supply.
All the code developed for this project is contained in our C++ library Akantu.
Dynamic failure
Failure of a civil engineering concrete structure under dynamic loading is a phenomenon which highly depends on the heterogeneous material composition. Concrete is a brittle like material which fractures via the nucleation, propagation and coalescence of local microcracks. Furthermore the rough surfaces of the generated macrocracks might enter in contact being responsible for the shear forces which can be transferred between the two cracks determining a part of the strength of the macrostructure.
The material microstructure of concrete plays then an important role in the failure processes. The wide kaleidoscope of sizes of the ingredients presents in the mixture defines the mechanical behavior. Concrete can be then modeled using a meso-mechanical approach in which aggregates and mortar are represented explicitly. Both continuum phases are considered to behave elastically, while nucleation, coalescence and propagation of cracks are modeled using the cohesive-element approach. Using a rigorous and scalable three-dimensional approach, the evolution of microcracks is simulated in a realistic manner.
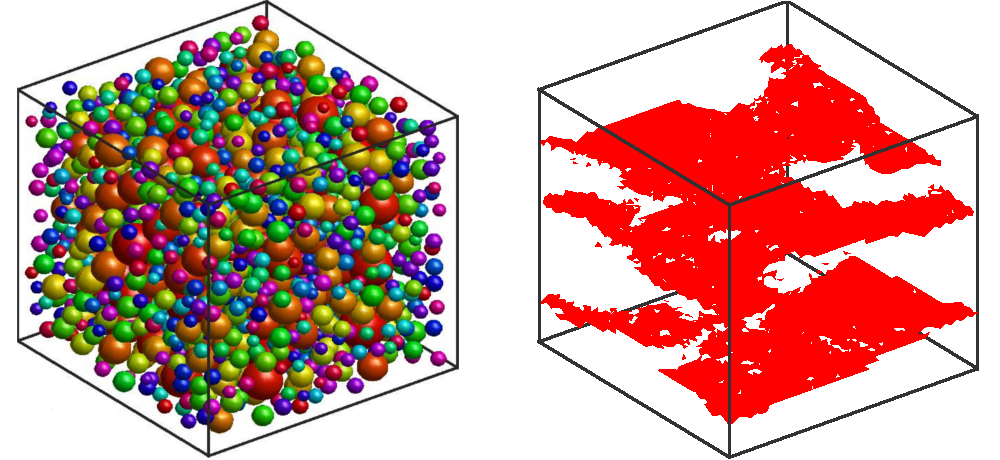
A cubic concrete model at the mesoscale and crack formation under tensile loading with a strain rate 10 /s.
Fragmentation
Fragmentation is a topic of major industrial (blast protection, mining, tunneling) as well as astrophysics (asteroid impacts) interest. Our focus is on fragmentation due to impacts, high-strain rate loads, and internal residual stresses. We conduct massively parallel simulations aiming at representing accurately cracks initiation, propagation, branching and interaction, as well as providing a detailed description of fragment sizes and velocities. Such simulations give us access to rapidly evolving fields and values (such as kinetic, potential, and dissipated energies) that cannot be accurately monitored during experimental tests, thus facilitating the understanding of the fragmentation process. Also, fragment statistics (their sizes, masses, velocities) can be derived. From these outputs, we can investigate the fragment mass and velocity global distributions and understand their correlations.
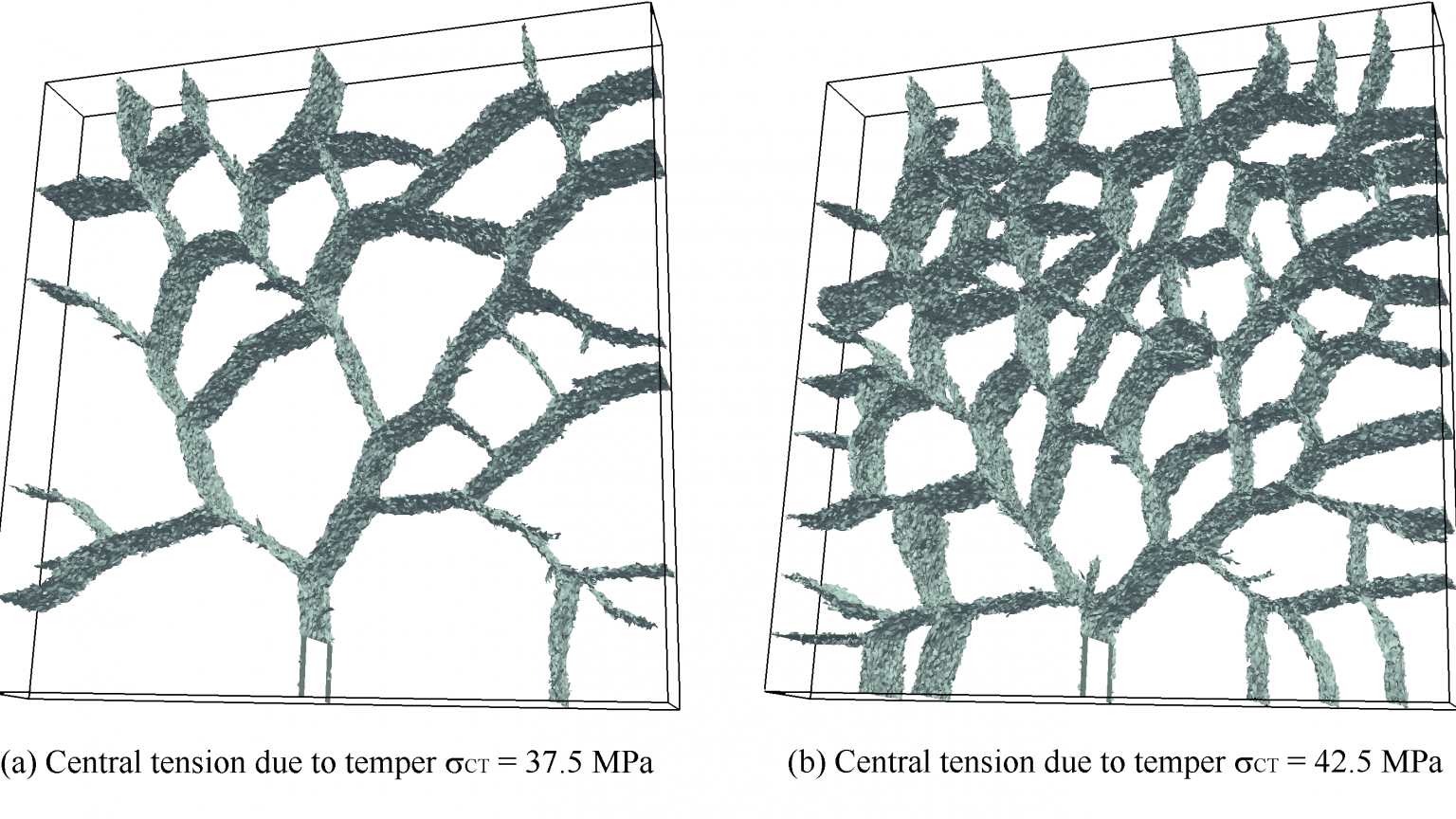
Fragments identified by fully damaged cohesive elements in two tempered glass plates 8 mm thick with different residual stress values.
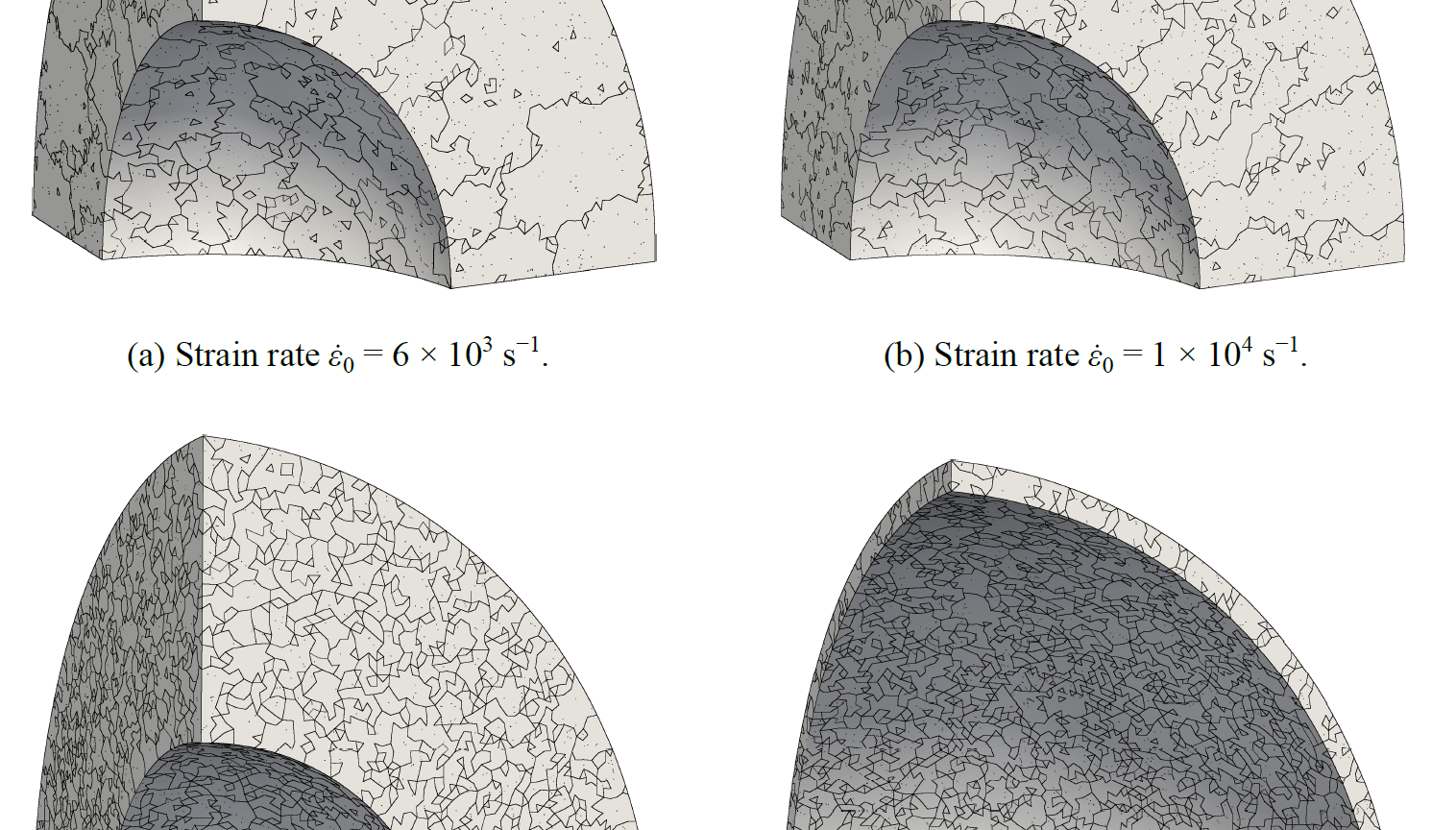
Dome subjected to radial expansion: borders of the fragments for different strain rates.