Our lab is always seeking motivated students eager to deepen their knowledge in the mechanics of materials and structures, as well as scientific computing (including the finite-element method, particle methods, and data-driven machine learning). We offer projects in collaboration with industry, government, and academic partners across a wide range of applications (such as space debris, sports mechanics, modeling concrete and dam aging, and earthquake science). Many of our students have the opportunity to conduct their Master projects abroad, at institutions like MIT and Caltech. Each project is unique, tailored to the student’s interests, and closely aligned with the lab’s ongoing research.
A complete list of available projects is posted just before each semester. Feel free to reach out—we look forward to welcoming you to the team!
All available projects have been booked for this spring semester 2025.
Student projects
For master’s theses and more semester projects, you can contact gaetan.cortes@epfl.ch and jean-francois.molinari@epfl.ch (Please put both in your mail !). Don’t hesitate to check out previous projects on infoscience.
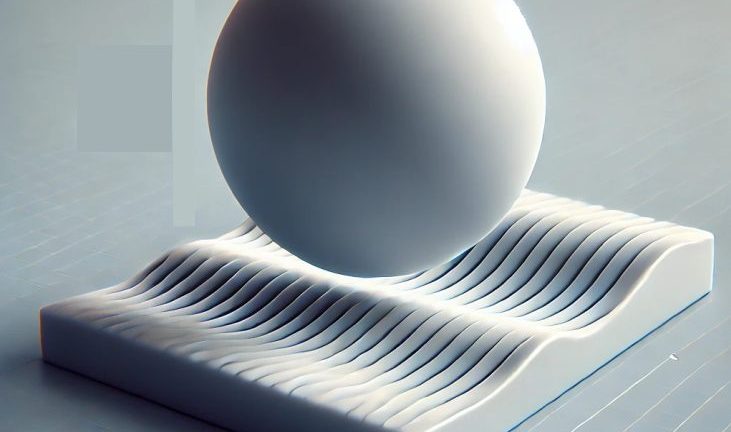
Soft lubrication of solid impacts [NOT AVAILABLE]
Bachelor/Master
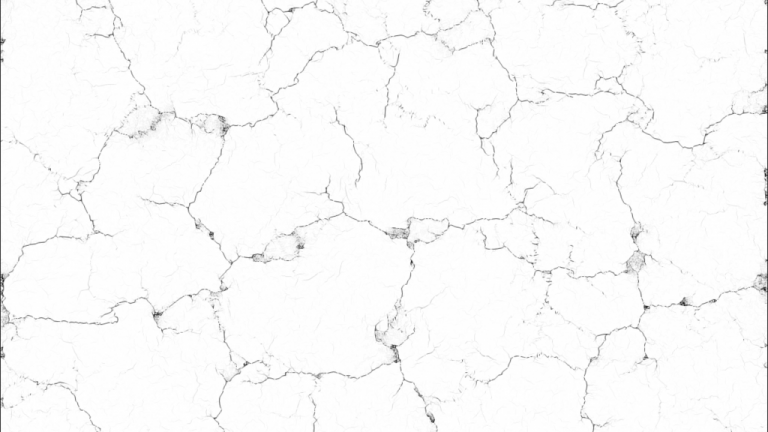
Numerical simulation of dynamic fragmentation
Bachelor/Master
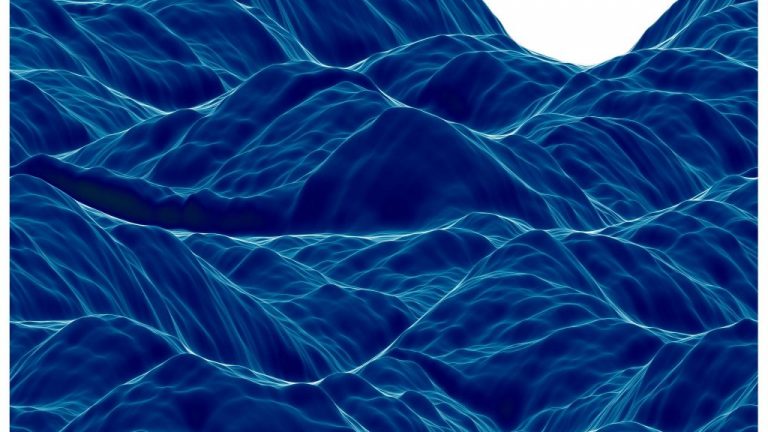
Emergence of complexity in a frictional system: reproducing earthquake statistics [NOT AVAILABLE]
Master thesis / Semester project
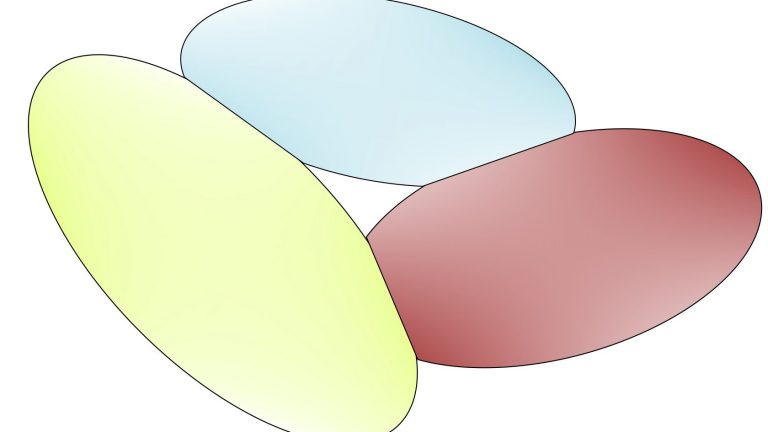
The Soft Discrete Element Method [NOT AVAILABLE]
Bachelor/Master
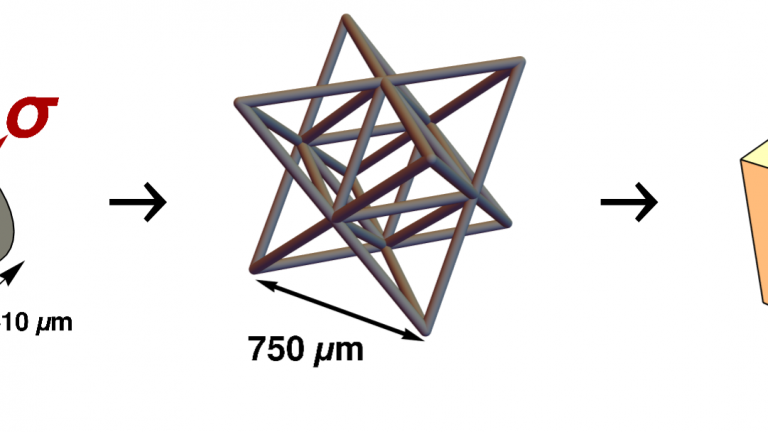
Neural networks meet finite elements [NOT AVAILABLE]
Bachelor/Master
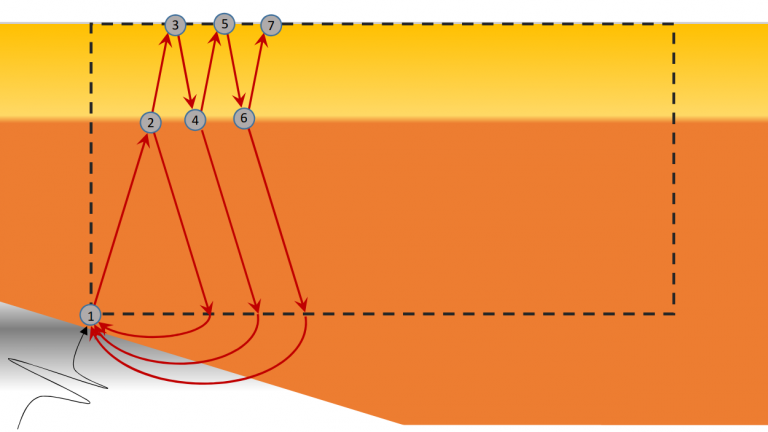
Wave propagation in layered media [NOT AVAILABLE]
Bachelor/Master
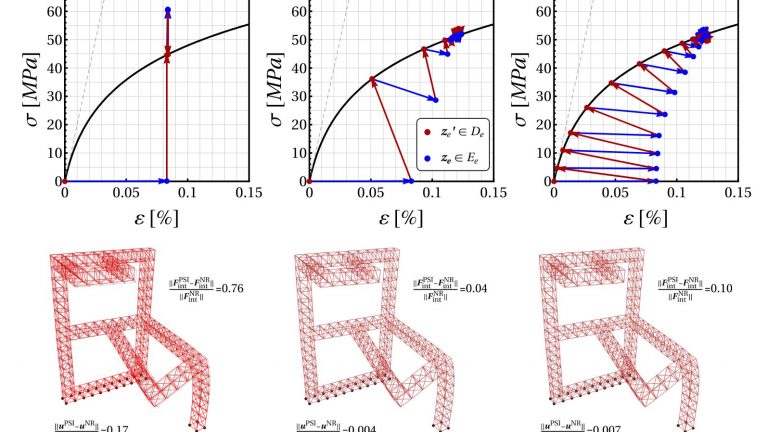
Phase-space iterative solvers [NOT AVAILABLE]
Bachelor/Master
Former student projects
Below is a non-exhaustive list of previous projects done by students of LSMS.
2025
PINNs applied to dynamic friction
2025
Advisor(s): A. J. Garcia Suarez; G. Cortes
DEM Implementation for Elliptical and Soft Particles Civil 481 -Semester Project Report
2025
Advisor(s): J-F. Molinari; J. Bilotto
Numerical Simulation of Dynamic Fragmentation
2025
Advisor(s): S. A. Durussel; T. Ghesquière-Diérickx; J-F. Molinari
2024
Convergence properties of phase-space iterative solvers
2024
Advisor(s): A. J. Garcia Suarez; J-F. Molinari
2023
Testing Benchmark for a Block Conjugate Gradient Solving Scheme in Poroelasticity
2023
Advisor(s): E. Gallyamov; J-F. Molinari
Study of shoe performance using a lattice spring model : Comparison of multiple outsoles
2023
Advisor(s): R. M. S. Ferry; J. Bilotto; J-F. Molinari
Simulation of dynamic fragmentation of solids
2023
Advisor(s): S. A. Durussel; J-F. Molinari
Introduction to dynamic fragmentation with FEM – plate breaking
2023
Advisor(s): J-F. Molinari; R. Dantas Batista
Discrete Element Method (DEM) study of the interaction between a solid body and granular medium
2023
Advisor(s): S. A. Durussel; M. E. Voisin–Leprince; J-F. Molinari
Data-driven Computational Mechanics: Implementation and Application
2023
Advisor(s): S. Z. Wattel
2022
Classification of Granular Material – Applied Machine Learning to granular materials
2022
Advisor(s): M. E. Voisin–Leprince; G. Anciaux
Development of a DEM simulation of the interaction between a shoe and soil
2022
Advisor(s): M. E. Voisin–Leprince; A. J. Garcia Suarez; J-F. Molinari
Extension of granular materials using machine learning
2022
Advisor(s): M. E. Voisin–Leprince; G. Anciaux
Outsole-and-soil contact simulation with the FEM
2022
Advisor(s): J. Garcia Suarez
Heat transfer in layered media
2022
Advisor(s): J. Garcia Suarez
DEM study of interaction between a salid body and a granular medium
2022
Advisor(s): J. Garcia Suarez
Ultiscale modeling of 1D site response analysis with data-driven computational mechanics and discrete-element method
2022
Advisor(s): J. Garcia Suarez; S. Z. Wattel
Implementation of the INTERNODES method for contact
2022
Advisor(s): G. Anciaux
2021
Dynamic crack propagation with phase-field approach
2021
Advisor(s): J-F. Molinari; G. Anciaux
Pressure effect on a crack
2021
Advisor(s): J-F. Molinari; E. Gallyamov; Y. Sun
Former master thesis
Below is a non-exhaustive list of previous master thesis done by students of LSMS.
2024
Pumped-Storage Plant in an Arctic Context. Design and Construction of Underground Structures.
2024
Advisor(s): B. Lecampion; E. Gallyamov
Block shape design to improve the seismic stability of multi-block structures – Seismic study of multi-block structure for energy storage
2024
Advisor(s): J-F. Molinari
2022
Detachment Dynamics of Heterogeneous Adhesive Pads
2022
Advisor(s): T. D. Roch; J-F. Molinari; T. Cohen
2021
On the preconditioning of the INTERNODES matrix for applications in contact mechanics
2021
Advisor(s): G. Anciaux; S. Deparis
Contact Mechanics for Hyperelastic Materials
2021
Advisor(s): J. M. Kolinski; J-F. Molinari
BEM Study of the Contact between Rough Surfaces for Dry and Lubricated Condition
2021
Advisor(s): J-F. Molinari; G. Costagliola
On the preconditioning of the INTERNODES matrix for applications in contact mechanics
2021
Advisor(s): G. Anciaux
2020
Tissue deformation algorithm to estimate breast tumor location from prone-to-supine position
2020
Advisor(s): J-F. Molinari
Fast modeling of frontal polymerization
2020
Advisor(s): J-F. Molinari
BEUCHAT_Bachelor_Powerpoint
2020
Advisor(s): J-F. Molinari
Two-dimensional granular shear model
2020
Advisor(s): J-F. Molinari; M. E. Voisin–Leprince
Dynamic fragmentation of a fragile ring
2020
Advisor(s): J-F. Molinari
Inverse Modelling and Predictive Inference in Continuum Mechanics: a Data-Driven Approach
2020
Advisor(s): J-F. Molinari
Development of discrete surface growth models for frictional surfaces
2020
Advisor(s): G. Anciaux; E. Milanese
Variational phase-field study of adhesive wear: elastic and elastic-plastic models
2020
Advisor(s): J-F. Molinari
Stick-Slip in Peeling of Soft Adhesives: a Finite Element Model Using Reversible Cohesive Elements
2020
Advisor(s): T. Massart; C. Tal; T. D. Roch; J-F. Molinari
2018
Propagation of peeling in finite adhesive pads
2018
Advisor(s): J-F. Molinari; T. Cohen; E. Gallyamov
Modélisation et optimisation des structures en coque par éléments finis
2018
Advisor(s): J-F. Molinari
Design of a Fiberglass Skateboard
2018
Advisor(s): J-F. Molinari; A. Vassilopoulos
Modélisation et optimisation des structures en coque par éléments finis
2018
Advisor(s): L. Frérot; J. Bleyer; J-F. Molinari
2017
Modeling weak layer failure using non-associated plasticity
2017
Advisor(s): G. Anciaux; J. Gaume
Study of the plastic interaction of asperities sitting on a rough surface
2017
Advisor(s): G. Anciaux; R. Aghababaei
2015
Developing a 3D finite element model for reinforced concrete
2015
Advisor(s): M. Vocialta; M. Corrado; T. Menouillard; J-F. Molinari