Origami robots characterized by rigid plates linked together with flexible joints have inherent compliance and large deformations. Their low-profile design and folding mechanical transmissions provide substantial force and torque, especially for wearables and humaninteractive devices. The current major limitation in the field is the need for embeddable dynamic actuation systems that produce actuation frequencies similar to human motion. In this study, we propose a novel low-profile printable electromagnetic actuator that can be integrated into thin large robotic surfaces made of rigid panels and into the streamlined pushbutton manufacturing process. We use already existing variable stiffness joints to demonstrate the scalability and distributable properties of the proposed actuation system on a locally controllable variable-stiffness distributed surface.

Figure 1: Distributed Stiffness Surface with printable electromagnetic actuation system distributed in the black tiles of the prototype. While the square magnets of the electromagnet are visible, the printed coils are embedded inside the low-profile structure. The variable stiffness is achieved through the sliding of a mechanical compliant slider inside the flexible joints made of Kapton film whose position is controlled via embedded actuator in the tiles. Our work brings a new dimension of a reconfigurable surface without having to be grounded to a base (as it is done in [37]). This distributed modulation can selectively tune the stiffness of a large scale high-DoF system.
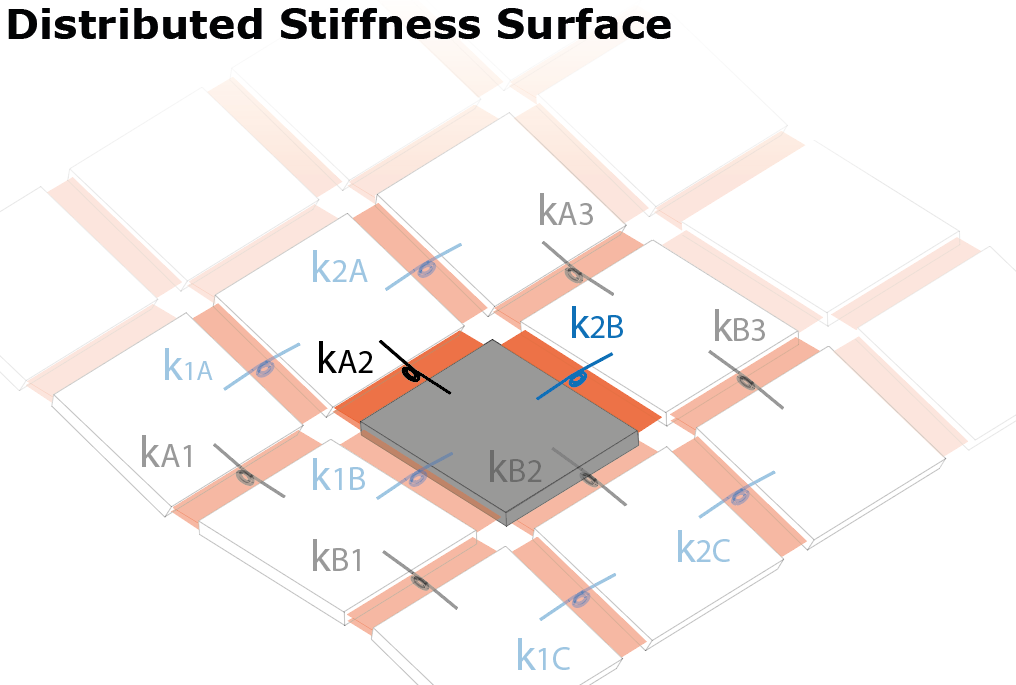
Figure 2: Distributed Stiffness Surface. Illustration of a high-Dof surface made of modular tiles that can have the stiffness of each link independently modulated on a continuous range to adapt the distributed stiffness of the whole surface. The black springs are for the joints in one direction and the blue ones in the other perpendicular direction. The electomagnetic embedded actuators allow to independently address each of those variable stiffness joints to modulate the stiffness of the whole surface.
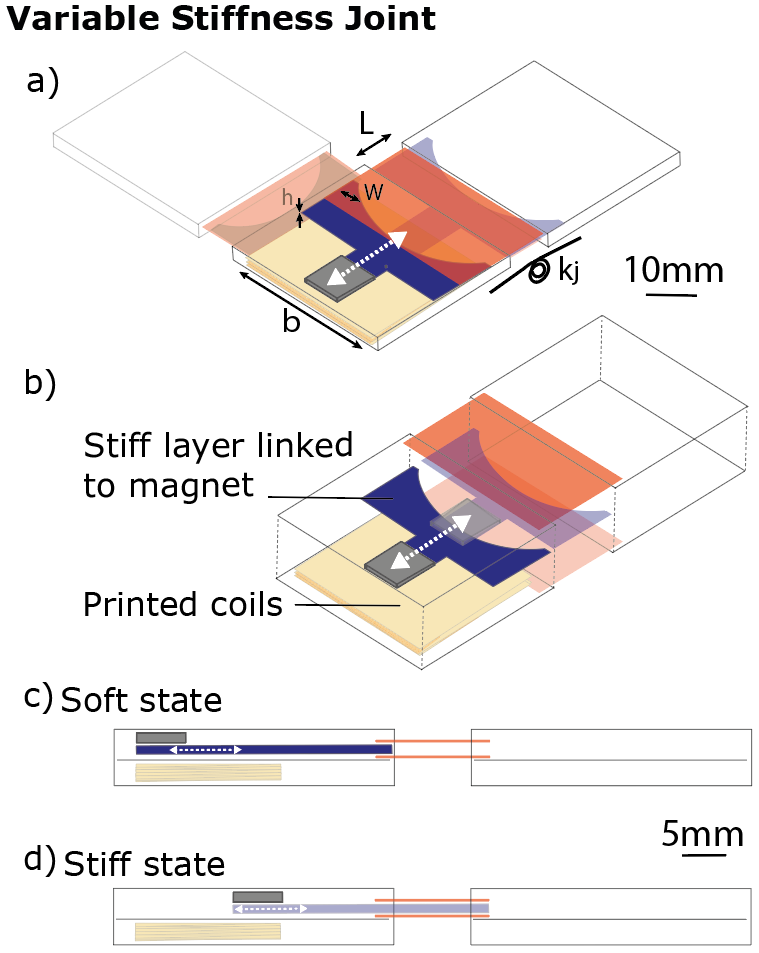
Figure 3: Variable Stiffness Joint Mechanism a) Illustration of a high-Dof Surface modular tile with two variable stiffness joints developped in a previous work [35] stacked together in a 4mm-thick structure that allows to modulate the stiffness in two perpendicular directions.. b) The parametric electromagnetic actuator (yellow) moves a magnet (grey) linked to a variable stiffness sliding layer (blue) inbetween two flexible Kapton layers (orange). c)d) The stiffness sliding layer varies the amount of stiff material in the joint to modify its rotational stiffness ?? . When the slider is completely retracted (c) inside the rigid tile, the compliant joint is soft and when it is slided into the compliant joint, it becomes stiffer (d). The EM actuators coupled with the U-shape of the sliding layer allows to modulate the rotational stiffnes of the joint.
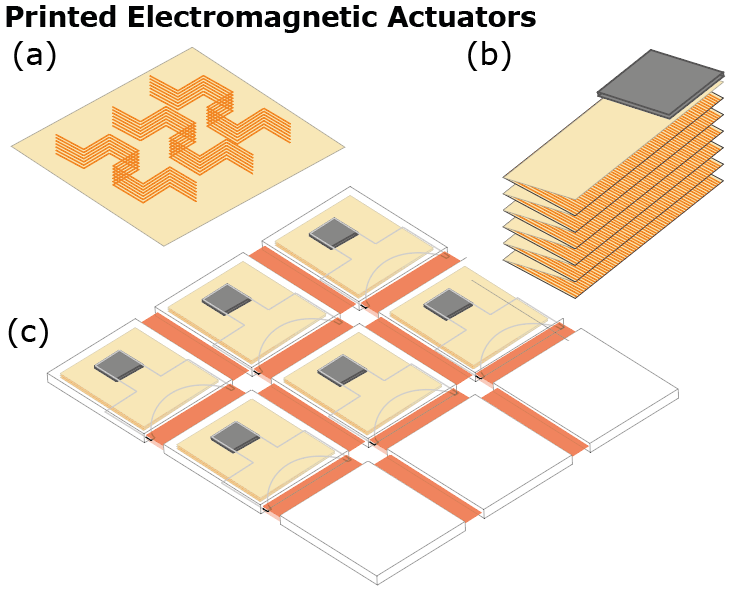
Figure 4: Printed Electromagnetic Actuators Integration Process. Illustration of the manufacturing process starting with (a) the printing of a Kapton-copper sheet through conventional copper etching into coil. (b) It is then only needed to fold the sheet to create a pattern of coils in order to have a low-profile linear actuator by putting a flat magnet on top. (c) The actuator so made can then be embedded into any kind of robotic surface thin structure such as this variable stiffness distribued surface with 6 actuators, each embedded into one rigid tile of the high-DoF structure.
Contact: Fabio Zuliani
Publications:
- Zuliani, F., & Paik, J. (2022, October) Electromagnetic Actuation Design for Distributed Stiffness. In Smart Materials and Structures
-
Zuliani, F., & Paik, J. (2021, January). Variable Stiffness Folding Joints for Haptic Feedback. In 2021 IEEE/RSJ International Conference on Intelligent Robots and Systems (IROS) (pp. 8332-8338). IEEE.