3D Printable κ‐carrageenan‐Based Granular Hydrogels
Κ-carrageenan, an algae-derived polysaccharide widely used in food and beauty products, shows promise as a biocompatible alternative to animal gelatin in tissue engineering due to its abundance and similarity to glycosaminoglycans.
However, its temperature-sensitive rheological properties limit its processability. To overcome this limitation, we developed a novel κ-carrageenan-based ink that can be processed through direct ink writing (DIW) at room temperature. This ink comprises jammed κ-carrageenan-based microgels that are loaded with precursors for a 2nd hydrogel network. Upon completion of the 3D printing process, the reagents contained within the microgels are transformed into a percolating network, resulting in double-network granular hydrogels (DNGHs). These DNGHs can be reinforced with metal ions and glucose, achieving stiffness up to 1.1 MPa and a 50-fold increase in fracture toughness. This breakthrough enables the creation of cm-scale load-bearing κ-carrageenan-based structures that can be used, for example, as a sustainable, algae-derived alternatives for biomedical and food applications, including tissue engineering and soft confectionery. The work is published in Advanced Functional Materials.
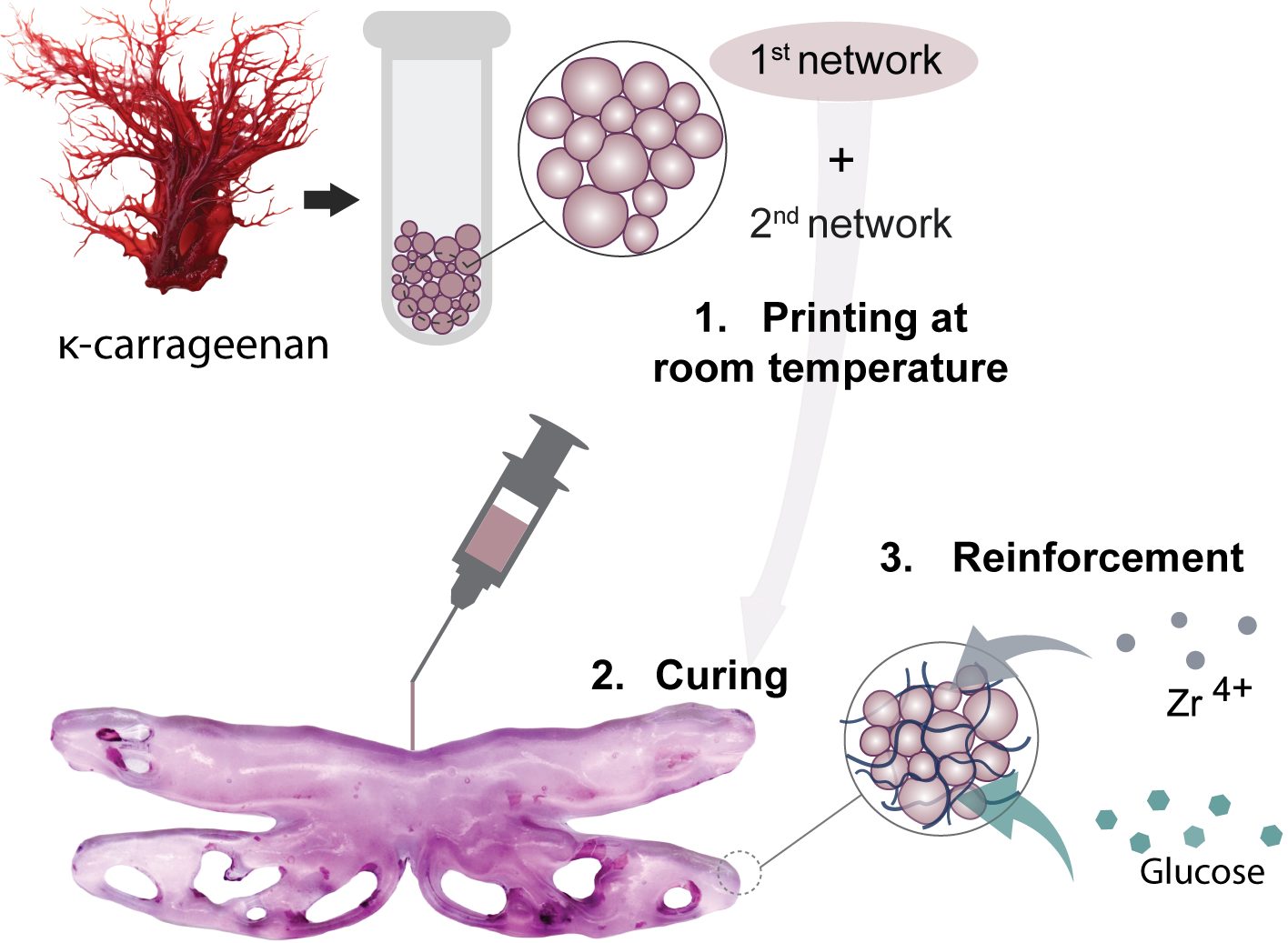
Direct Ink Writing of Rigid Microparticles
Direct ink writing (DIW) enables the 3D printing of intricate macroscopic structures. However, inks can only be successfully direct ink written, if they fulfil stringent rheological requirements which are not fulfilled by densely packed stiff microparticles. To overcome this limitation, we introduce core-shell microparticles composed of stiff epoxy-based microparticle cores that are surrounded by thin, soft hydrogel-based shells. We demonstrate that jammed particles whose shells exceed a thickness of few micrometers fulfill the rheological requirements DIW imparts on its inks. We process these core-shell particles into cm-sized structures and firmly connect them by forming a 2nd hydrogel network that interpenetrates the hydrogel shells and covalently linking the microparticles. We demonstrate that the addition of SiO2 nanoparticles with diameters between 130 and 180 nm to the epoxy-based particle cores endows them structural colors that can be locally varied by co-printing different types of inks. The article is published in Small.
Recyclable 3D Printable Single Network Granular Hydrogels
This study introduces recyclable single network granular hydrogels composed of poly(acrylic acid) (PAA) microgels that are electrostatically connected with poly(diallyldimethylammonium chloride) (PD) and optionally reinforced with Cu2+. The combination of electrostatic and ionic interactions enables 3D printing high aspect ratio structures in air and aqueous media. Due to the electrostatic interactions, the structures are self-healing and can be decomposed into individual microgels that can be recycled into new granular materials under benign conditions and without significantly altering their mechanical properties. Indeed, in the absence of ions, this material is self-sustaining and does not significantly sag if printed on top of pillars with distances up to 1.6 cm. Due to the electrostatic interactions, this material efficiently dissipates energy such that it can be used as soft underwater dampers. This work is published in Biomaterials Science.
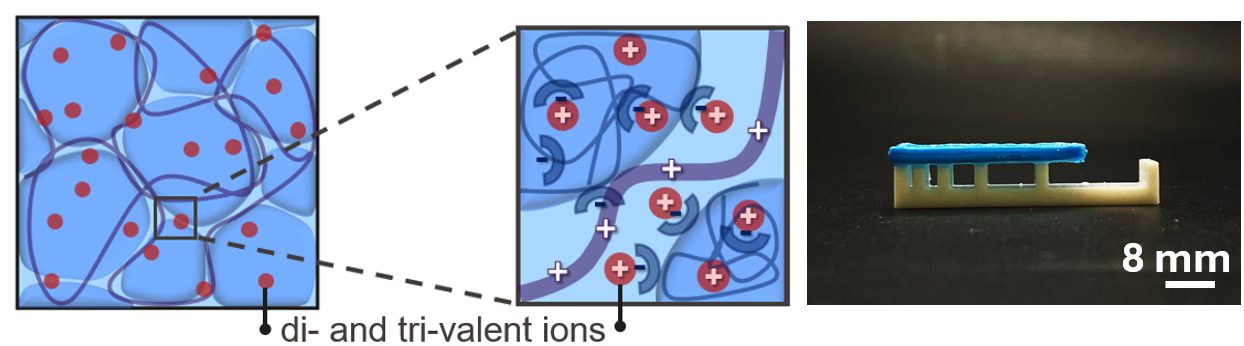
Localized Ionic Reinforcement of Double Network Granular Hydrogels
Nature produces soft materials with well-defined structures and compositions controlled on lengths scales ranging from cm down to tens of nanometers which is yet unmatched in synthetic hydrogels. Here, we introduce 3D printable load-bearing granular hydrogels whose composition changes on the tens of nanometer length scale. The granular hydrogels are composed of jammed microgels encompassing tens of nm-sized polyelectrolyte-based domains. We demonstrate that upon ionic reinforcement of these 10s of nm sized domains, the stiffness of double network granular hydrogels increases up to 18-fold. Leveraging the rheological properties inherent to jammed microgels, this formulation is direct ink written into cm-sized structures, such as a butterfly, that are locally reinforced. This work is published in Small.
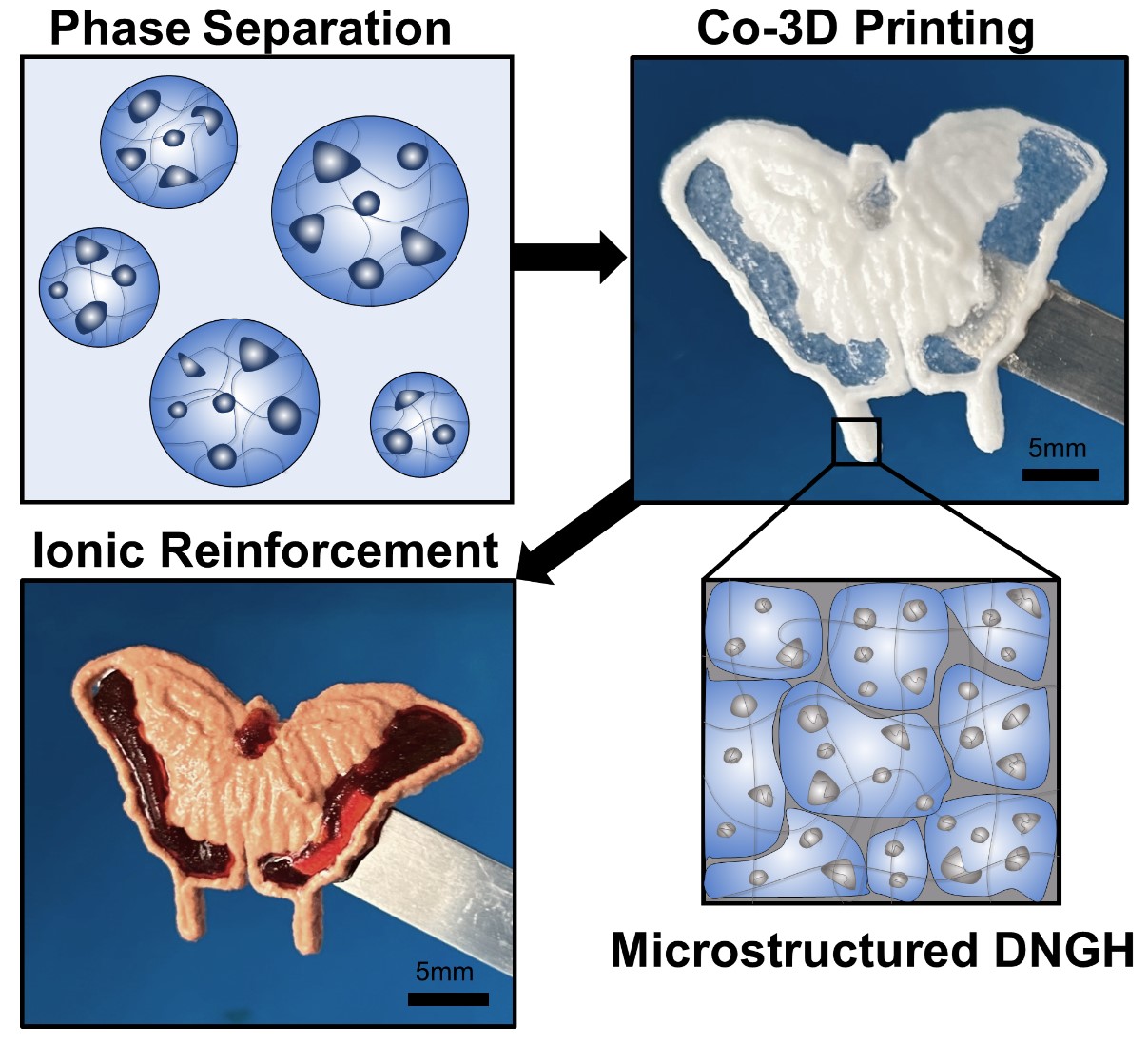
Osmosis-driven stiffening of structured hydrogels
Plant cells harness osmotic pressures to stiffen their leaves through strong turgor pressures. Inspired by the turgor effect in plants, we fabricate hydrogels possessing inclusions that are filled with polyelectrolytes possessing a high degree of swelling. The swelling of these polyelectrolytes is spatially confined by the stiffer inert hydrogel surrounding. The resulting osmotic pressure increases the stiffness of these structured hydrogels up to three-fold compared to that of the matrix with water-filled inclusions. We leverage osmotic pressure gradients to change the morphology of cm-sized hydrogel leaves by immersing their bottom parts in water, without the need for additional stimuli that consume energy or require a change in the environmental conditions. We foresee these materials to open up new possibilities to actuate soft materials in a benign, energy-efficient manner. The article is published in Applied Materials Today.
4D Printing of Metal-Reinforced Double Network Granular Hydrogels
Recent developments in soft actuation demand for resilient, responsive materials with locally varying compositions that are sufficiently stiff to exhibit significant actuation forces. Hydrogels are inherently responsive to certain stimuli. Yet, they typically suffer from a stiffness-toughness compromise such that those that are soft and show adequate flexibility display limited actuation forces. Here, we introduce 3D printable metal-reinforced DNGHs (mrDNGHs) that combine three seemingly contradictory traits: stiffness, toughness, and processability. Our mrDNGHs can bear loads up to 3 MPa while displaying a fracture energy up to 12 MJ·m−3, a value exceeding that of any of the previously 3D printed hydrogels at least 20-fold. We leverage the different degrees of swelling of the mrDNGHs to 3D print shape morphing structures. This work is published in Chemical Engineering Journal.
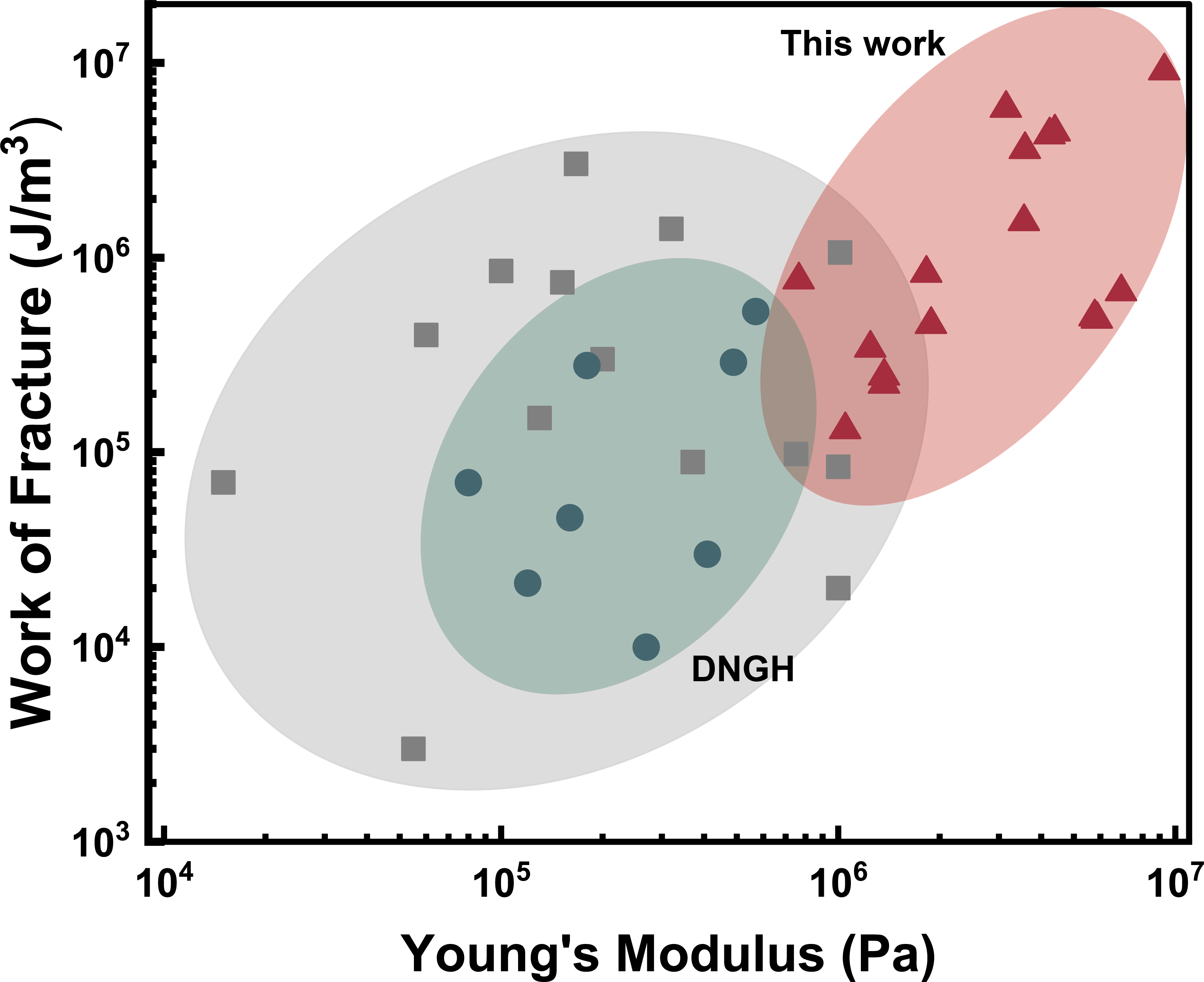
Porous 3D Printable Hydrogels
We recently introduced double network granular hydrogels that displayed the highest stiffness that has been reported for 3D printed hydrogels. This was achieved by connecting adjacent microgels through a 2nd percolating network. While this network imparts stiffness to the granular system, it also fills the interstitial spaces, thereby limiting the diffusivity of reagents within these hydrogels. In this work, we introduce porous 3D printable double network hydrogels. This is achieved by loading microgels with a mixture of two-phase separating reagents, namely acrylamide and poly(ethylene glycol) (PEG). After the granular ink has been 3D printed, it is solidified through its exposure to UV light. Through the polymerization of the acrylamide, we obtain a phase separation between the two polymers. We subsequently remove the PEG, which we use as a sacrificial porogen to obtain double network granular hydrogels possessing pores with diameters exceeding 20 nm. We demonstrate the use of this material as a size-selective filter to absorb reagents only at well-defined locations. This work is now published in Advanced Materials Technologies and featured on the back cover.
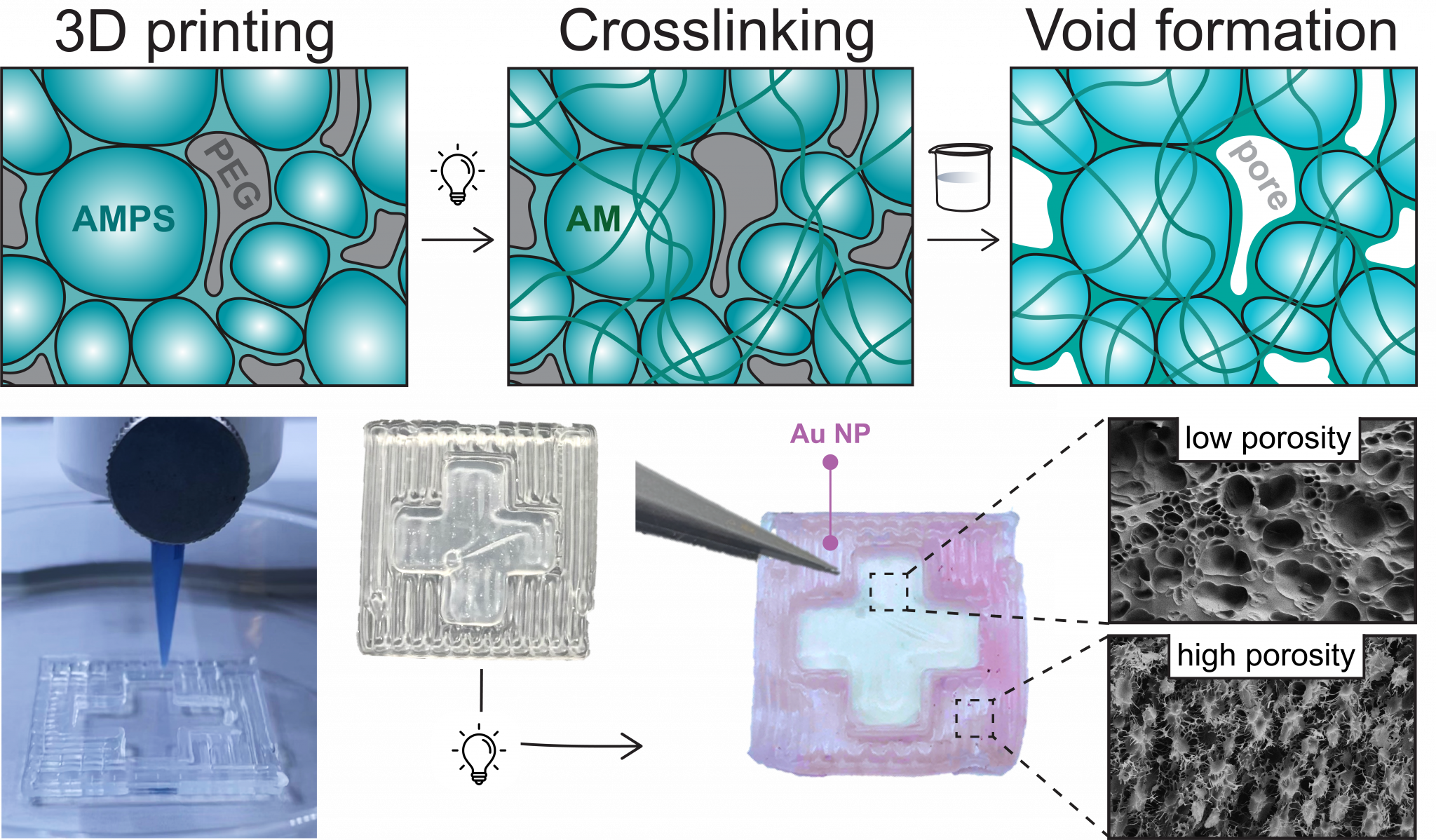
Does the Size of Microgels Influence the Toughness of Microgel Reinforced Hydrogels?
Microgels are frequently used to reinforce bulk hydrogels, yet, the influence of their size and inter-microgel distance is unknown, preventing a targeted design of microgel-reinforced hydrogel. This work fills this gap by demonstrating that the stiffness of microgel-reinforced bulk hydrogels is solely dependent on the microgel volume fraction, whereas their stress at break also depends on the microgel size and their toughness on the inter-microgel connectivity. These insights enable tuning the mechanical properties of 3D printable or castable microgel-reinforced hydrogels over a much wider range than was previously possible. This article is now published in Macromolecular Rapid Communications, and featured on the front cover.
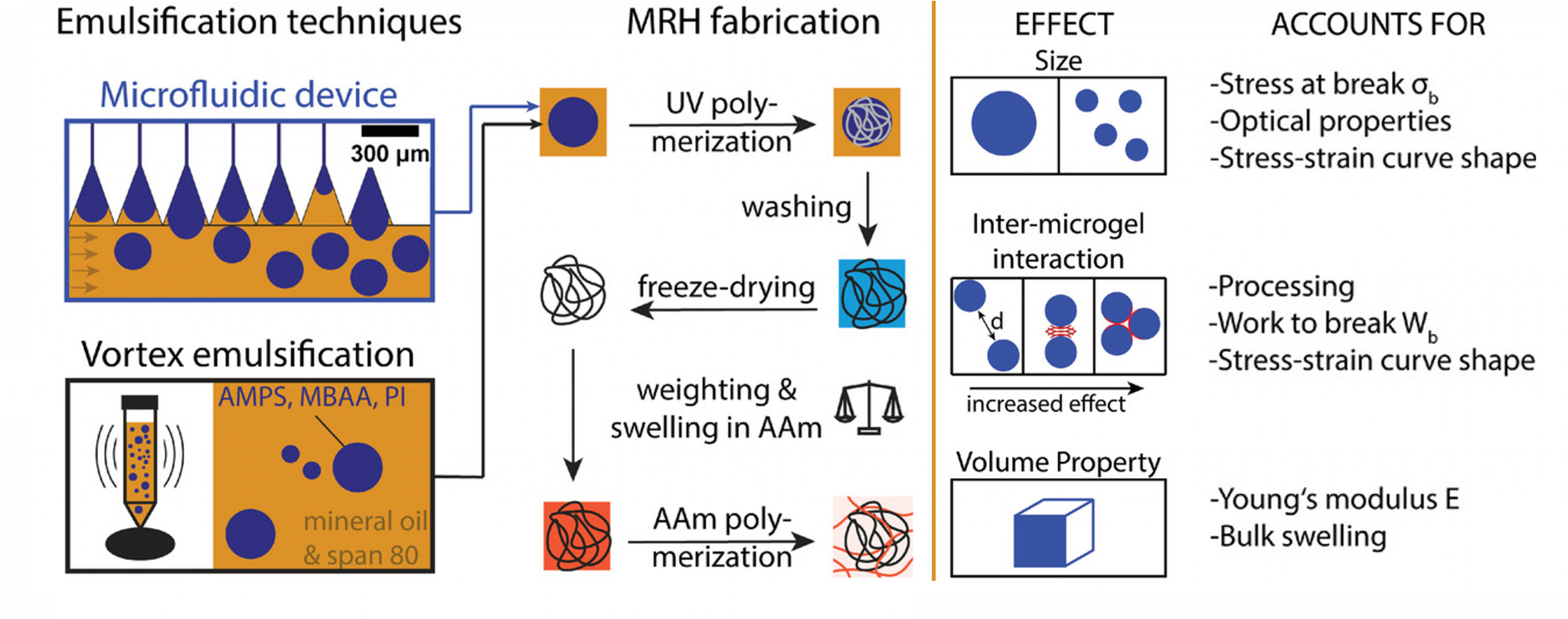
Recycling of Load-Bearing 3D Printable Double Network Granular Hydrogels
In this work, we demonstrate a strategy to 3D print recyclable load-bearing granular hydrogels. This is achieved by connecting jammed microgels with a percolating hydrogel that can be hydrolyzed under benign conditions and within hours at the end of the life of the material. Thereby, the material is disassembled into individual microgels that can be recovered, loaded with new reagents, and 3D printed into recycled materials that are even stiffer than the original material. Upon drying, this material is converted into a recyclable hard plastic. This work is now published in Small, and it is featured in Nature Research Highlights.
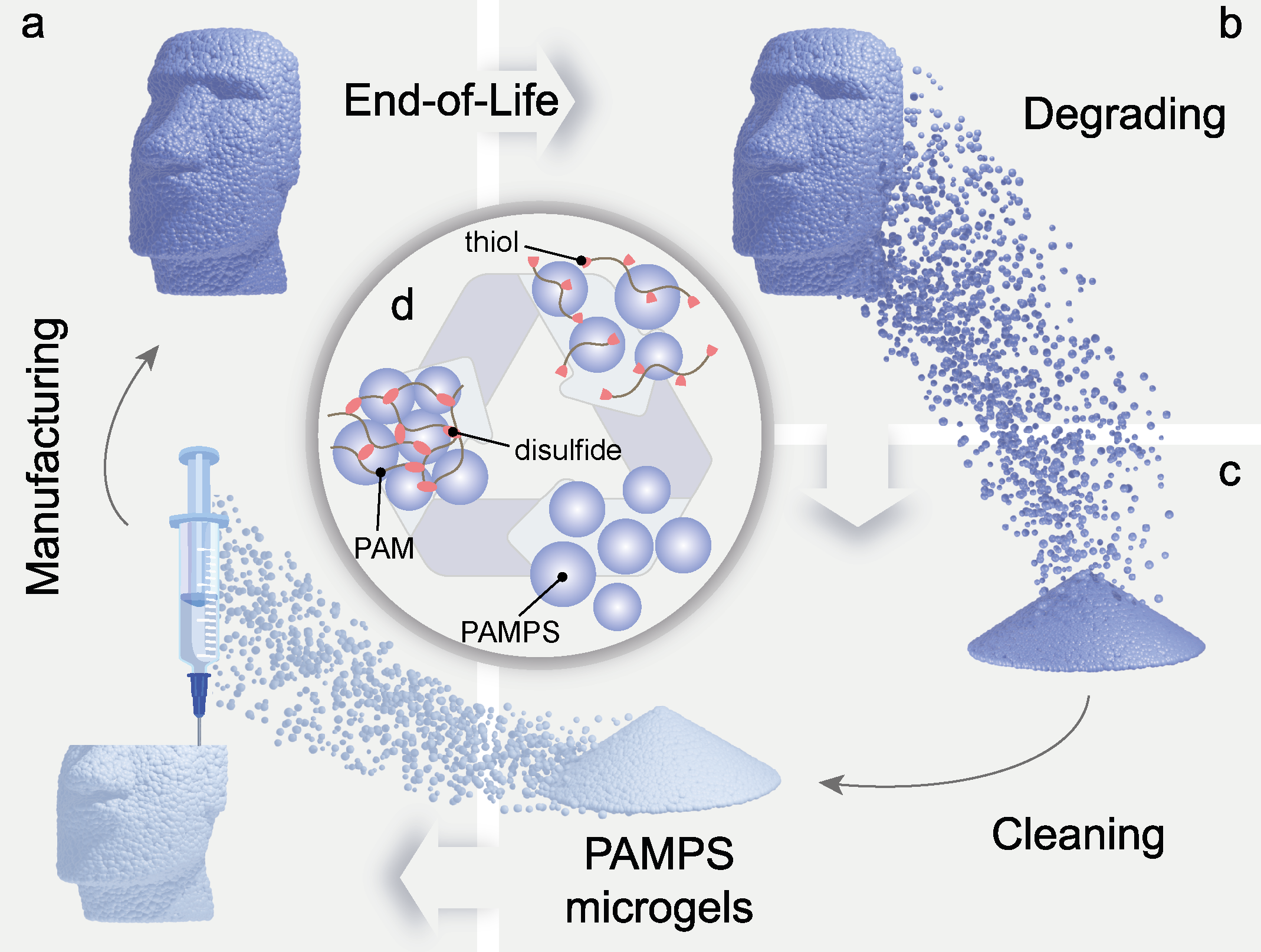
Load-bearing Hydrogels Ionically Reinforced through Competitive Ligand Exchanges
Inspired by nature, we introduce a competitive ligand-mediated approach to selectively and interchangeably reinforce metal-coordinated hydrogels. This is achieved by reinforcing carboxylate-containing hydrogels with Fe3+ ions. Key to achieving a homogeneous, predictable reinforcement of the hydrogels is the presence of weak complexation agents that delay the formation of metal-complexes within the hydrogels, thereby allowing a homogeneous distribution of the metal ions. Competitive ligand exchanges offer an additional advantage: they enable non-linear compositional changes that, for example, allow the formation of joints within these hydrogels. These features open up new possibilities to extend the field of use of metal-reinforced hydrogels to load-bearing applications that are omnipresent for example in soft robots and actuators. This work is now published in Biomaterials Science, and is featured in the Inside front cover.
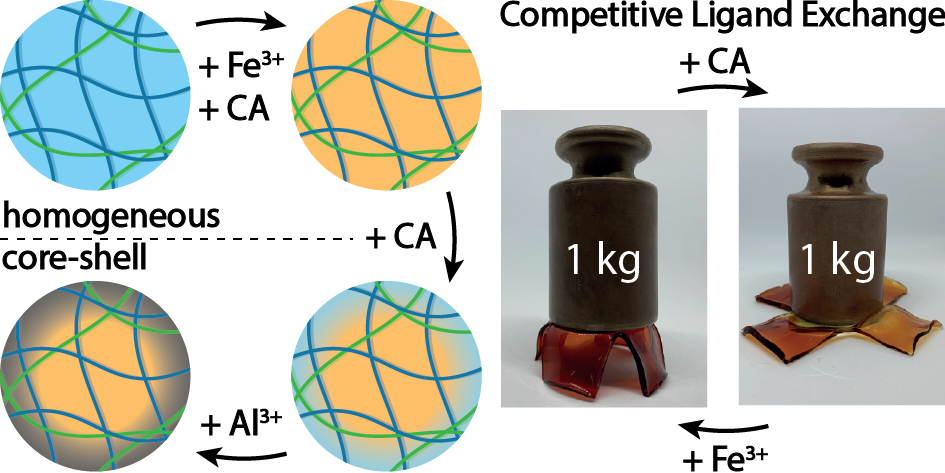
Shape Retaining Self-Healing Metal-Coordinated Hydrogels
We synthesized metal-coordinated hydrogels based on pyrogallol end-functionalized polymers that can be crosslinked by di- and trivalent ions. We demonstrated that the mechanical properties of these metal-coordinated hydrogels can be tuned over an unprecedented range by varying the ionic crosslinker. Small X-ray scattering (SAXS) analysis suggests that nm-sized precipitates form at the crosslinking sites. These nanoprecipitates bind to pyrogallols, thereby causing the gelation of the pyrogallol functionalized polymers and imparting shape-retaining and self-healing properties to them. This work published in the themed collection Nanoscale Emerging Investigators brings new insights in the crosslinking mechanism of metal-coordinated hydrogels and its implication on their mechanical properties.
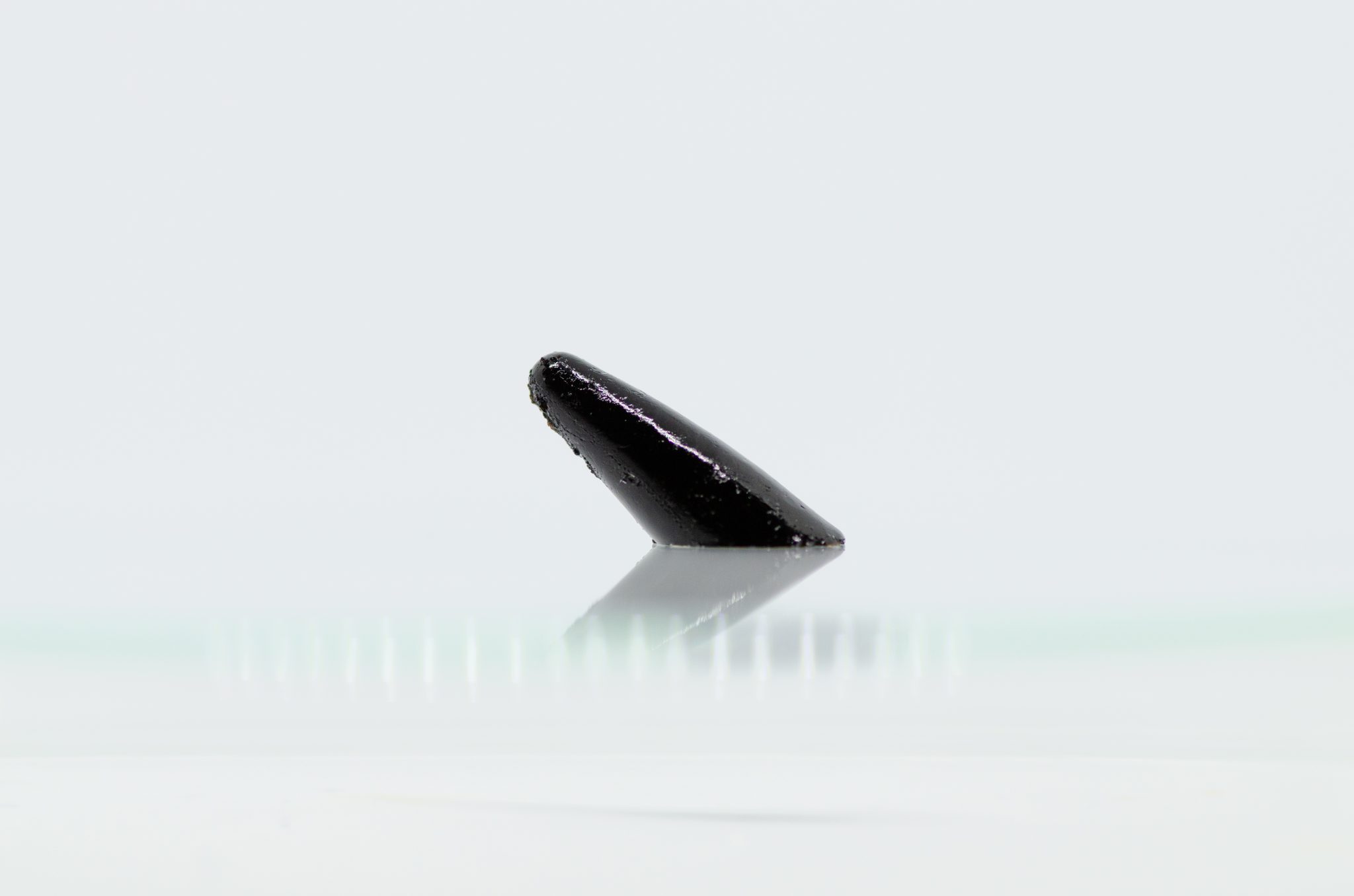
Controlling the Local Composition of Hydrogels Using Microfluidic Traps
Nature produces many soft materials, such as the mussel byssus or chameleon skin, with abruptly changing compositions that display a fascinating set of mechanical or optical properties. These outstanding properties of natural materials are strongly influenced by the non-linearly changing composition of the materials. To design soft materials possessing controlled abrupt changes in their composition, we introduce a microfluidic Hele-Shaw cell that encompasses different types of traps. Microfluidic traps are locations where the channel height locally and abruptly increases. If drops with diameters that exceed the height of the Hele-Shaw cells are injected into the trapping device, they are deformed and hence, can reduce their surface area and therefore surface energy by relaxing into a trap. This reduction in surface energy results in a trapping force. We demonstrate that the trapping force depends on the dimensions and in-plane geometries of the traps. Taking advantage of these insights, we immobilize two different batches of drops at well-defined locations, as shown in Figure 1. Trapped drops are then converted into microparticles before the Hele-Shaw cell is filled with a matrix precursor solution. This solution is solidified by polymerizing the reagents contained in it, resulting in thin composite hydrogel sheets possessing locally varying compositions. This work has been published in a themed collection: Lab on a Chip Recent HOT Articles.
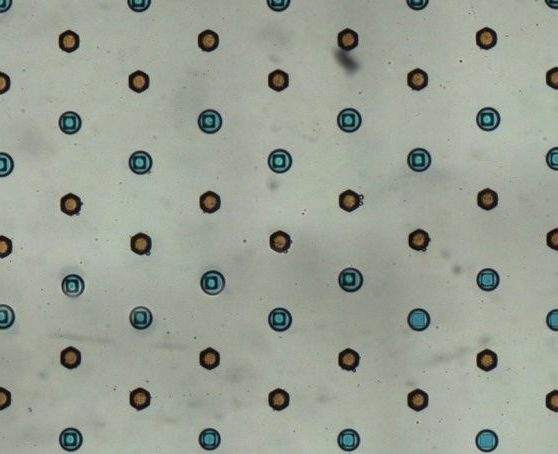
3D Printing of Strong Double Network Granular Hydrogels
Soft natural materials possess locally varying compositions and structures that are well-defined over many length scales. By contrast, synthetic hydrogels typically have an ill-defined microstructure and their composition is most often homogeneous. We introduce a novel type of soft materials, double network granular hydrogels (DNGHs), that are strong and tough such that they can bear pressures up to 1.2 MPa even under tension. These materials can be 3D printed into macroscopic objects, thereby opening up new possibilities for their use in load-bearing applications including soft actuators and robots. The DNGHs are fabricated from microgels that are swollen in a monomer-containing solution before they are jammed to enable their 3D printing. After the microgels have been 3D printed into the desired macroscopic structures, they are post-cured by converting the monomers contained in them into a percolating network, yielding a solid DNGH. The resulting DNGHs display the highest stiffness that has been reported for 3D-printed hydrogels thus far. We exploit this feature by building shape-morphing objects from them, lifting weights with them, or to reversibly compressing them to demonstrate their potential as dampers. This work has been published in Advanced Functional Materials.
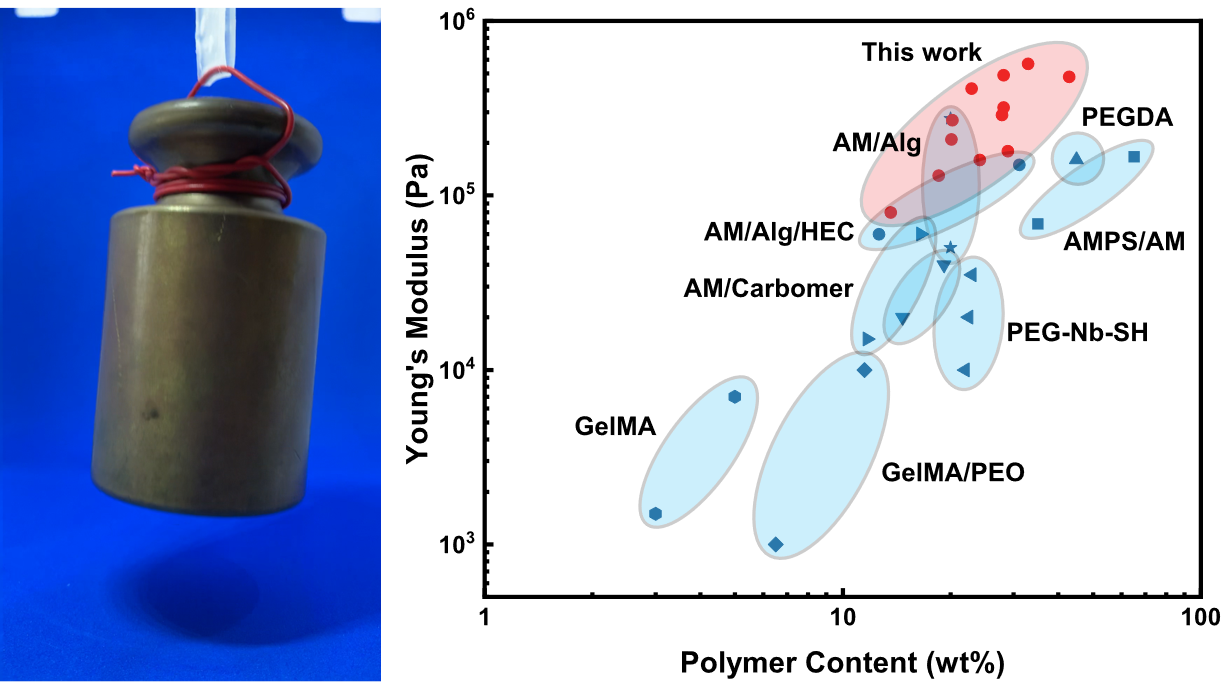
Fabrication of Granular Hydrogels
Many natural hydrogels have well-defined structures on different length scales and possess excellent mechanical properties. For example, the mussel byssus is a hydrogel-based, soft material that displays an exceptional combination of strength and toughness. In addition, this byssus can adhere bind to solid surfaces, such as rocks and ships, such that mussels remain attached even during stormy weather when high waves are impacting these surfaces. Inspired by nature, we are studying how the structure and local composition of hydrogels influence their mechanical properties. To achieve this goal, we are developing microfluidic tools to control the arrangement of drops before we convert them into microparticles that are linked to each other to form granular hydrogels. We study how the structure and local composition of these granular hydrogels influences their mechanical properties intending to produce hydrogels that display mechanical properties that are similar or even superior to those of the mussel byssus. This work is published in Langmuir.