AZ 10XT-20 is a photoresist from the AZ 10XT family (which replaces the old AZ9200 line of products) with a thickness range from 2um to 4um. It is the standard resist choice for dry etching applications requiring steep sidewalls. Transfer of critical dimensions from the mask/design is not accurate and will require the introduction of CD biases (~800nm).
- Coating Tools : ACS 200; Sawatec SM-200
- Thickness range [µm]: 2 … 4
- Minimum CD / typical aspect ratio: ~ 2um / AR ~ 2:1
- Substrate topography: Medium
- Recommended for: Ion beam etching (IBE), dry etching (depth <50um & vertical sidewalls)
Process in CMi
! Cleanroom humidity warning !
Control of the relative humidity (RH) in photolithography zones is extremely critical. Stable and reproducible photolithography is expected within 38% to 48% RH range.
- In case of low RH (< 38%), the resist sensitivity and development rate decreases. It is then recommended to increase the recommended exposure doses.
- In case of high RH (> 48%), the resist adhesion decreases. It is then recommended to do an additional bake (>10 minutes @ 150°C) before loading the wafers in the HMDS or coating equipment.
Wafer surface preparation
Usually adhesion of photoresist on inorganic materials is poor resulting in losses of fine structures after development. To solve the issue, silicon wafers are generally treated using the HMDS vapor prime treatment before spincoating the photoresist. Details about the HMDS process and control can be found here: link
Assuming wafers with a clean surface free of organic contamination, the best adhesion will be obtained with the surface preparation recommended in the table:
Surface material (larger area) | Vapor HMDS | Plasma O2 | Thermal dehydratation |
---|---|---|---|
Si | √√ | √ | √ |
SiO2, fused silica, SiN, Si3N4 | √√ | √ | √ |
Float glass, pyrex | √ | √√ | √ |
Metals: Al, Au, Pt, Ti | … | √ | √√ |
Metals: Ag, Cu, Cr, Fe | … | X | √√ |
III/V semiconductors (GaN, GaAs) | … | X | √√ |
Legend: √√ Strongly recommended / √ Alternative process / … Not effective / X May affect or destroy underlaying material
Spincoating
The AZ 10XT-20 spincurve is shown below, as well as process details for both automatic and manual coating.
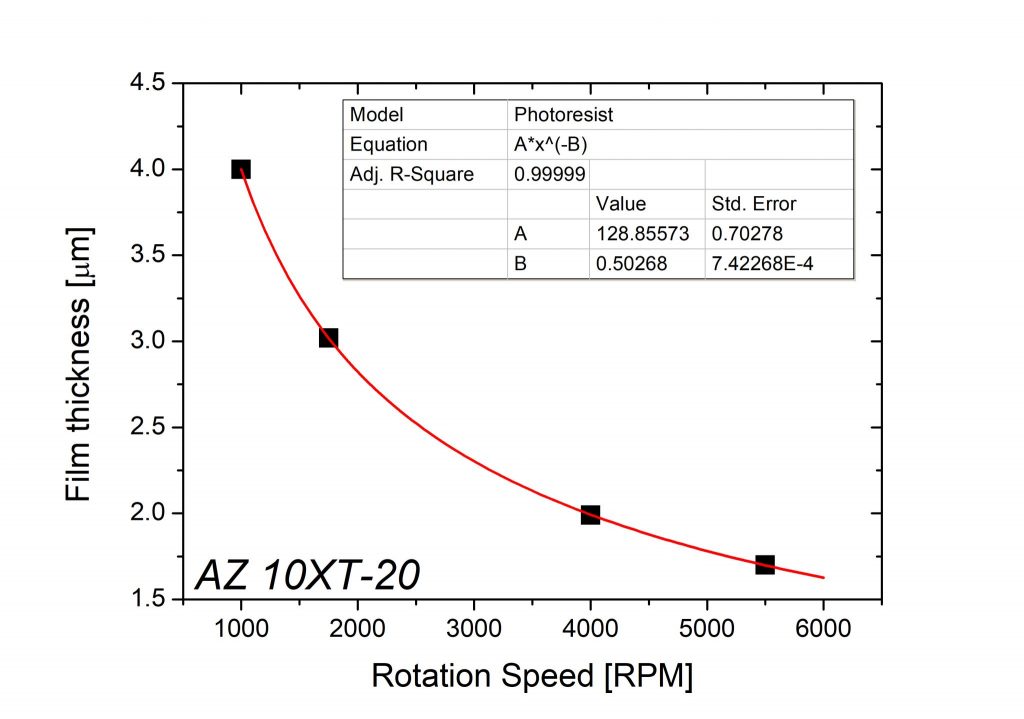
Available thicknesses: 2 um / 3 um / 4 um
Spin speed [rpm] | Softbake time [mm:ss] | PR thickness [µm] |
---|---|---|
3950 | 02:00 | 2 |
1700 | 02:30 | 3 |
1000 | 02:30 | 4 |
Spin time is adjusted with the rotation speed. Softbake is performed at minimum proximity. Softbake temperature is 110°C for all options.
Available options:
- HMDS / EC (edge clean)
- Dehydrate / EC
- HMDS / EBR (edge bead removal)
- Dehydrate / EBR
- Find the spin-coating speed “XXXX” [RPM] matching your target thickness from the AZ 10XT-20 spincurve.
- When coating on wafers, use the STD_”XXXX” recipe, which includes a 500 RPM spreading step and 40 seconds of main coating step.
- When coating on small chips, use the CHIP_”XXXX” recipe, which includes 40 seconds of main coating step and a short acceleration at the end to reduce edge bead effects.
- Softbake temperature: 105°C
- Softbake time: 90” + 20”/um
Exposure
The following table lists the recommend dose “to clear” for AZ 10XT-20 coated on silicon wafers. It is recommended to perform a contrast curve / exposure matrix calibration for wafers other than silicon.
Illumination: | Broadband* | i-line (355-365 nm) | h-line (405 nm) |
---|---|---|---|
Equipment: | MABA6, MA6 Gen3 (no filter) | VPG 200, MA6 Gen3 (filter), MJB4 | MLA 150 |
PR thickness [µm] | Dose [mJ/cm2]+ | Dose [mJ/cm2]++ | Dose [mJ/cm2]+++ |
2 | 190 | 175 | Refer to Resist Tables |
3 | 240 | 220 | |
4 | 300 | 270 |
* Mercury Lamp, Mask Aligner with UV400 configuration & no filter / + Based on intensity readings from Süss optometer broadband CCD / ++ Based on intensity readings from Süss optometer i-line CCD / +++ Based on MLA150 internal dose measurements
Development
The recommended developer for AZ 10XT is AZ 400K (diluted in water 1:3.5), an inorganic solution based upon KOH. Development with AZ 400K will result in a sharper edge profile.
Development sequences for AZ 10XT-07 are listed below:
Recipe name | PR thickness [µm] | Total contact time [s] |
---|---|---|
D4_N_10XT_2u_PUD |
2
|
93
|
D4_N_10XT_3u_PUD |
3
|
110
|
D4_N_10XT_4u_PUD |
4
|
130
|
The development combines spray and puddle methods with intermediates spin-clean steps. Hardbake is performed at 110°C for 90 seconds with a 50µm proximity gap.
- Recommended developer: AZ 400K diluted 1 to 3.5 DI
- Development time: 45″/um
- Rinse: H2O 1min
IMPORTANT:
After development, it is mandatory for wafers to go through an additional rinsing step with DI water to avoid backside contamination and damage on equipments (chuck in etcher) in further processing steps. The water baths of the following wet benches can be used free of charge (5 min. billing delay after login):
- Z01 – Plade “Solvent” wet bench
- Z02 – UFT “Resist” wet bench