Electra 92 is a protective conductive coating for ebeam resists (PMMA, ZEP, CSAR, HSQ). It can be used as a top coating layer for the dissipation of ebeam charges on partially insulating substrates.
WARNING: Electra 92 is not a substitute for a properly deposited conductive metal layer on a fully insulating substrate and should not be used as such. Damage to the ebeam lithography tool can result.
The power delivered by a 100kV, 100nA electron beam of the e-beam litho machine is one million times higher than a power delivered by a 1kV (or less), 10pA beam of SEM (typical imaging conditions used for charging substrates). While Electra 92 will certainly help to dissipate some of the overall charge delivered, depending on the pattern layout and density, dose chosen, and other factors, it may not be able to remove all of the rapidly built-up electrical charge.
It is not only an electrical charge that builds up during the ebeam exposure. Heat does also. Poorly electrically conductive substrates tend to also be poor conductors of heat, and the rapidly built-up temperature can under certain circumstances exceed the melting temperature of the resist. This can lead to droplets of resist being ejected from the substrate. The objective lens of the ebeam machine is only 4cm away from the surface of the substrate…. Metal coating normally prevents the resist droplets from flying out. Electra 92 is however a polymer, with a melting point even below many of the resists, and it will not offer any protection against the resist heating and possible particle defects creation.
Last but not least, the vast majority of non-conductive substrates are transparent (glass, sapphire, CaF2, diamond, lithium niobate, etc…). The laser interferometer in the ebeam tool requires an opaque and reflective surface of the substrate in order to measure its height properly during the exposure. Electra 92 coating, while black in color, is not opaque enough to provide such surface, and the height measurements will fail on clear substrates coated with resist and Electra 92 only.
Recommended use
Electra 92 is recommended for substrates, where the bulk is opaque and conductive, and only the top layers (oxide, nitride, and resist) are electrically insulating. It can also be successfully used with insulating substrates coated with opaque metal layer, the resist being coated on the top of the metal, and Electra 92 deposited as the top most layer (typical example of this scheme is mask writing). In these cases, using Electra 92 does help reduce charging and associated image placement errors.
Electra 92 can also be used as a sole coating for insulating substrates for SEM imaging, where the power in the electron beam is lower. The advantage over metal layer here is the ease of processing. The disadvantage is that the Electra 92 coating is thicker than the typical metal coating, thus reducing the resolution limit for observable features.
Polarity
Electra 92 can be used with both positive and negative tone resists.
Doses
Coating with Electra 92 should not alter significantly the exposure dose of the underlying ebeam resist. As usual, everything is a matter of specifications, and users in need of very precise image size (CD) control should perform their dose test exposures with the exact coating stack they intend to use for the actual fabrication. Electra 92 itself is not sensitive to light or electron radiation.
Resolution
Resolution of the underlying resist should not be significantly affected, but again, everything is a matter of specification and users who are pushing the limits of their process window should perform their dose test exposures with the exact same coating stack they plan to use for fabrication of their actual designs.
Chemical capabilities
Electra 92 is a polyanilin derivative dissolved in water and IPA. It is easily removed after ebeam exposure by rinse with water. Electra 92 exhibits long term stability, and as such, it is a good alternative to other similar products in the market (Aquasave, Espacer).
Quick process
The bottle with Electra 92 is stored in the fridge in zone 7. It should be returned there immediately after each use.
Step | Description | Program/Parameters |
---|---|---|
1 | resist coating/baking/drying | follow quick process for each respective type of resist |
2 | substrate cooling | 1min |
3 | Electra 92 coating | recommended thickness: 40nm at 4000rpm, or see curve below |
4 | Electra 92 drying | 5min air drying at room temperature, or (optional) 2min tempering at 90°C on the hotplate |
5 | resist exposure | dose dependent on the underlying resist |
6 | Electra 92 rinsing off | 1min DI water rinse on the water wetbench |
7 | resist development | follow quick process for each respective type of resist |
The electrical conductivity of the Electra 92 depends on the coating thickness. Thicker coating will exhibit a higher conductivity. At 60nm thickness the conductivity will be 1.2 S/m, at 90nm it will be 3 S/m. These values further improve once the water gets removed from the coating, either by hot plate tempering, or simply by pumping in a vacuum of the ebeam tool. Coating with Electra should be done close to the exposure time, the humidity in the cleanroom air for prolonged time results in water re-absorption and subsequent decrease of conductivity. Be careful with the use of hotplate. Temperatures above 165 °C destroy the polyaniline irreversibly and no conductivity is observed any more.
Spin curve
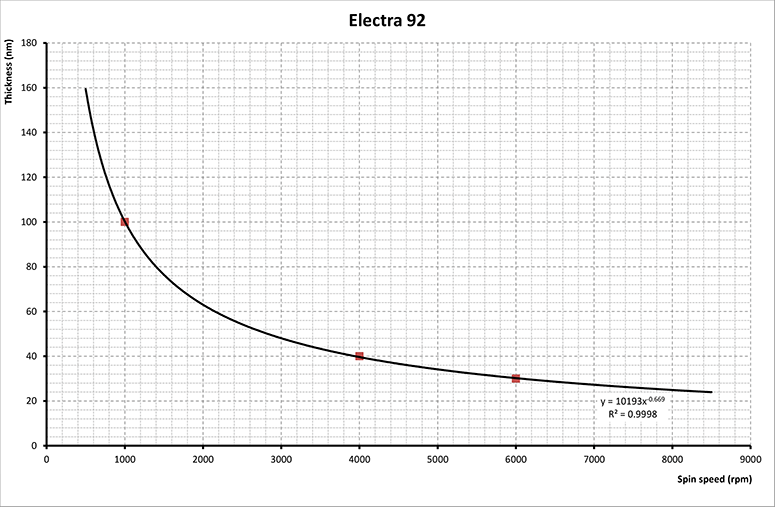