PMMA (poly methyl methacrylate) and MMA (8.5) (methyl methacrylate) are positive ebeam resists consisting of long polymer chain of carbon atoms which comes in various molecular weights. The two standard molecular weights of PMMA which we use here are of 495K and 950K. The standard use for PMMA/PMMA and MMA/PMMA bilayers in EBL is for lift-off of metallic structures.
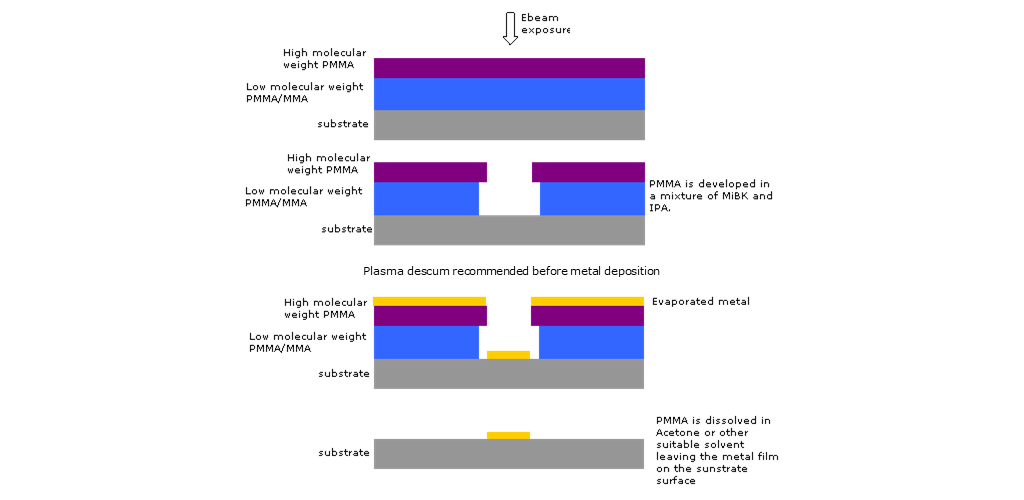
For good lift-off you need an undercut resist profile to avoid coating the sidewall of the resist when you evaporate metal. This is particularly true for high beam energies (100kV) where the sidewall profile is normally extremely vertical. The PMMA/MMA bilayer gives a larger undercut profile than PMMA/PMMA. This larger undercut is good for liftoff, but fails to work for small dense features as the undercut can cause the central MMA structure to collapse. A good rule of thumb is that you should the lower layer of resist should be 2x the thickness of the metal you want to deposit.
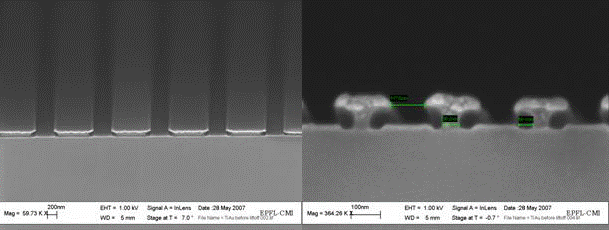
Metalized with 15nm Ti and 45 Au.
Right image: 100nm lines after development of MMA/PMMA bilayer.
Metalized with 5nm Ti and 15 Au.
Polarity
Positive
Exposure doses
For large structures (above 1µm) the clearing dose at 100kV is around 600µC/cm2, for small isolated structures it can go up to about 3000µC/cm2.
Resolution
The best resolution attainable with PMMA/PMMA bilayer is around 10nm using a well focused beam and a very good process. < 20nm should be possible regularly.
Chemical capabilities
- PMMA/MMA is resistant to water, IPA, methanol, HCl, dilute NH3, dilute H2SO4, dilute HF for short periods, H3PO4 for short periods, dilute HNO3 importantly it’s also resistant to TMAH based developers.
- PMMA/MMA is attacked by acetone, chlorobenzene, concentrated NH3, HF (after more than a few seconds, depending on strength). More generally it is a poor dry etch mask.
Quick process
Before processing choose 2 beakers into the MMA/PMMA tray and rinse them with a small amount of developer for the fist and IPA for the 2nd.
Step | Description | Program/Parameters |
---|---|---|
1 | substrate dehydration | 5min of O2 plasma at high power or alternatively 5mins at 180°C on the hotplate |
2 | substrate cooling | 1min |
3 | MMA coating | ~2x the final metal thickness on the spin coater |
4 | MMA baking | 5mins at 180°C on the hotplate |
5 | substrate cooling | 1min |
6 | PMMA 495 coating | on the spin coater |
7 | PMMA 495 baking | 5min at 180°C on the hotplate |
8 | resist exposure | on the ebeam tool |
9 | resist development | 1min into MiBK:IPA 1:3 on the metalic wetbench |
10 | substrate rinsing and drying | 1min rinse with IPA and dry with nitrogen |
When you have finish rinse the beakers with IPA (into the solvent recuperation tray) and put them into the MMA/PMMA recuperation tray (which is on the wet bench).
Spin curves
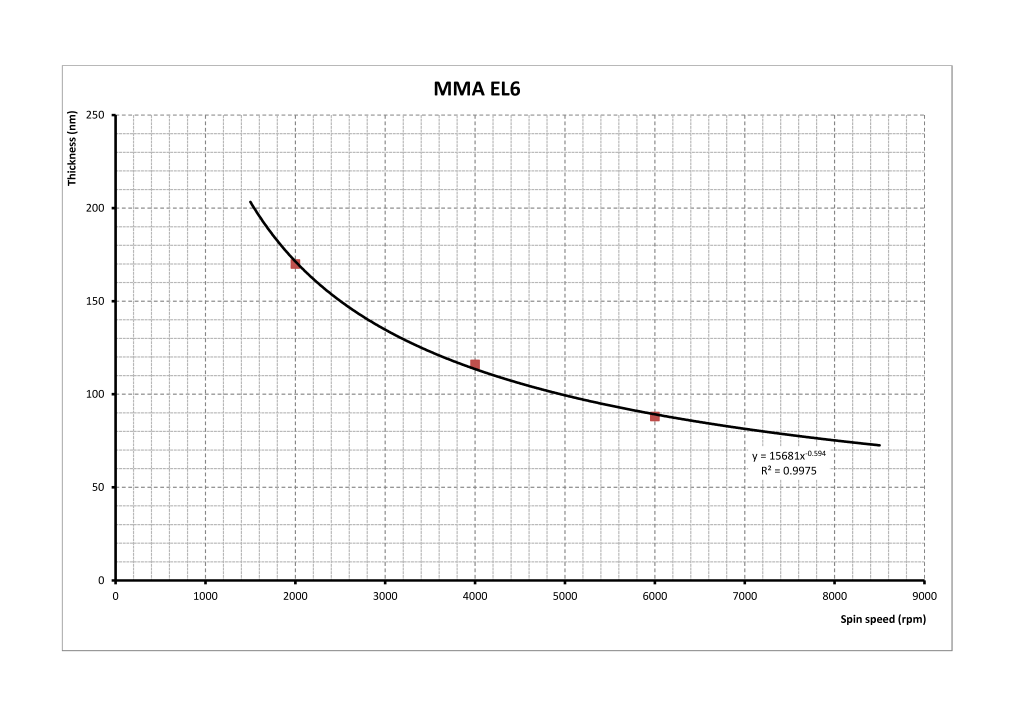
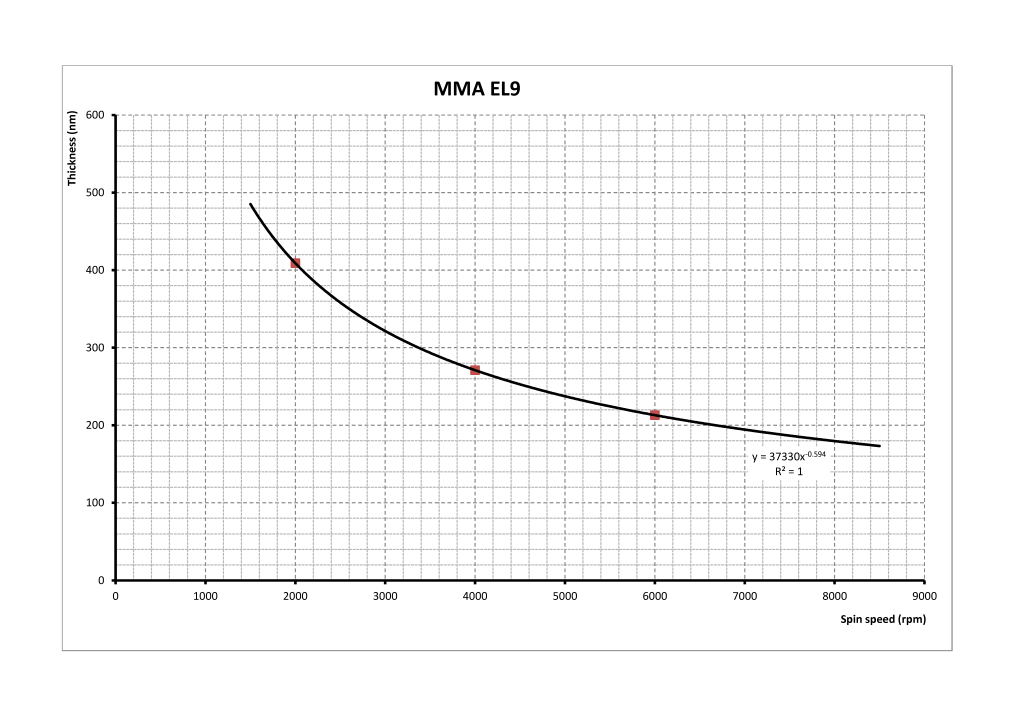
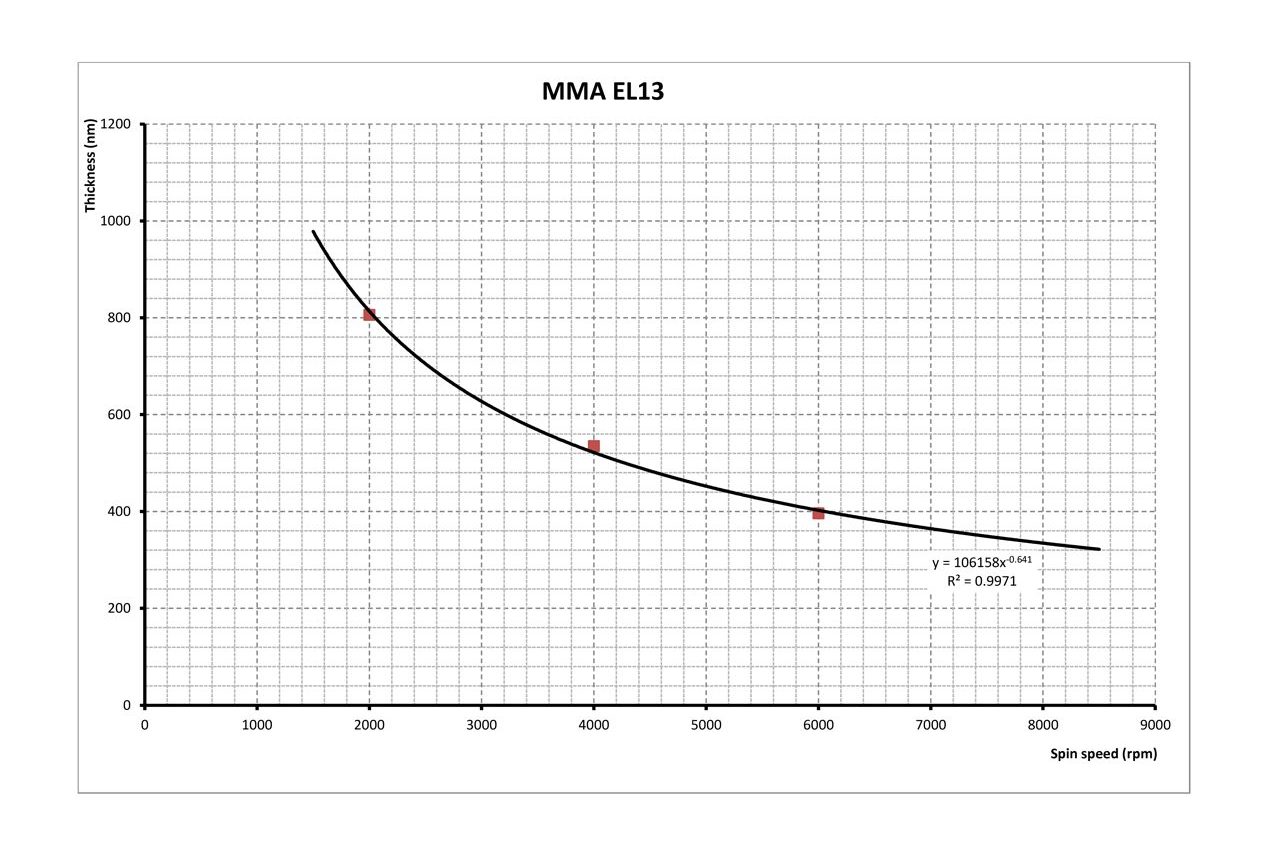
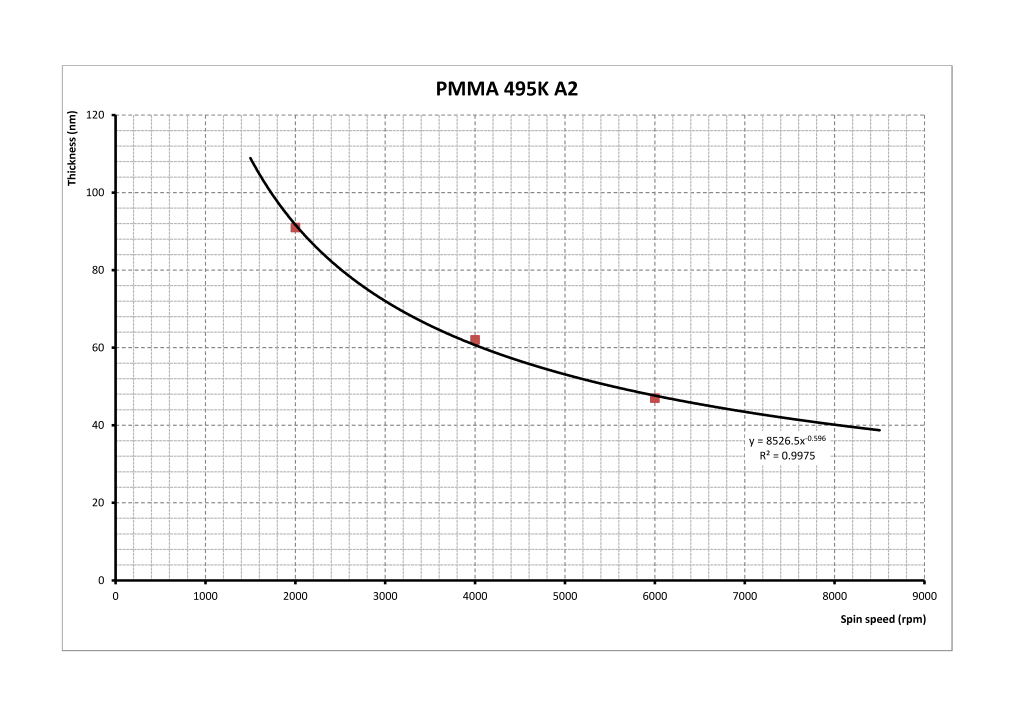
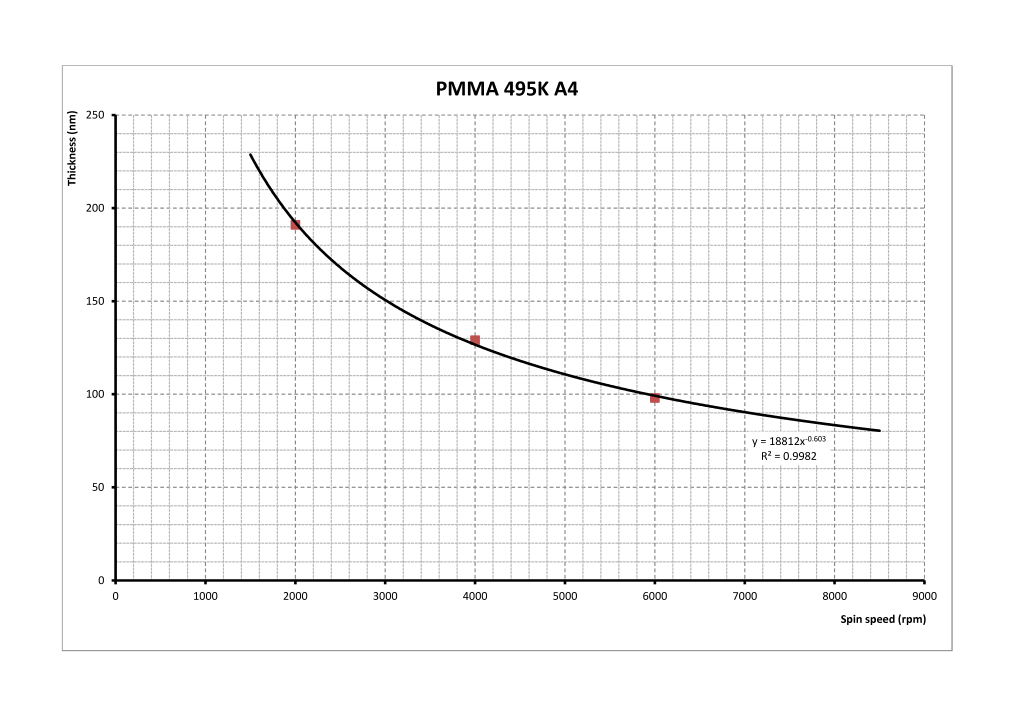
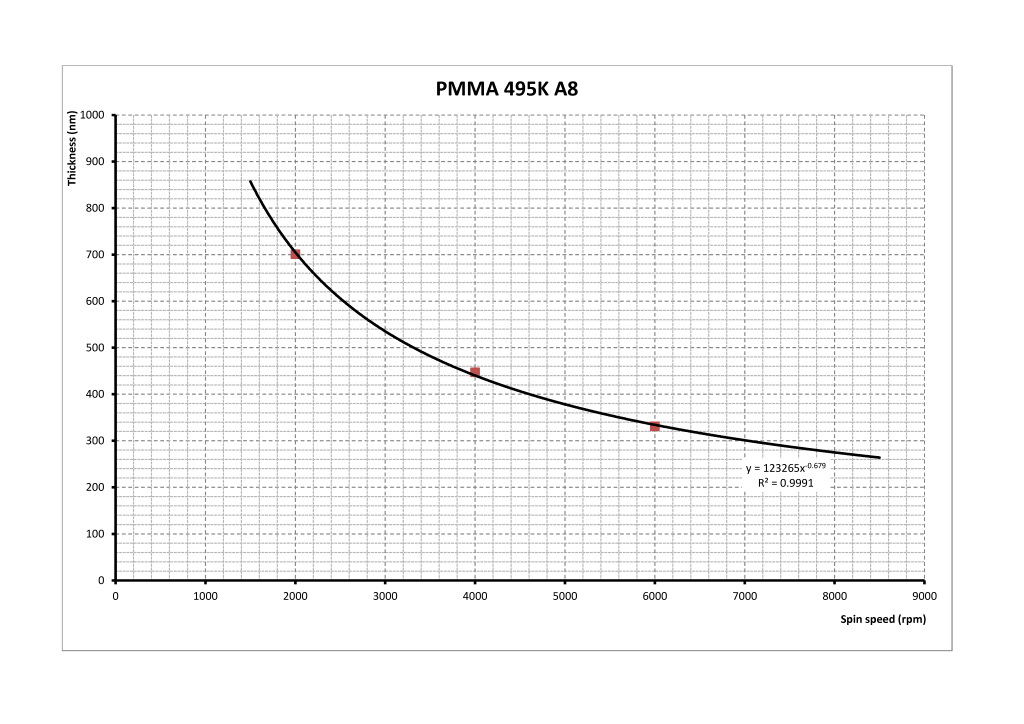
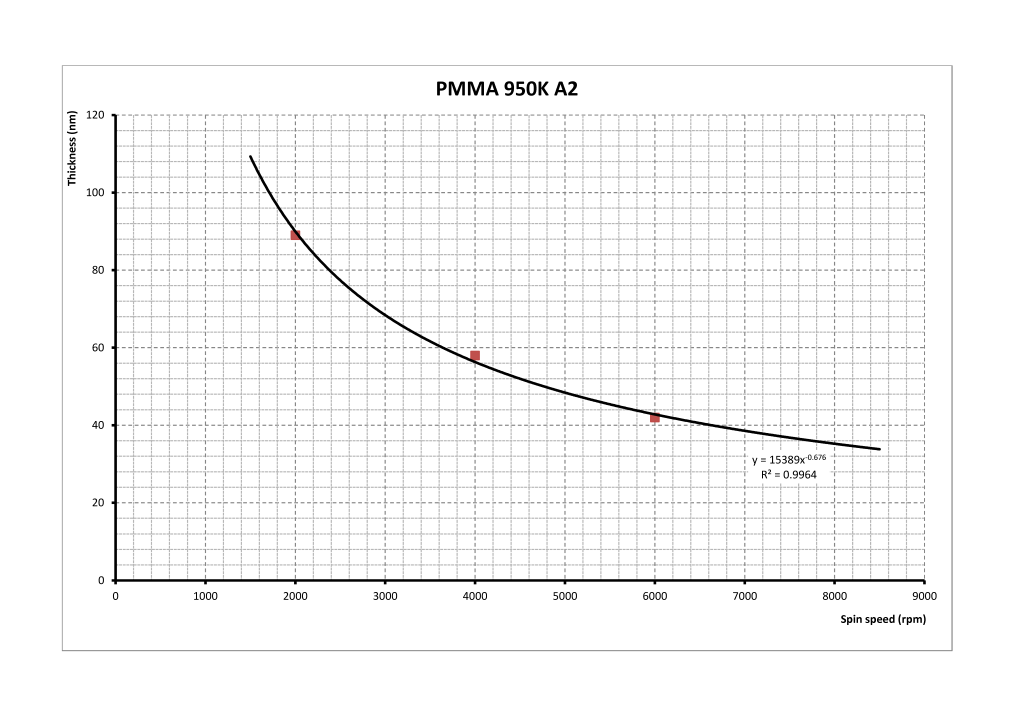
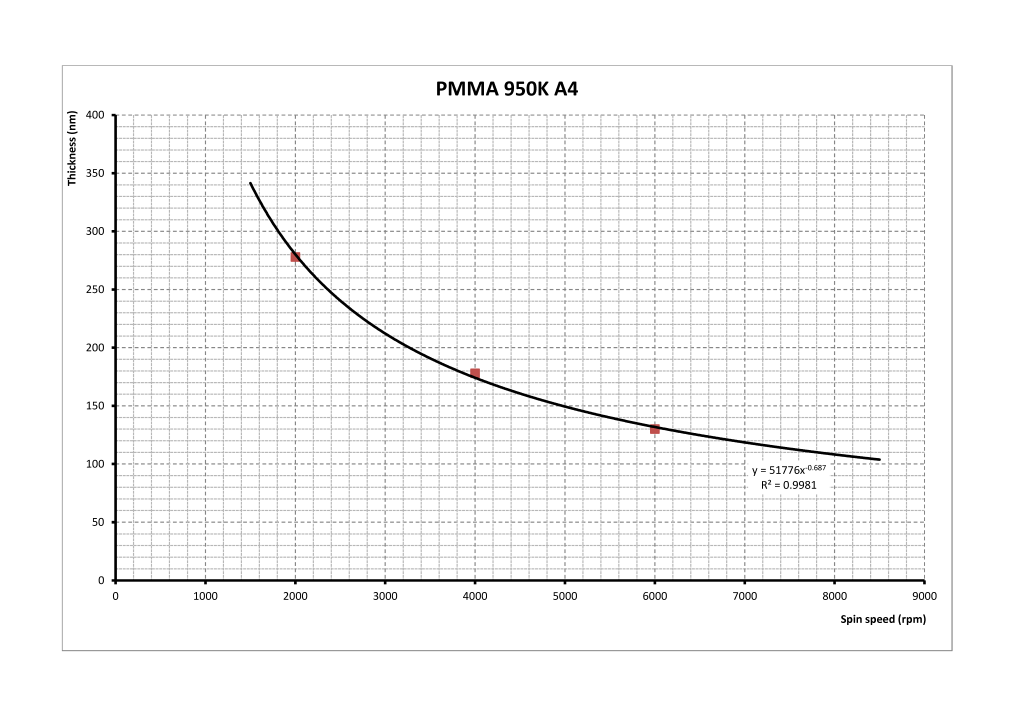
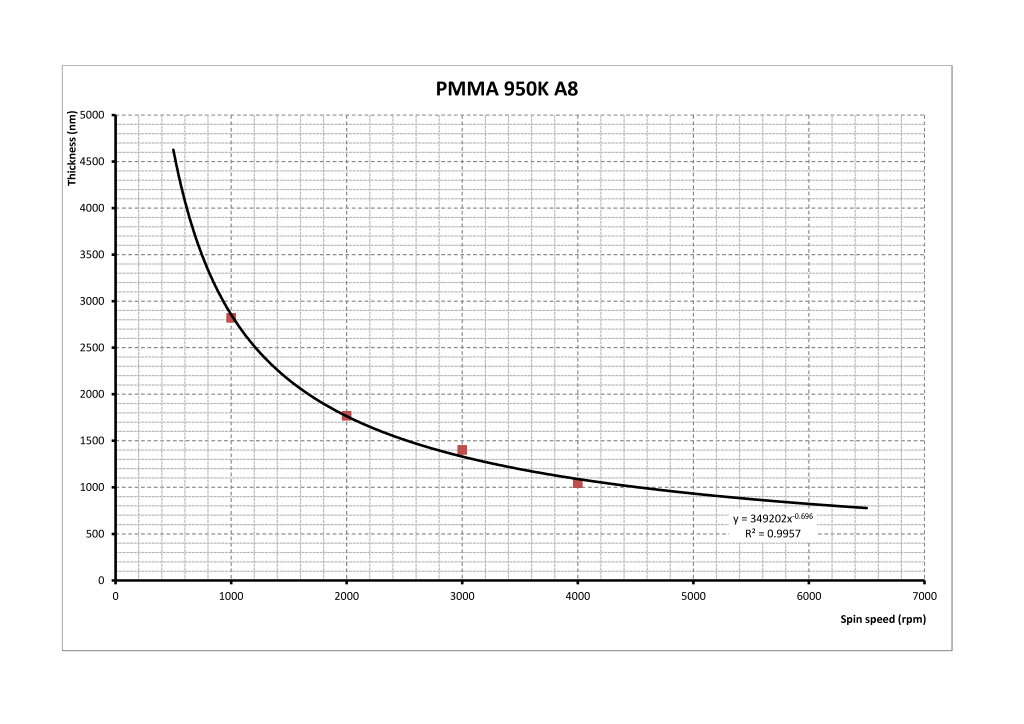