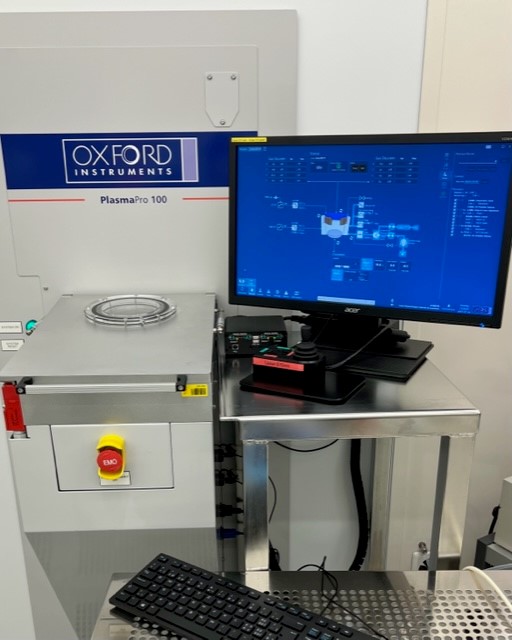
Restrictions and Precautions
Materials such as pyrex, floatglass or any “fancy” metal (Cu, Cr, Au, Fe, Ag…) require CMi staff agreement BEFOREHAND
1. Maximum allowed booking per person between 9am and 5pm is 2 hours. It is still possible to get 4 consecutive hours from 7am to 11am or from 3pm to 7pm.
2. Reservation names must correspond to operators.
I. Tool description
Oxford PlasmaPro100 Cobra offers large range materials etching possibility.
It primarily targets etching of metals (Al & Ti Alloys) with chlorine chemistry, but it can also etch silicon and its insulators (SiO2, Si3N4 and SiC) with fluorine/carbonate chemistry and some polymers with oxygen chemistry.
Technological advantages of this equipment are the followings:
- Full wafer 100mm with fast pump/vent loading track
- High density plasma of ICP (Inductively Coupled Plasma ) type
- An electrostatic clamping and biasing chuck controlled in temperature (20°C to 60°C)
- 8 digital Mass Flow Controllers (MFC) for the following gas : O2 (100sccm), O2 (10sccm), SF6, CF4, BCl3, Ar, Cl2 and HBr
- Laser reflectometry/interferometry end-point-detection
- Optical Emission Spectroscopy (EOS) end-point-detection
II. Standard processes
Material to etch Al*, Ti, TiN | Process name Al_Ti_TiN_etch | Mask PR | Etch rate (nm/min) Al 340 Ti 250 PR 300 | Chemistry Cl2/BCl3 |
Material to etch Al*, Ti, TiN | Process name Al_etch_w-breakthrough | Mask PR | Etch rate (nm/min) Al 510 PR 250 SiO2 50 | Chemistry BCl3 (BT) Cl2 (main) |
Material to etch Si | Process name Si_etch | Mask PR SiO2 | Etch rate (nm/min) Si 370 PR 430 BARC DUV42P 120 | Chemistry Cl2 |
Material to etch SiO2, Si3N4 | Process name SiO2_Si3N4_etch | Mask PR | Etch rate (nm/min) SiO2 175 Si 220 PR 332 BARC DUV42P 120 | Chemistry CF4 |
Material to etch SiO2, Si3N4 | Process name SiO2_Si3N4_RIE | Mask PR | Etch rate (nm/min) SiO2 45 Si 55 PR 25 BARC DUV42P 50 | Chemistry CF4/Ar |
Material to etch Polyimide | Process name PI_etch_O2-Ar | Mask SiO2 | Etch rate (nm/min) PI 2’550 SiO2 20 | Chemistry O2/Ar |
Material to etch Al2O3 | Process name Sapphire_etch | Mask PR | Etch rate (nm/min) Al2O3 ALD 50 Al2O3 Sputtered 90 PR 415 | Chemistry Cl2/BCl3/Ar |
*Aluminum post-etch treatment
After Aluminum etch, corrosion is an issue because of trapped Chlorine at patterns’ sidewalls: HCl creation will locally initiate as soon as the sample is at atmosphere and in contact with ambient humidity.
In order to avoid slow corrosion of the Aluminum, straight after loadlock vent, get with no delay the wafers rinsed in a high volume of DI water (cascade or trickle tank on any of the benches of Zone2). This will force create HCl but will dilute/rinse it right away from the wafers.
Then proceed as soon as possible with full removal of the resist mask.
1. Start with a short high power oxygen plasma using the Tepla GiGAbatch.
2. Then do a wet remover treatment using the Ultrafab wetbench.
3. If necessary, remove final residues with the Tepla GiGAbatch again.